I t is two years since CM tested a random sample
Page 53
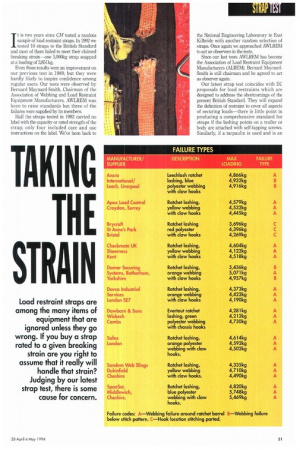
Page 54
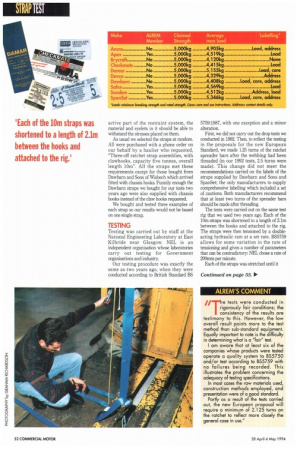
Page 57
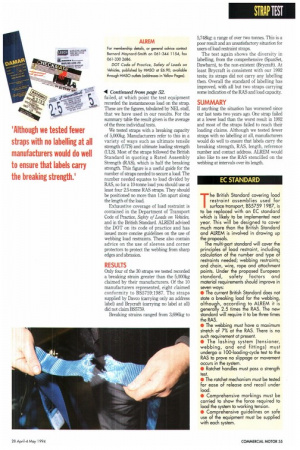
If you've noticed an error in this article please click here to report it so we can fix it.
of load restraint straps. In 1992 we tested 10 straps to the British Standard and most of them failed to meet their claimed breaking strain-one 5,000kg strap snapped at a loading of 3,851kg.
Even those results were an improvement on our previous test in 1989, but they were hardly likely to inspire confidence among regular users. Our tests were observed by Bernard Maynard-Smith, Chairman of the Association of Webbing and Load Restraint Equipment Manufacturers. AWLREM was keen to raise standards but three of the failures were supplied by its members.
Half the straps tested in 1992 carried no label with the capacity or rated strength of the strap; only four included care and use instructions on the label. We've been back to the National Engineering Laboratory in East Kilbride with another random selection of straps. Once again we approached AWLREM to act as observers in the tests.
Since our last tests AWLREM has become the Association of Load Restraint Equipment Manufacturers (ALREM). Bernard MaynardSmith is still chairman and he agreed to act as observer again.
Our latest strap test coincides with EC proposals for load restraints which are designed to address the shortcomings of the present British Standard. They will expand the definition of restraint to cover all aspects of securing loads-there is little point in producing a comprehensive standard for straps if the lashing points on a trailer or body are attached with self-tapping screws. Similarly, if a tarpaulin is used and is an active part of the restraint system, the material and eyelets in it should be able to withstand the stresses placed on them.
As usual we selected the straps at random. All were purchased with a phone order on our behalf by a haulier who requested, "Three-off ratchet strap assemblies, with clawhooks, capacity five tonnes, overall length lOna". All the straps met these requirements except for those bought from Dawbarn and Sons of Wisbech which arrived fitted with chassis hooks. Funnily enough the Dawbarn straps we bought for our tests two years ago were also supplied with chassis hooks instead of the claw hooks requested We bought and tested three examples of each strap so our results would not be based on one single strap.
TESTING
Testing was carried out by staff at the National Engineering Laboratory at East Kilbride near Glasgow. NEL is an independent organisation whose laboratories carry out testing for Government organisations and industry Our testing procedure was exactly the same as two years ago, when they were conducted according to British Standard BS 5759:1987, with one exception and a minor alteration.
First, we did not carry out the drop tests we conducted in 1992. Then, to reflect the testing in the proposals for the new European Standard, we made 1.25 turns of the ratchet spreader bars after the webbing had been threaded (in our 1992 tests, 2.5 turns were made). This change did not meet the recommendations carried on the labels of the straps supplied by Dawbarn and Sons and SpanSet; the only manufacturers to supply comprehensive labelling which included a set of cautions. Both manufacturers recommend that at least two turns of the spreader bars should be made after threading.
The tests were carried out on the same test rig that we used two years ago. Each of the 10m straps was shortened to a length of 2.1m between the hooks and attached to the rig. The straps were then tensioned by a doubleacting hydraulic ram at a set rate. BS5759 allows for some variation in the rate of tensioning and gives a number of parameters that can be contradictory: NEL chose a rate of 200mm per minute.
Each of the straps was stretched until it failed, at which point the test equipment recorded the instantaneous load on the strap. These are the figures, tabulated by NEL staff, that we have used in our results. For the summary table the result given is the average of the three individual tests.
We tested straps with a breaking capacity of 5,000kg. Manufacturers refer to this in a variety of ways such as ultimate tensile strength (UTS) and ultimate loading strength (U1S). Most of the straps followed the British Standard in quoting a Rated Assembly Strength (RAS), which is half the breaking strength. This figure is a useful guide for the number of straps needed to secure a load. The number needed equates to load divided by RAS, so for a 10-tonne load you should use at least four 2.5-tonne RAS straps. They should be positioned no more than 1.5m apart along the length of the load.
Exhaustive coverage of load restraint is contained in the Department of Transport Code of Practice, Safely of Loads on Vehicles, and in the British Standard. ALREM advised the DOT on its code of practice and has issued more concise guidelines on the use of webbing load restraints. These also contain advice on the use of sleeves and corner protectors to protect the webbing from sharp edges and abrasion.
RESULTS
Only four of the 30 straps we tested recorded a breaking strain greater than the 5,000kg claimed by their manufacturers. Of the 10 manufacturers represented, eight claimed conformity to BS5759:1987. The straps supplied by Davco (carrying only an address label) and Brycraft (carrying no label at all) did not claim BS5759.
Breaking strains ranged from 3,696kg to 5,748kg a range of over two tonnes. This is a poor result and an unsatisfactory situation for users of load restraint straps.
The test again shows the diversity in labelling, from the comprehensive (SpanSet, Dawbarn), to the non-existent (Brycraft). At least Brycraft is consistent with our 1992 tests; its straps did not carry any labelling then. Overall the standard of labelling has improved, with all but two straps carrying some indication of the RAS and load capacity.
SUMMARY
If anything the situation has worsened since our last tests two years ago. One strap failed at a lower load than the worst result in 1992 and most of the straps failed to reach their loading claims. Although we tested fewer straps with no labelling at all, manufacturers would do well to ensure that labels carry the breaking strength, RAS, length, reference number and contact address. ALREM would also like to see the RAS stencilled on the webbing at intervals over its length.