IN Almost a year ago to the day, a group
Page 47

Page 48
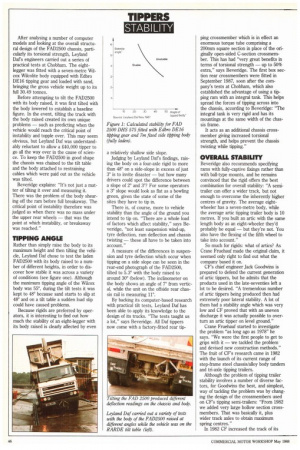
Page 49
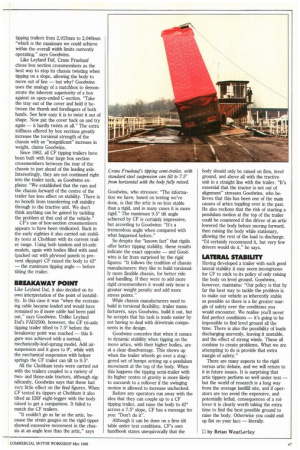
If you've noticed an error in this article please click here to report it so we can fix it.
of hard-nosed tipper operators gathered in the plush surroundings of the Majestic Hotel, Harrogate for the Road Haulage Association's annual Tipcon exhbition and conference.
During the final seminar, on modern vehicle designs, the conversation drifted back and forth covering, among other things, the quest for a truck to fill the gap between a conventional eight-legger and an artic tipper. What was needed, it was agreed, was a tipper combining the payload of a 38-tonner with the off-road performance and stability of a rigid.
At this point in the proceedings, Angus Spooner, product liaison manager with Crane Fruehauf, and one of Tipcon's panel of pundits, declared that as far as CF was concerned, artic tippers already offered greater stability than rigids. The overall reaction was one of disbelief.
How could an artic be more stable than a rigid when so many fall over? Common sense told them that with a much larger body, a higher centre of gravity and a hinge in the middle artics were obviously less stable than rigids.
Spooner stuck to his guns. Tipping trailers — at least CF's tipping trailers — were more stable, he repeated, thanks to their wider spring centres, and CF had carried out tests to prove it.
RESEARCHING
Maybe because it was almost time for lunch, or because the delegates were keen to see the burgeoning vehicle exhibition, the discussion ended there, and could easily have been forgotten; but not by Commercial Motor.
To separate myth from reality, we contacted a rigid chassis manufacturer and a trailer builder to find out exactly what they base their claims on: the results of our research are, to say the least, sur
prising. Leyland Daf is one of the many four-axle chassis manufacturers to have carried out extensive research into rigid vehicle stability, including tests on the RARDE tilt table at Chobham in Surrey. Our choice of Leyland Daf to represent the rigid sector is no accident.
The company is the market leader in both the three-axle and four-axle tipper market, and it claims that its Dutch-built FAD2500 8x4 is among the most stable tippers in the business.
Leyland Dafs sales engineering manager John Beveridge says that Daf Trucks started researching vehicle stability about three years ago.
Following the merger Leyland Daf has maintained that process, partly in collaboration with Edbro, which also participated in the tilt tests. Beveridge says: "We both happened to be working on stability projects at the same time, which helped each of us." After analysing a number of computer models and looking at the overall structural design of the FAD2500 chassis, particularly its torsional strength, Leyland Dal's engineers carried out a series of practical tests at Chobham. The eightlegger was fitted with a seven-metre Wilcox Wilcolite body equipped with Edbro DE16 tipping gear and loaded with sand, bringing the gross vehicle weight up to its full 30.49 tonnes.
Before attempting to tilt the FAD2500 with its body raised, it was first tilted with the body lowered to establish a baseline figure. In the event, tilting the truck with the body raised created its own unique problems — such as predicting when the vehicle would reach the critical point of instability and topple over. This may seem obvious, but Leyland Daf was understandably reluctant to allow a 240,000 tipper to go all the way over in the cause of science. To keep the FAD2500 in good shape the chassis was chained to the tilt table and the body attached to restraining cables which were paid out as the vehicle was tilted.
Beveridge explains: "It's not just a matter of tilting it over and measuring it. There was the problem of the body shearing off the ram before full breakaway. The critical point of instability therefore was judged as when there was no mass under the upper rear wheels — that was the point at which instability, or breakaway was reached."
TIPPING ANGLE
Rather than simply raise the body to its maximum height and then tilting the vehicle, Leyland Daf chose to test the laden FAD2500 with its body raised to a number of different heights, in order to discover how stable it was across a variety of conditions (see figure one). Although the maximum tipping angle of the Wilcox body was 55°, during the tilt tests it was kept to 480 because sand starts to slip at 48° and on a tilt table a sudden load slip could have caused problems.
Because rigids are preferred by operators, it is interesting to find out how much the stability of an eight-legger with its body raised is clearly affected by even a relatively shallow side slope.
Judging by Leyland Daf s findings, raising the body on a four-axle rigid to more than 48° on a side-slope in excess of just 30 is to invite disaster — but how many drivers could spot the difference between a slope of 2° and 3°? For some operators a 30 slope would look as flat as a bowling green, given the state of some of the sites they have to tip in.
There is, of course, more to vehicle stability than the angle of the ground you intend to tip on. "There are a whole load of factors which affect stability," says Beveridge, "not least suspension wind-up, tyre deflection, ram deflection and chassis twisting — these all have to be taken into account."
A measure of the differences in suspension and tyre deflection which occur when tipping on a side slope can be seen in the rear-end photograph of the FAD2500, tilted to 5.3° with the body raised to around 300 (below), The inclinometer on the body shows an angle of 7° from vertical, while the unit on the offside rear chassis rail is measuring 11°.
By backing its computer-based research with practical tilt tests, Leyland Daf has been able to apply its knowledge to the design of its trucks. "The tests taught us a lot," says Beveridge. All Daf tippers now come with a factory-fitted rear tip ping crossmember which is in effect an enormous torque tube comprising a 200mm square section in place of the originally open-sided C-section crossmember. This has had "very great benefits in terms of torsional strength — up to 50% extra," says Beveridge. The first box section rear crossmembers were fitted in September 1987, soon after the company's tests at Chobham, which also established the advantage of using a tipping ram with an integral tank. This helps spread the forces of tipping across into the chassis, according to Beveridge: "The integral tank is very rigid and has its mountings at the same width of the chassis frame.
It acts as an additional chassis crossmember giving increased torsional strength, and helps prevent the chassis twisting while tipping."
OVERALL STABILITY
Beveridge also recommends specifying rams with fully-captive fixings rather than with ball-type mounts, and he remains convinced that the rigid offers the best combination for overall stability: "A semitrailer can offer a wider track, but not enough to overcome the inherently higher centres of gravity. The average eightwheeler has a seven-metre body, while the average artic tipping trailer body is 10 metres_ If you built an artic with the same length body as an eight-wheeler they'd probably be equal — but they're not. You also have the flexing of the fifth wheel to take into account."
So much for rigids: what of artics? As Crane Fruehauf made the original claim, it seemed only right to find out what the company based it on.
CF's chief engineer Jack Goodwins is prepared to defend the current generation of artic tippers, but he admits that the products used in the late-seventies left a lot to be desired. "A tremendous number of artic tippers being produced then had extremely poor lateral stability. A lot of them had a stability angle which was very low and CF proved that with an uneven discharge it was actually possible to overturn an artic tipper on level ground."
Crane Fruehauf started to investigate the problem "as long ago as 1978" he says. "We were the first people to get to grips with it — we tackled the problem and devised new construction methods." The fruit of CF's research came in 1982 with the launch of its current range of step-frame steel chassis/alloy body tandem and tri-axle tipping trailers.
Although the problem of tipping trailer stability involves a number of diverse factors, for Goodwins the best, and simplest, way of tackling the problem was by changing the design of the crossmembers used on CF's tipping semi-trailers: "From 1982 we added very large hollow section crossmembers. That was basically it, plus wider track axles to obtain maximum spring centres."
In 1982 CF increased the track of its tipping trailers from 2,015mm to 2,040mm "which is the maximum we could achieve within the overall width limits currently operating," says Goodwins.
Like Leyland Daf, Crane Fruehauf chose box section crossmembers as the best way to stop its chassis twisting when tipping on a slope, allowing the body to move out of line — but why? Goodwins uses the analogy of a matchbox to demonstrate the inherent superiority of a box against an open-ended C-section. "Take the tray out of the cover and hold it between the thumb and forefingers of both hands. See how easy it is to twist it out of shape. Now put the cover back on and try again — it hardly twists at all." The extra stiffness offered by box sections greatly increase the torsional strength of the chassis with an "insignificant" increase in weight, claims Goodwins.
Since 1982, all CF tipping trailers have been built with four large box section crossmembers between the rear of the chassis to just ahead of the leading axle. Interestingly, they are not continued right into the trailer neck, as Goodwins explains: "We established that the ram and the chassis forward of the centre of the trailer has less effect on stability. There is no benefit from transferring roll stability through to the tractive unit. We don't think anything can be gained by tadding the problem at that end of the vehicle."
CF's use of box-section crossmembers appears to have been vindicated. Back in the early eighties it also carried out stability tests at Chobham with its current trailer range. Using both tandem and tri-axle models, again with bodies filled with sand (packed out with plywood panels to prevent slippage) CF raised the body to 42° — the maximum tipping angle — before tilting the trailer.
BREAKAWAY POINT
Like Leyland Daf, it also decided on its own interpretation of the point of instability. In this case it was "when the restraining cable became loaded and would have remained so if more cable had been paid out," says Goodwins. Unlike Leyland Daf's FAD2500, however, the CF tri-axle tipping trailer tilted to 7.5° before the breakaway point was reached — this figure was achieved with a normal, mechanically-leaf-sprung model. Add airsuspension and it goes to 9°, while with the mechanical suspension with helper springs the CF trailer can tilt to 9.5°.
All the Chobham tests were carried out with the trailers coupled to a variety of twoand three-axle tractors, although significantly, Goodwins says that these had very little effect on the final figures. When CF tested its tippers at Chobham it also tilted an ERF eight-legger with the body raised to get a comparison. It failed to match the CF trailers.
"It couldn't go as far as the artic, because the strain gauges on the rigid tipper showed excessive movement in the chassis at an angle less than the artic," says Goodwins, who stresses: "The information we have, based on testing we've done, is that the artic is no less stable than a rigid, and in many cases it is more rigid." The maximum 9.5° tilt angle achieved by CF is certainly impressive, but according to Goodwins: "It's a tremendous angle when compared with what, happened before."
So despite the "known fact" that rigids offer better tipping stability, these results indicate the exact opposite — and Goodwins is far from surprised by the rigid figures: "It follows the tradition of chassis manufacturers: they like to build torsionally more flexible chassis, for better ride and handling. If they were to add more rigid crossmembers it would only incur a greater weight penalty and add more stress points."
While chassis manufacturers need to build in torsional flexibility, trailer manufacturers, says Goodwins, build it out, but he accepts that his task is made easier by not having to deal with drivetrain components in the design.
Goodwins concedes that when it comes to dynamic stability when tipping on the move artics, with their higher bodies, are at a clear disadvantage. This shows up when the trailer wheels go over a staggered set of bumps setting up a pendulum movement at the top of the body. When this happens the tipping semi-trailer with its higher centre of gravity is more likely to succumb to a rollover if the swinging motion is allowed to increase unchecked.
Before any operators run away with the idea that they can couple up to a CF tipping trailer, and raise the body to 42° across a 7.5° slope, CF has a message for you: "Don't do it".
Although it can be done on a firm tilt table under test conditions, CF's own handbook states unequivocally that the body should only be raised on firm, level ground, and above all with the tractive unit in a straight line with the trailer. "It's essential that the tractor is not out of alignment" stresses Goodwins, who believes that this has been one of the main causes of artics toppling over in the past. He also reckons that the risk of starting a pendulum motion at the top of the trailer could be countered if the driver of an artic lowered the body before moving forward, then raising the body while stationary, allowing the rest of the load to discharge. "I'd certainly recommend it, but very few drivers would do it," he says.
LATERAL STABILITY
Having developed a trailer with such good lateral stability it may seem incongruous for CF to stick to its policy of only raising the body on level ground. Goodwins, however, maintains: "Our policy is that by far the best way to tackle the problem is to make our vehicle as inherently stable as possible so there is a far greater margin of safety over the conditions you would encounter. We realise you'll never find perfect conditions — it's going to be impossible to find level ground all the time. There is also the possibility of loads discharging unevenly, leaving it unstable, and the effect of strong winds. These all combine to create problems. What we are attempting to do is provide that extra margin of safety."
There are many aspects to the rigid versus artic debate, and we will return to it in future issues. It is surprising that artic tippers perform so well under test — but the world of research is a long way from the average landfill site, and if operators are too avoid the expensive, and potentially lethal, consequences of a rollover it is clearly worth taking the extra time to find the best possible ground to raise the body. Otherwise you could end up flat on your face — literally.
0 by Brian WeatLerley