It's 'ASAP' please when
Page 122
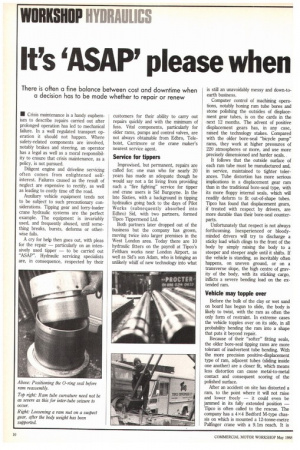
Page 123
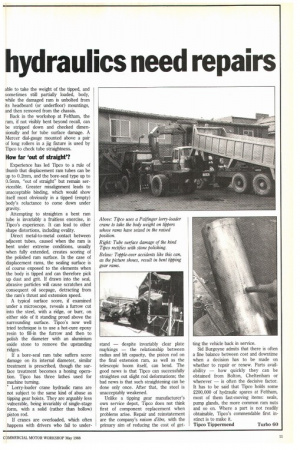
If you've noticed an error in this article please click here to report it so we can fix it.
hydraulics need repairs
There is often a fine balance between cost and downtime when a decision has to be made whether to repair or renew
• Crisis maintenance is a handy euphemism to describe repairs carried out after prolonged operation has led to mechanical failure. In a well regulated transport operation it should not happen. Where safety-related components are involved, notably brakes and steering, an operator has a legal as well as a moral responsibility to ensure that crisis maintenance, as a policy, is not pursued.
Diligent engine and driveline servicing often comes from enlightened selfinterest. Failures caused as the result of neglect are expensive to rectify, as well as leading to costly time off the road.
Auxiliary vehicle equipment tends not to be subject to such precautionary considerations. Tipping gear and lorry-loader crane hydraulic systems are the perfect example. The equipment is invariably used, and frequently abused, until something breaks, bursts, deforms or otherwise fails.
A cry for help then goes out, with pleas for the repair — particularly on an intensively used tipper — to be carried out "ASAP". Hydraulic servicing specialists are, in consequence, respected by their customers for their ability to carry out repairs quickly and with the minimum of fuss. Vital components, particularly for older rams, pumps and control valves, are not always obtainable from Edbro, Telehoist, Carrirnore or the crane maker's nearest service agent.
Service for tippers
Improvised, but permanent, repairs are called for; one man who for nearly 20 years has made an adequate though he would say not a fat living from providing such a "fire fighting" service for tipper and crane users is Sid Burgoyne. In the late Sixties, with a background in tipping hydraulics going back to the days of Pilot Works (subsequently absorbed into Edbro) Sid, with two partners, formed Tipco Tippermend Ltd.
Both partners later dropped out of the business but the company has grown, moving twice into larger premises in the West London area. Today there are 10 hydraulic fitters on the payroll at Tipco's Feltham works near London Airport, as well as Sid's son Adam, who is bringing an unlikely whiff of new technology into what is still an unavoidably messy and down-toearth business.
Computer control of machining operations, notably honing ram tube bores and stone polishing the outsides of displacement gear tubes, is on the cards in the -next 12 months. The advent of positive displacement gears has, in any case, raised the technology stakes. Compared with the older bore-seal "bicycle pump" rams, they work at higher pressures of 220 atmospheres or more, and use more precisely dimensioned and harder seals..
It follows that the outside surface of each ram tube must be manufactured and, in service, maintained to tighter tolerances. Tube distortion has more serious implications in a displacement gear ram than in the traditional bore-seal type, with its more floppy internal seals, which will readily deform to fit out-of-shape tubes. Tipco has found that displacement gears, if treated with respect by drivers, are more durable than their bore-seal counterparts.
Unfortunately that respect is not always forthcoming. Inexperienced or bloodyminded drivers will try to discharge a sticky load which clings to the front of the body by simply raising the body to a steeper and steeper angle until it shifts. If the vehicle is standing, as inevitably often happens, on uneven ground, or on a transverse slope, the high centre of gravity of the body, with its sticking cargo, inflicts a severe bending load on the extended ram.
Vehicle may topple over
Before the bulk of the clay or wet sand on board has begun to slide, the body is likely to twist, with the ram as often the only form of restraint. In extreme cases the vehicle topples over on its side, in all probability bending the ram into a shape that puts it beyond repair.
Because of their "softer" fitting seals, the older bore-seal tipping rams are more tolerant of inadvertent tube bending. With the more precision positive-displacement type of ram, adjacent tubes (sliding inside one another) are a closer fit, which means less distortion can cause metal-to-metal contact and consequent scoring of the polished surface.
After an accident on site has distorted a ram, to the point where it will not raise and lower freely — it could even be jammed in its fully extended position — Tipco is often called to the rescue. The company has a 4 x4 Bedford M-type chassis on which is mounted a 12-tonne-metre Palfinger crane with a 9.1m reach. It is able to take the weight of the tipped, and sometimes still partially loaded, body, while the damaged ram is unbolted from ts headboard (or underfloor) mountings, and then removed from the chassis.
Back in the workshop at Feltham, the ram, if not visibly bent beyond recall, can be stripped down and checked dimensionally and for tube surface damage. A Mercer dial-gauge mounted above a pair of long rollers in a jig fixture is used by Tipco to check tube straightness.
How far 'out of straight'?
Experience has led Tipco to a rule of thumb that displacement ram tubes can be up to 0.2mm, and the bore-seal type up to 0.5mm, "out of straight" but remain serviceable. Greater misalignment leads to unacceptable binding, which would show itself most obviously in a tipped (empty) body's reluctance to come down under gravity.
Attempting to straighten a bent ram tube is invariably a fruitless exercise, in Tipco's experience. It can lead to other shape distortions, including ovality.
Direct metal-to-metal contact between adjacent tubes, caused when the ram is bent under extreme conditions, usually when fully extended, creates scoring of the polished rain surface. In the case of displacement rams, the sealing surface is of course exposed to the elements when the body is tipped and can therefore pick up dust and grit. If drawn into the seal, abrasive particles will cause scratches and consequent oil seepage, detracting from the ram's thrust and extension speed.
A typical surface score, if examined under a microscope, reveals a furrow cut into the steel, with a ridge, or burr, on either side of it standing proud above the surrounding surface. Tipco's now well tried technique is to use a hot-cure epoxy resin to fill-in the furrow and then to polish the diameter with an aluminium oxide stone to remove the upstanding ridges.
If a bore-seal ram tube suffers score damage on its internal diameter, similar treatment is prescribed, though the surface treatment becomes a honing operation. Tipco has three lathes used for machine turning.
• Lorry-loader crane hydraulic rams are not subject to the same kind of abuse as tipping gear hoists. They are arguably less vulnerable, being invariably of single-stage form, with a solid (rather than hollow) piston rod.
If cranes are overloaded, which often happens with drivers who fail to under stand — despite invariably clear plate markings — the relationship between radius and lift capacity, the piston rod on the final extension ram, as well as the telescopic boom itself, can bend. The good news is that Tipco can successfully straighten out slight rod deformations; the bad news is that such straightening can be done only once. After that, the steel is unacceptably weakened.
Unlike a tipping gear manufacturer's own service depot, Tipco does not think first of component replacement when problems arise. Repair and reinstatement are the company's raison d'être, with the primary aim of reducing the cost of get
ting the vehicle back in service.
Sid Burgoyne admits that there is often a fine balance between cost and downtime when a decision has to be made on whether to repair or renew. Parts availability — how quickly they can be obtained from Bolton, Cheltenham or wherever — is often the decisive factor. It has to be said that Tipco holds some 2200,000 of hydraulic spares at Feltham, most of them fast-moving items: seals, pump glands, the more common ram nuts and so on, Where a part is not readily obtainable, Tipco's commendable first instinct is to make it.
Tipco Tippermend Turbo 60