Edbro's modernisation survives the slump
Page 41
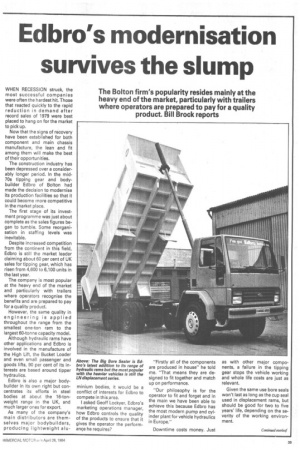
Page 42
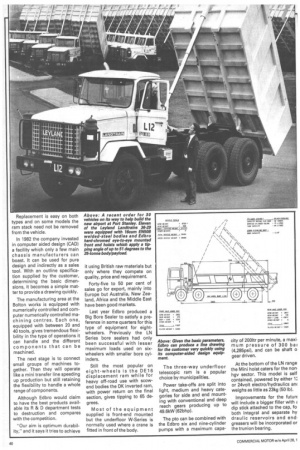
If you've noticed an error in this article please click here to report it so we can fix it.
The Bolton firm's popularity resides mainly at the heavy end of the market, particularly with trailers where operators are prepared to pay for a quality product. Bill Brock reports
WHEN RECESSION struck, the most successful companies were often the hardest hit. Those that reacted quickly to the rapid reduction in demand after record sales of 1979 were best placed to hang on for the market to pick up.
Now that the signs of recovery have been established for both component and main chassis manufacture, the lean and fit among them will make the best of their opportunities.
The construction industry has been depressed over a considerably longer period. In the mid70s tipping gear and bodybuilder Edbro of Bolton had made the decision to modernise its production facilities so that it could become more competitive in the market place.
The first stage of its investment programme was just about complete as the sales figures began to tumble. Some reorganisation in staffing levels was inevitable.
Despite increased competition from the continent in this field, Edbro is still the market leader claiming about 60 per cent of UK sales for tipping gear, which has risen from 4,600 to 6,100 units in the last year.
The company is most popular at the heavy end of the market and particularly with trailers where operators recognise the benefits and are prepared to pay for a quality product.
However, the same quality in engineering is applied throughout the range from the smallest one-ton ram to the largest 60-tonne capacity model.
Although hydraulic rams have other applications and Edbro is involved in the manufacture of the High Lift, the Bucket Loader and even small passenger and goods lifts, 90 per cent of its interests are based around tipper hydraulics.
Edbro is also a major bodybuilder in its own right but concentrates its efforts in steel bodies at about the 16-tonweight range in the UK, and much larger ones for export.
As many of the company's main distributors are themselves major bodybuilders, producing lightweight alu minium bodies, it would be a conflict of interests for Edbro to compete in this area.
I asked Geoff Lockyer, Edbro's marketing operations manager, how Edbro controls the quality of the products to ensure that it gives the operator the performance he requires? "Firstly all of the components are produced in house" he told me. "That means they are designed to fit together and match up on performance.
"Our philosophy is for the operator to fit and forget and in the main we have been able to achieve this because Edbro has the most modern pump and cylinder plant for vehicle hydraulics in Europe."
Downtime costs money. Just as with other major components, a failure in the tipping gear stops the vehicle working and whole life costs are just as relevant.
Given the same use bore seals won't last as long as the cup seal used in displacement rams, but should be good for two to five years' life, depending on the severity of the working environment. Replacement is easy on both types and on some models the ram stack need not be removed from the vehicle.
In 1982 the company invested in computer aided design (CAD) a facility which only a few main chassis manufacturers can boast. It can be used for pure design and indirectly as a sales tool. With an outline specification supplied by the customer, determining the basic dimensions, it becomes a simple matter to provide a drawing quickly.
The manufacturing area at the Bolton works is equipped with numerically controlled and computer numerically controlled machining centres. Each one, equipped with between 20 and 40 tools, gives tremendous flexibility in the type of operations it can handle and the different components that can be machined.
The next stage is to connect small groups of machines together. Then they will operate like a mini transfer line speeding up production but still retaining the flexibility to handle a whole range of components.
Although Edbro would claim to have the best products available its R & D department tests to destruction and compares with the competition.
''Our aim is optimum durability,' and it says it tries to achieve it using British raw materials but only where they compete on quality, price and requirement.
Forty-five to 50 per cent of sales go for export, mainly into Europe but Australia, New Zealand, Africa and the Middle East have been good markets.
Last year Edbro produced a Big Bore Sealer to satisfy a preference in some quarters for this type of equipment for eightwheelers. Previously the LN Series bore sealers had only been successful with lesser maximum loads used on six wheelers with smaller bore cylinders.
Still the most popular on eight-wheels is the DE1 6 displacement ram while for heavy off-road use with scowend bodies the DK inverted ram, with power return on the final section, gives tipping to 65 degrees.
Most of the equipment supplied is front-end mounted
but the under-floor W-Series is normally used where a crane is fitted in front of the body.
The three-way underfloor telescopic ram is a popular choice by municipalities.
Power take-offs are split into light, medium and heavy categories for side and end mount ing with conventional and deep reach gears producing up to 49.6kW (62bhp).
The pto can be combined with the Edbro six and nine-cylinder pumps with a maximum capa city of 200Itr per minute, a maximum pressure of 300 bar (4,285psi), and can be shaft o gear driven.
At the bottom of the LN range the Mini hoist caters for the non hgv sector. This model is self contained, powered by either 1: or 24volt electro/hydraulics an weighs as little as 23kg (50 Ib).
Improvements for the futurE will include a bigger filler with dip stick attached to the cap, fo both integral and separate hy draulic reservoirs and endgreasers will be incorporated or the trunion bearing.