New Ideas in Steel-tube Seats
Page 64
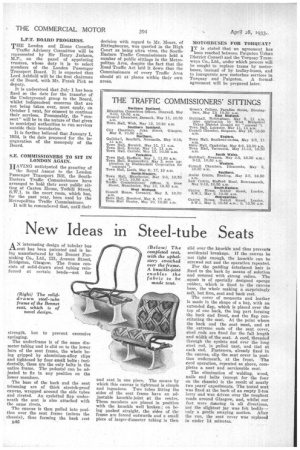
If you've noticed an error in this article please click here to report it so we can fix it.
AN interesting design of tubular bus seat has been patented and is being manufactured by the Bennet Furnishing Co., Ltd., 121, Avenue Street, Bridgeton, Glasgow. The frame consists of solid-drawn steel tubing reinforced at certain bends—not for
strength, but to prevent excessive Springing.
The underframe is of the same diameter tubing and is slid on to the lower bars of the seat frame, the whole being gripped by aluminium-alloy clips and tightened by four small bolts ; incidentally, these are the only bolts in the entire frame. The pedestal can be adjusted to fix in any position on the lower members.
The base of the back and the seat trimming are of thick stretch-proof canvas, wrapped around the side tubes and riveted. An eyeletted flap underneath the seat is also attached with the same rivets.
The canvas is then pulled into position over the seat frame (minus the chassis), thus forming the back rest E46 and seat in one piece. The means by which this canvas is tightened is simple and ingenious. Two tubes fitting the sides of the seat frame have an adjustable knuckle-joint at the centre. These members are placed in position with the knuckle well broken; on being pushed straight, the sides of the frame are forced outwards and a small piece of larger-diameter tubing is then
slid over the knuckle and thus prevents accidental breakage. If the canvas be not tight enough, the knuckle can be screwed out and the operation repeated.
For the padding 'interlaced hair is fixed to the back by means of solution and covered with strong calico. The squab is of specially designed sponge rubber, which is fixed to the canvas base, the whole making a surprisingly soft, but firm, seat and back rest.
The cover of moquette and leather is made in the shape of a bag, with an extended flap, which is placed over the top of one back, the bag part forming the back and front, and the flap constituting the seat. At the point where the back and the seat meet, and at the extreme ends of the seat cover, steel rods are fixed for the full length and width of the seat. A cord, threaded through the eyelets and over the long steel rod, is pulled taut, and tied at each end. Fasteners, already fixed in the canvas, clip the seat cover in position underneath, at the front. The cord operation, repeated as above, completes a neat and serviceable seat.
The elimination of welding, wood, nails and bolts (except for the four on the chassis) is the result of nearly two years' experiments. The tested seat was fixed at the back of an empty 2-ton lorry and was driven over the roughest roads around Glasgow, and, whilst our feet were dab:Icing in all directions, not the slightest jar was felt bodily— only a gentle swaying motion. After the run, the seat cover was replaced in under 14 minutes.