FROM RIVETS TO BONDS
Page 102
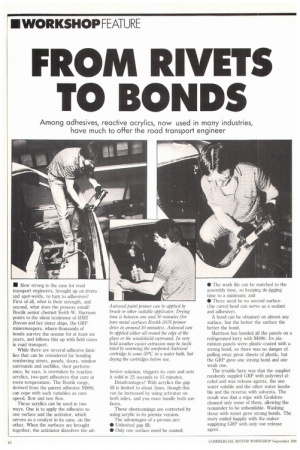
Page 103
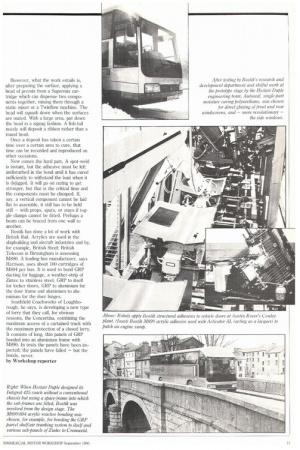
If you've noticed an error in this article please click here to report it so we can fix it.
Among adhesives, reactive acrylics, now used in many industries, have much to offer the road transport engineer
• How strong is the case for road transport engineers, brought up on rivets and spot-welds, to turn to adhesives? First of all, what is their strength, and second, what does the process entail? Bostik senior chemist Keith W. Harrison points to the silent testimony of HMS Brecon and her sister ships, the GRP minesweepers, where thousands of bonds survive the oceans for at least six years, and follows this up with field cases in road transport.
While there are several adhesive families that can be considered for bonding reinforcing struts, panels, doors, window surrounds and suchlike, their performance, he says, is overtaken by reactive acrylics, two-part adhesives that cure at room temperature. The Bostik range, derived from the parent adhesive M890, can cope with such variables as cure speed, flow and non flow.
These acrylics can be used in two ways. One is to apply the adhesive to one surface and the activator, which serves as a catalyst in its cure, on the other. When the surfaces are brought together, the activiator dissolves the ad hesive solution, triggers its cure and sets it solid in 25 seconds to 15 minutes.
Disadvantages? With acrylics the gap fill is limited to about 3mm, though this can be increased by using activator on both sides, and you must handle both surfaces.
These shortcomings are corrected by using acrylic in its premix version. The advantages of a premix are: • Unlimited gap fill; • Only one surface need be coated; • The work life can be matched to the assembly time, so keeping de-jigging time to a minimum; and • There need be no second surface (the cured bead can serve as a sealant and adhesive).
A bond can be obtained on almost any surface, but the better the surface the better the bond.
Harrison has bonded all the panels on a refrigerated lorry with M890. Its aluminium panels were plastic coated with a strong bond, so there was no danger of pulling away great sheets of plastic, but the GRP gave one strong bond and one weak one.
The trouble here was that the supplier randomly suppled GRP with polyvinyl alcohol and wax release agents, the one water soluble and the other water insoluble and the reverse with solvents. The result was that a wipe with Genldene cleaned only some of them, allowing the remainder to be unbondable. Washing those with water gave strong bonds. The story ended happily with the maker supplying GRP with only one release agent. However, what the work entails is, after preparing the surface, applying a bead of premix from a Superrnix cartridge which can dispense two components together, mixing them through a static mixer or a Twinflow machine. The bead will squash down when the surfaces are mated. With a large area, put down the bead in a zigzag fashion. A fish-tail nozzle will deposit a ribbon rather than a round bead.
Once a deposit has taken a certain time over a certain area to cure, that time can be recorded and reproduced on other occasions.
Now comes the hard part. A spot-weld is instant, but the adhesive must be left undisturbed in the bond until it has cured sufficiently to withstand the load when it is dejigged. It will go on curing to get stronger, but that is the critical time and the components must be clamped, if, say, a vertical component cannot be laid flat to assemble, it still has to be held still — with props, spars, or stays if toggle clamps cannot be fitted. Perhaps a beam can be braced from one wall to another.
Bustik has done a lot of work with British Rail. Acrylics are used in the shipbuilding and aircraft industries and by, for example, British Steel; British Telecom in Birmingham is assessing M890. A leading bus manufacturer, says Harrison, uses about 100 cartridges of M894 per bus. It is used to bond GRP ducting for luggage, a weather-strip of Zintec to stainless steel, GRP to itself for locker doors. GRP to aluminium for the door frame and aluminium to aluminium for the door hinges.
Southfield Coachworks of Loughborough, he says, is developing a new type of lorry that they call, for obvious reasons, the Concertina, combining the maximum access of a curtained truck with the maximum protection of a closed lorry. It consists of long, thin panels of GRP bonded into an aluminium frame with M890. In tests the panels have been impacted; the panels have failed — but the bonds, never.
by Workshop reporter