Via Canada to the Far East Reports that the Minister
Page 63
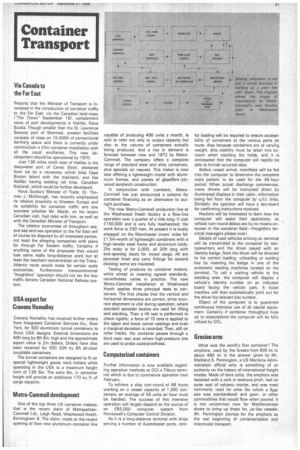
If you've noticed an error in this article please click here to report it so we can fix it.
of Transport is interested in the introduction of container traffic to the Far East. via the Canadian land-mass "The Times" September 16), complement news of port developments in Halifax, Nova Scotia. Though smaller than the St. Lawrence Seaway port of Montreal, present facilities consists of close on 19,000ft of conventional berthing space and there is currently under construction a E4m container installation with all the usual ancillaries. This new development should be operational by 1970.
Just 130 miles north east of Halifax is the deepwater port of Canso Strait, sheltered from ice by a causeway which links Cape Breton Island with the mainland, and like Halifax having existing rail links, Canadian National, which could be further developed.
Nova Scotia's Minister of Trade, Dr. Thomas J. McKeough, has recently emphasized its relative proximity to Western Europe and its suitability for container traffic and one wonders whether Mr. Marsh, on his recent Canadian visit, had talks with him, as well as with the Canadian Minister of Transport.
The relative economies of throughout sea, and sea-and-sea operation to the Far East will of course be disputed by all interested parties, not least the shipping companies with plans for through Far Eastern traffic. Certainly if anything came of the proposals they would lose some really long-distance work but at least the resultant concentration on the TransAtlantic route would make for certain scale economies. Furthermore transcontinental "freightline" operation should not tax the low traffic density Canadian National Railway system.
USA export for Cravens Homalloy
Cravens Homalloy has received further orders from Integrated Container Services Inc., New York, for 500 aluminium tunnel containers to Strict USA designs. External dimensions are 40ft long by 8ft 6in. high and the approximate export value is 2m dollars. Orders have also been received for 500 20ft by 8ft all-steel couplable containers.
The tunnel containers are designed to fit on special lightweight goose neck trailers while operating in the USA to a maximum height limit of 13ft 6in. The extra 6in. in container height will provide an additional 170 cu. ft. of cargo capacity.
M etro-Cammell development
One of the top three UK container makers: that is the recent claim of MetropolitanCammell Ltd., Leigh Road, Washwood Heath, Birmingham 8. The claim, made at the recent opening of their new aluminium container line capable of producing 400 units a month, is said to refer not only to output capacity but also to the volume of containers actually being produced. And a rise in demand is forecast between now and 1972 by MetroCammell. The company offers a complete range of standard steel and alloy containers, plus specials on request. This maker is now also offering a lightweight model with aluminium frames, and panels of glassfibre /plywood sandwich construction.
In conjunction with Lombank, MetroCammell has just announced a scheme for container financing as an alternative to outright purchase.
The new Metro-Cammell production line at the Washwood Heath factory is a flow-line operation over a quarter of a mile long. It cost E150,000 and is very fully mechanized; the work force is 250 men. At present it is busily engaged on the Manchester Liners' order for £1.5m-worth of lightweight containers with a high-tensile steel frame and aluminium body. The order is for 2,000, all 20ft long with end-opening doors for mixed cargo. All are plywood lined and carry fittings for second decking; some are insulated.
Testing of products by container makers, while aimed at meeting agreed standards, nevertheless varies in practice. The new Metro-Cammell installation at Washwood Heath applies three principal tests to containers. The first checks that the vertical and horizontal dimensions are correct, since accurate alignment is vital during operation, where standard spreader beams are used for lifting and stacking. Then a lift test is performed to check rigidity; a force of 10 tons is applied to the upper and lower corner castings and even a marginal deviation is recorded. Then, still on roller tracks, the container passes through a third main test area where high-pressure jets are used to probe waterproofness.
Computerized containers
Further information is now available regarding operation methods at OCL's Tilbury terminal which is due to commence operation next February.
To achieve a ship turn-round of 48 hours working on a vessel capacity of 1,300 containers, an average of 55 units an hour must be handled. The success of this intensive operation will largely depend on the succss of an £85,000 computer system from Honeywell's Computer Control Division.
As it is a long-distance terminal with ships serving a number of Australasian ports, care ful loading will be required to ensure accessibility of containers at the various ports en route, Also because containers are of varying weight, ship stability must be taken into account when stacking the holds, and it is anticipated that the computer will rapidly be able to furnish accurate data.
Before vessel arrival, manifests will be fed into the computer to determine the complete work pattern to be used for the 48-hour period. When actual discharge commences, crane drivers will be instructed direct by illuminated displays in their cabin, information being fed from the computer by u.h.f. links. Similarly the operator will have a key-board for confirming instructions received.
Hauliers will be interested to learn how the computer will assist their operations, as vehicle turn-round delays are by no means unknown in the container field—Freightline terminal managers please note!
Details of road vehicles arriving on terminal will be transmitted to the computer by teletypewriters and the driver issued with an identity badge. Next the driver will be directed to his correct loading, unloading or waiting bay by inserting his badge in one of the automatic reading machines located on the terminal. To call a waiting vehicle to the stacking area, the computer will display a vehicle's identity number on an indicator board facing the vehicle park. A ticket machine will then automatically print out for the driver his relevant bay number.
Object of the computer is to guarantee continuous intensive use of all capital equipment. Certainly if container throughput lives up to expectations the computer will be fully utilized by OCL.
Grecian urns
What was the world's first container? The amphora, used by the Greeks from 600 ac to about 480 BC is the answer given by Mr. Maitland S. Pennington, a US Maritime Administration official who is something of an authority on the history of international freight modes. Made of terra cotta, the amphora was fastened with a -cork in resinous pitch, had an outer seal of volcanic mortar, and was most commonly used for wine (for which a 5gal size was standardized) and grain, or other commodities that would flow when poured. It is not uncommon now for Mediterranean divers to bring up these fat, jar-like vessels. Mr. Pennington plumps for the amphora as the real beginning of containerization and intermodal transport.