some on-the-spot reactions
Page 58
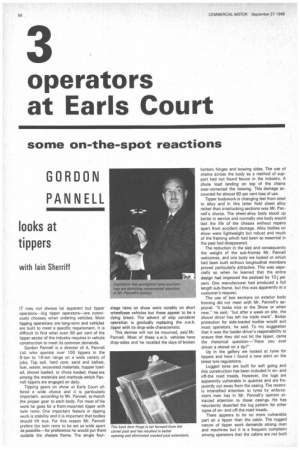
Page 59
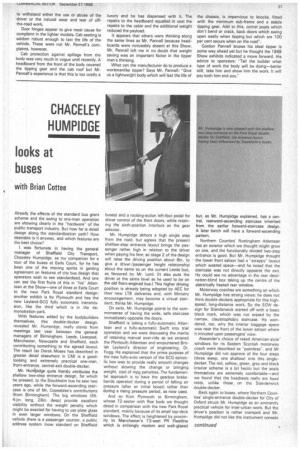
If you've noticed an error in this article please click here to report it so we can fix it.
GORDON PANNELL
looks at tippers
with lain Sherriff
IT may not always be apparent but tipper operators-big tipper operators—are notoriously choosey when ordering vehicles. Most tipping operations are long-term and vehicles are built to meet a specific requirement. It is difficult to find what even 50 per cent of the tipper sector of the industry requires in vehicle construction to meet its common demands.
Gordon Pannell is a director of A. Pannell Ltd. who operate over 100 tippers in the 8-ton to 16-ton range on a wide variety of jobs. Top soil, hard core, sand and ballast, fuel, waste, excavated materials, hopper loaded, shovel loaded, or chute loaded, these are among the materials and methods which Pannell tippers are engaged on daily.
Tipping gears on show at Earls Court offered a wide choice and it is particularly important, according to Mr. Pannell, to Match the proper gear to each body. For most of his work he goes for a front-mounted tipper with twin rams. One important feature in tipping work is stability and it is important that bodies should lift true. For this reason Mr. Pannell prefers the twin rams to be set as wide apart as possible—for preference he would put them outside the chassis frame. The single four stage rams on show were notably on short wheelbase vehicles but these appear to be a dying breed. The advent of skip container operation is gradually replacing the s.w.b. tipper with its drop-side characteristic.
This demise wilt not be mourned, said Mr. Pannell. Most of these s.w.b. vehicles have drop-sides and he recalled the days of broken bottom hinges and bowing sides. The use of chains across the body as a method of support had not found favour in the industry. A chute load landing on top of the chains over-corrected the bowing. This damage accounted for almost 60 per cent loss of use.
Tipper bodywork is changing fast from steel to alloy and in this latter field sheet alloy rather than interlocking sections was Mr. Pannell's choice. The sheet-alloy body stood up better in service and normally one body would last the life of the chassis without repairs apart from accident damage. Alloy bodies on show were lightweight but robust and much of the framing which had been so essential in the past had disappeared.
The reduction in the size and consequently the weight of the sub-frames Mr. Pannell welcomes, and one body we looked at which had been built without longitudinal members proved particularly attractive. This was especially so when he learned that the entire design had improved the payload by 12 pei cent. One manufacturer had produced a full length sub-frame, but this was apparently at a customer's request.
The use of box sections on exterior body framing did not meet with Mr. Pannell's approval. "It looks nice at the Show or when new," he said, "but after a week on site, the shovel driver has left his trade mark". Better protection for side-loaded bodies would suit most operators, he said. To my suggestion that it was the loader-driver's responsibility to ensure that they did not hit the tipper, came the rhetorical question—"Have you ever driven a shovel on a tip?"
Up in the gallery we looked at tyres for tippers and here I found a new slant on the latest tyre regulations.
Lugged tyres are built for soft going and this construction has been included in onand off-the road treads. However, the lugs are apparently vulnerable in quarries and are frequently cut away from the casing. The recently intensified attention to tyres by enforcement men has in Mr. Pannell's opinion attracted attention to those casings. He has reluctantly deserted the lug pattern for other types of onand off-the-road treads.
There appears to be no more vulnerable part on a tipper than the cabin. The rugged nature of tipper work demands strong men and machines but it is a frequent complaint among operators that the cabins are not built to withstand either the use or abuse of the driver or the natural wear and tear of offthe-road work.
Door hinges appear to give most cause for complaint in the lighter models. Cab seating is seldom robust enough to last the life of the vehicle. These were not Mr. Pannell's complaints, however.
Cab protection against spillage from the body was very much in vogue until recently. A headboard from the front of the body covered the tipping gear and the cab roof but Mr. Pannell's experience is that this is too costly a luxury and he has dispensed with it. The repairs to the headboard equalled in cost the repairs to the cabin and the additional weight reduced the payload.
It appears that others were thinking along the same lines as Mr. Pannell because headboards were noticeably absent at this Show. Mr. Pannell left roe in no doubt that weight saving was an important factor in the tipper man's thinking.
What can the manufacturer do to produce a workmanlike tipper? Says Mr. Pannell: -Give us a lightweight body which will last the life of
the chassis, is impervious to knocks, fitted with the minimum sub-frame and a stable tipping gear. Add to this, corner posts which don't bend or crack, back doors which swing open easily when tipping but which are 100 per cent secure when on the road".
Gordon Pannell knows his ideal tipper is some way ahead yet but he thought the 1968 Show exhibits indicated a move forward. His advice to operators: "Tell the builder what type of work the body will be doing—better still, take him and show him the work. It will pay both him and you."