Cost Recording Made Easy
Page 32
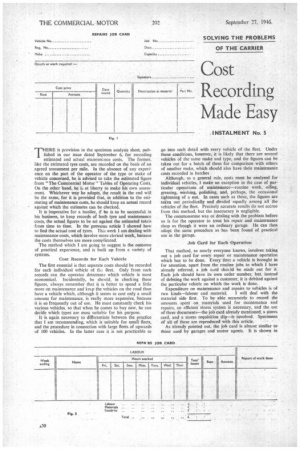
Page 33
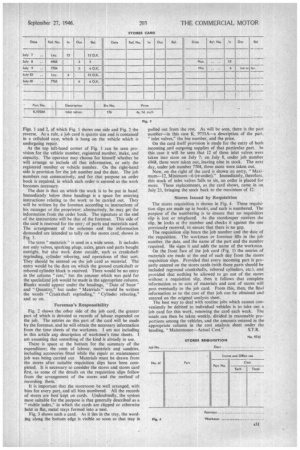
If you've noticed an error in this article please click here to report it so we can fix it.
THERE is provision in the specimen analysis sheet, published in our issue dated September 6, for recording estimated and actual maintenance costs, The former, like the estimated tyre costs, are recorded on the basis of an agreed assessment per mile. In the absence of any experience on the part of the operator of the type or make of vehicle concerned, he is advised to take the estimated figure from "The Commercial Motor" Tables of Operating Costs. On the other hand, he ie. at liberty to make his own assessment. Whichever way he adopts, the result in the end will be the same, for it is provided that, in addition to the estimating of maintenance costs, he should keep an actual record against which the estimates can be checked.
It is imperative for a haulier, if be is to be successful in his business, to keep records of both tyre and maintenance costs, the actual figures to be set against the estimated totals from time to time. In the 'prevtous article I showed how to find the actual cost of tyres. This week I am dealing with maintenance costs, which involve more clerical work, because the costs themselves are more complicated.
The method which I am going to suggest is the outcome of practical experience, and is built up from a variety of systems.
Cost Records for Each Vehicle The first essential is that separate costs should be recorded for each individual vehicle ot tlie fleet. Only from such records can the operator determine. which vehicle is most economical. Incidentally, he sheuld, in checking these figures, always remember that it is better to spend a little more on maintenance and kesp the vehicles on the road than have a vehicle which, although it seems to cost only a small amount for maintenance, is really more expensive, because it is so frequently out of use. He must constantly check his various vehicles, so that when he comes to buy new, he can decide which types are mast suitable for his purpose, IL is again necessary to differentiate between the practice that I am recommending, which is' suitable for small fleets, and the procedure in connection with large fleets of upwards of 100 vehicles. In the latter case it is not practicable to go into such detail with every vehicle of the fleet. Under those conditions, howevet, it is likely that there are several vehicles of the same make and type, and the figures can be taken out for a batch of them for comparison with others of another make, which should also have their maintenance costs recorded in batches Although, as a general rule, costs must be analysed for individual vehicles, I make an exception in the case of particular operations of maintenance—routine work, offing. greasing, washing, polishing, and, perhaps, the occasional tightening of a nut, In cases such as these, the figures are taken out periodically and divided equally among all the vehicles of the fleet. Precisely accurate results do not accrue from this method, but the inaccuracy is negligible.
The cotternonsense way OE dealing with the problem before us is for the operator to treat his repair and maintenance shop as though it were an ordinary garage. He can then adopt the same procedure as has been found of practical use in the garage.
Job Card for Each Operation
That method, as nearly everyone knows, involves taking out a job card for every repair or maintenance operation which has to be done. Every time a vehicle is brought in for attention, apart from the routine jobs to which I have already referred, a fob card shoeld be made out for it. Each job should have its own order number, but. instead of debiting the work against a customer, it is debited against the particular vehicle on which the work is done.
Expenditure on maintenance and repairs to vehicles is of two kinds—labour and material. I will deal with the material side first. To be able accurately to record the amounts spent on . materials used for maintenance and repairs, an efficient stores system is necessary, and the use of three documents—the job card already mentioned, a stores card, and a stores requisition slip—is involved. Specimens of all of these are reproduced with this article. As already pointed out, the job card is almost similar to those used by garages and motor agents. It is shown in Figs. 1 and 2, of which Fig. 1 shows one side and Fig. 2 the reverse. As a rule, a job card is quarto size and is contained in a celluloid case, which is hung on the vehicle which is undergoing repair.
At the top left-hand corner of Fig. I can be seen provision for the vehicle number, registered number, make, and capacity. The operator may choose for himself whether he will arrange to include all that information, or only the registered number or vehicle number. On the right-hand side is provision for the job number and the date. The job numbers run consecutively, and for that purpose an order book is required, in which each order is entered as the work becomes necessary.
The date is that on which the work is to be put in hand. Immediately below these headings is a space for entering instructions relating to the work to be carried out. They will be written by the foreman according to instructions of his manager or the proprietor; alternatively, he may get the information from the order book. The signature at the end of the instructions will be that of the foreman. This side of the card is reserved for the entry of parts and materials used. The arrangement of the columns and the information demanded are intended to tally on the stores card, shown in Fig. 3.
The term " materials" is used in a wide sense. It includes not only valves, sparking plugs, axles, gears and parts bought outright, but also work done outside, such as crankshaft regrinding, cylinder reboring. and operations of that sort. They should be entered on the job card as material. The entry would be the date on which the ground crankshaft or rebored cylinder block is received. There would be no entry in the column "rate," but the amount which was paid for the specialized job would be made in the appropriate column. Blanks would appear under the headings, ' Date of issue" and "Quantity," but under "Materials" would be written the words "Crankshaft regrinding," "Cylinder reboring," and so on.
Foreman's Responsibility Fig. 2 shows the other side of the job card, the greater part of which is devoted to records of labour expended on the job. The entries on this part of the card will be made by the foreman, and he will obtain the necessary information from the time sheets of the workmen. I am not including in this article any description of workmen's time sheets. I am assuming that something of the kind is already in use.
There is space at the bottom for the summary of the expenditure; the costs of labour, materials and sundries. including accessories fitted while the repair or maintenance job was being carried out Materials must be drawn from the stores after suitable requisition slips have been completed. It is necessary to consider the stores and stores card first, as some of the details on the requisition slips follow from the arrangement of the stores and the method of recording them.
It is important that the storeroom be well arranged, with bins for every part, and all bins numbered. Alt the records of stores are best kept on cards. Undoubtedly, the system most suitable for the purpose is that generally described as a " visible index," in which the cards are clipped or otherwise held in flat, metal trays formed into a nest.
Fig. 3 shows such a card. As it lies in the tray, the wording along the bottom edge is visible so soon as that tray is pulled out from the rest. As will be seen, there is the part number—in this case K. 9733A—a description of the part, "inlet valves," the bin number, and the price.
On the card itself provision is made for the entry of both incoming and outgoing supplies of that particular part. In this case it will be seen that 12 of these inlet valves were taken into store on July 7; on July 8, under job number 6968, three were taken out, leaving nine in stock. The next day, under job number 7704, three more were taken out.
Now, on the right of the card is shown an entry, " Maximum-12, Minimum-6 (re-order)." Immediately, therefore, this stock of inlet valves falls to six, an order is placed for more. These replacements, as the card shows, came in on July 23, bringing the stock back to the maximum of 12.
Stores Issued by Requisition The stores requisition is shown in Fig. 4. These requisition slips are made up in books, and each is numbered. The purpose of the numbering is to ensure that no requisition slip is lost or misplaced. As the storekeeper receives the slip, he looks at the number and checks it against the one previously received, to ensure that there is no gap.
The requisition slip bears the job number and the date of the requisition. The workman or foreman fills in the job number, the date, and the name of the part and the number required. He signs it and adds the name of the workman. On the front face of the job card (Fig. 1) the entries of materials are made at the end of each day from the stores requisition slips. Provided that every incoming part is properly entered on the stores cards (with those parts should be included reground crankshafts, rebored cylinders, etc.), and provided that nothing be allowed to go out of the stores without a requisition slip, then it follows that complete information as to cost of materials and cost of stores will pass eventually to the job card. From this, then, the final information as to the cost of that job can be obtained and entered on the original analysis sheet. The best way to deal with routine jobs which cannot conveniently be debited to individual vehicles is to take out a job card for this work, renewing the card each week. The totals can then be taken weekly, divided in reasonable proportions among the vehicles, and the amounts entered in the appropriate column in the cost analysis sheet under the heading, "Maintenance—Actual Cost." S.T.R.