IVECO FORD CARGO 3828
Page 75
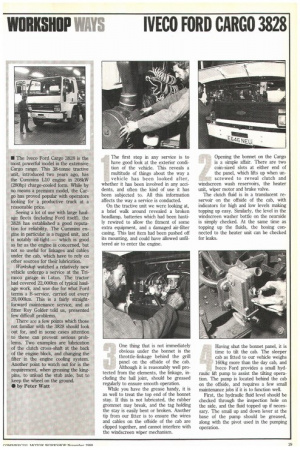
Page 76
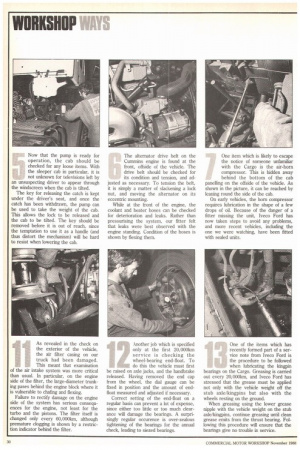
Page 77
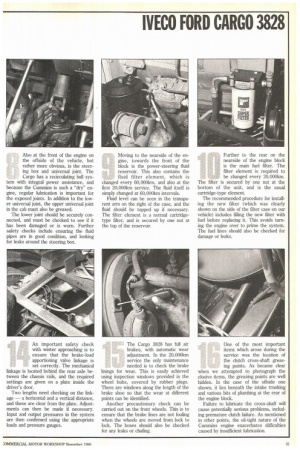
Page 78
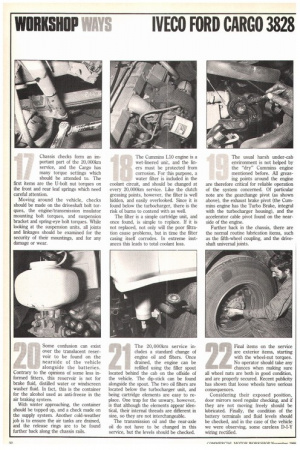
If you've noticed an error in this article please click here to report it so we can fix it.
The first step in any service is to have good look at the exterior condition of the vehicle. This reveals a multitude of things about the way a vehicle has been looked after, whether it has been involved in any acci dents, and often the kind of use it has been subjected to. All this information affects the way a service is conducted.
On the tractive unit we were looking at, a brief walk around revealed a broken headlamp, batteries which had been hastily rewired to allow the fitment of some extra equipment, and a damaged air-filter casing. This last item had been pushed off its mounting, and could have allowed unfiltered air to enter the engine.
One thing that is not irrunediately obvious under the bonnet is the throttle-linkage behind the grill panel on the offside of the cab. Although it is reasonably well protected from the elements, the linkage, including the ball joint, should be greased regularly to ensure smooth operation.
While you have the grease handy, it is as well to treat the top end of the bonnet stay. If this is not lubricated, the rubber grommet may break, and the tag holding the stay is easily bent or broken. Another tip from our fitter is to ensure the wires and cables on the offside of the cab are clipped together, and cannot interfere with the windscreen wiper mechanism. Opening the bonnet on the Cargo is a simple affair. There are two coin-sized slots at either end of the panel, which lifts up when unscrewed to reveal clutch and windscreen wash reservoirs, the heater unit, wiper motor and brake valve.
The clutch fluid is in a translucent reservoir on the offside of the cab, with indicators for high and low levels making topping up easy. Similarly, the level in the windscreen washer bottle on the nearside is simply checked. At the same time as topping up the fluids, the hosing connected to the heater unit can be checked for leaks.
Having shut the bonnet panel, it is time to tilt the cab. The sleeper cab as fitted to our vehicle weighs 160kg more than the day cab, and Iveco Ford provides a small hyd raulic lift pump to assist the tilting operation. The pump is located behind the cab on the offside, and requires a few small maintenance jobs if it is to function well.
First, the hydraulic fluid level should be checked through the inspection hole on the side, and the fluid topped up if necessary. The small up and down lever at the base of the pump should be greased, along with the pivot used in the pumping operation. Now that the pump is ready for operation, the cab should be checked for any loose items. With the sleeper cab in particular, it is not unknown for televisions left by an unsuspecting driver to appear through the windscreen when the cab is tilted.
The key for releasing the catch is kept under the driver's seat, and once the catch has been withdrawn, the pump can be used to take the weight of the cab. This allows the lock to be released and the cab to be tilted. The key should be removed before it is out of reach, since the temptation to use it as a handle (and thus distort the mechanism) will be hard to resist when lowering the cab. The alternator drive belt on the Cummins engine is found at the front, offside of the vehicle. The drive belt should be checked for its condition and tension, and adjusted as necessary. To tension the belt, it is simply a matter of slackening a lock nut, and moving the alternator on its eccentric mounting.
While at the front of the engine, the coolant and heater hoses can be checked for deterioration and leaks. Rather than pressurising the system, our fitter felt that leaks were best observed with the engine standing. Condition of the hoses is shown by flexing them. One item which is likely to escape the notice of someone unfamiliar with the Cargo is the air-horn compressor. This is hidden away behind the bottom of the cab panelling on the offside of the vehicle. As shown in the picture, it can be reached by leaning round the side of the cab.
On early vehicles, the horn compressor requires lubrication in the shape of a few drops of oil. Because of the danger of a fitter missing the unit, Iveco Ford has now taken steps to avoid any problems, and more recent vehicles, including the one we were watching, have been fitted with sealed units. Also at the front of the engine on the offside of the vehicle, but rather more obvious, is the steering box and universal joint. The Cargo has a recirculating ball sys tem with integral power assistance, and because the Cummins is such a "dry" engine, regular lubrication is important for the exposed joints. In addition to the lower universal joint, the upper universal joint in the cab must also be greased.
The lower joint should be securely connected, and must be checked to see if it has been damaged or is worn. Further safety checks include ensuring the fluid pipes are in good condition, and looking for leaks around the steering box. Moving to the nearside of the engine, towards the front of the block is the power-steering fluid reservoir. This also contains the fluid filter element, which is changed every 60,000km, and also at the first 20,000km service. The fluid itself is simply changed at 60,000km intervals.
Fluid level can be seen in the transparent arm on the right of the case, and the fluid should be topped up if necessary. The filter element is a normal cartridgetype filter, and is secured by one nut at the top of the reservoir. Further to the rear on the nearside of the engine block is the main fuel filter. The filter element is required to be changed every 20,000km. The filter is secured by one nut at the bottom of the unit, and is the usual cartridge-type element.
The recommended procedure for installing the new filter (which was clearly shown on the side of the filter case on our vehicle) includes filling the new filter with fuel before replacing it. This avoids turning the engine over to prime the system. The fuel lines should also be checked for damage or leaks.
As revealed in the check on the exterior of the vehicle, the air filter casing on our truck had been damaged. This meant that examination of the air intake system was more critical than usual. In particular, on the engine side of the filter, the large-diameter trunking pases behind the engine block where it is vulnerable to chafing and flexing.
Failure to rectify damage on the engine side of the system has serious consequences for the engine, not least for the turbo and the pistons. The filter itself is changed only every 60,000Iun, although premature clogging is shown by a restriction indicator behind the filter. Another job which is specified only at the first 20,000km service is checking the wheel-bearing end-float. To do this the vehicle must first be raised on axle jacks, and the handbrake released. Having removed the end cap from the wheel, the dial gauge can be fixed in position and the amount of endfloat measured and adjusted if necessary.
Correct setting of the end-float on a regular basis can prevent a lot of expense, since either too little or too much clearance will damage the bearings. A surprisingly regular occurence is over-zealous tightening of the bearings for the annual check, leading to siezed bearings. One of the items which has recently formed part of a service note from Iveco Ford is the procedure to be followed when lubricating the kingpin bearings on the Cargo. Greasing is carried out every 20,000km, and Iveco Ford has stressed that the grease must be applied not only with the vehicle weight off the stub axle/kingpins but also with the wheels resting on the ground.
When greasing using the lower grease nipple with the vehicle weight on the stub axle/kingpins, continue greasing until clean grease emits from the thrust bearing. Following this procedure will ensure that the bearings give no trouble in service. An important safety check with winter approaching is to ensure that the brake-load apportioning valve linkage is set correctly. The mechanical linkage is located behind the rear axle between the chassis rails, and the required settings are given on a plate inside the driver's door.
Two lengths need checking on the linkage — a horizontal and a vertical distance, and these are clear from the plate. Adjustments can then be made if necessary. Input and output pressures in the system are then confirmed using the appropriate loads and pressure gauges. The Cargo 3828 has full air brakes, with automatic wear adjustment. In the 20,000km service the only maintenance needed is to check the brake linings for wear. This is easily achieved using inspection windows provided in the wheel hubs, covered by rubber plugs_ There are windows along the length of the brake shoe so that the wear at different points can be identified.
Another precautionary check can be carried out on the front wheels. This is to ensure that the brake lines are not fouling when the wheels are moved from lock to lock. The hoses should also be checked for any leaks or chafing. One of the most important items which arose during the service was the location of the clutch cross-shaft greasing points. As became clear when we attempted to photograph the elusive items, the greasing points are well hidden. In the case of the offside one shown, it lies beneath the intake trunking and various bits of plumbing at the rear of the engine block.
Failure to lubricate the cross-shaft will cause potentially serious problems, including premature clutch failure. As mentioned in other points, the oil-tight nature of the Cummins engine exacerbates difficulties caused by insufficient lubrication. Chassis checks form an important part of the 20,000km service, and the Cargo has many torque settings which should be attended to. The first items are the U-bolt nut torques on the front and rear leaf springs which need careful attention.
Moving around the vehicle, checks should be made on the driveshaft bolt torques, the engine/transmission insulator mounting bolt torques, and suspension bracket and spring-eye bolt torques. While looking at the suspension units, all joints and linkages should be examined for the security of their mountings, and for any damage or wear. The Cummins L10 engine is a wet-linered unit, and the liners must be protected from corrosion. For this purpose, a water filter is included in the coolant circuit, and should be changed at every 20,000km service. Like the clutch greasing points, however, the filter is well hidden, and easily overlooked. Since it is found below the turbocharger, there is the risk of burns to contend with as well.
The filter is a simple cartridge unit, and once found, is simple to replace. If it is not replaced, not only will the poor filtration cause problems, but in time the filter casing itself corrodes. In extreme instances this leads to total coolant loss.
The usual harsh under-cab environment is not helped by the "dry" Cummins engine mentioned before. All greasing points around the engine are therefore critical for reliable operation of the system concerned. Of particular note are the gearchange pivot (as shown above), the exhaust brake pivot (the Cummins engine has the Turbo Brake, integral with the turbocharger housing), and the accelerator cable pivot found on the nearside of the engine.
Further back in the chassis, there are the normal routine lubrication items, such as the fifth-wheel coupling, and the driveshaft universal joints.
Some confusion can exist over the translucent reservoir to be found on the nearside of the vehicle alongside the batteries. Contrary to the opinions of some less informed fitters, this reservoir is not for brake fluid, distilled water or windscreen washer fluid. In fact, this is the container for the alcohol used as anti-freeze in the air braking system.
With winter approaching, the container should be topped up, and a check made on the supply system. Another cold-weather job is to ensure the air tanks are drained, and the release rings are to be found further back along the chassis rails.
The 20,000km service includes a standard change of engine oil and filters. Once drained, the engine can be refilled using the filler spout located behind the cab on the offside of the vehicle. The dip-stick can be found alongside the spout. The two oil filters are located below the turbocharger unit, and being cartridge elements are easy to replace. One trap for the unwary, however, is that although the elements appear identical, their internal threads are different in size, so they are not interchangeable.
The transmission oil and the rear-axle oil do not have to be changed in this service, but the levels should be checked. Final items on the service are exterior items, starting with the wheel-nut torques. No operator should take any
1111111111inglg chances when making sure all wheel nuts are both in good condition, and are properly secured. Recent publicity has shown that loose wheels have serious consequences.
Considering their exposed position, door mirrors need regular checking, and if they are not moving freely should be lubricated. Finally, the condition of the battery terminals and fluid levels should be checked, and in the case of the vehicle we were observing, some careless D-I-Y wiring rectified.