Replace wheelnuts after 10 changes, delegates told
Page 70
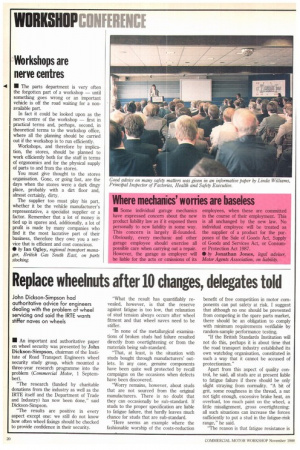
Page 71
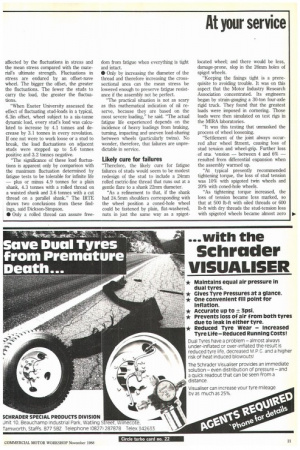
Page 72
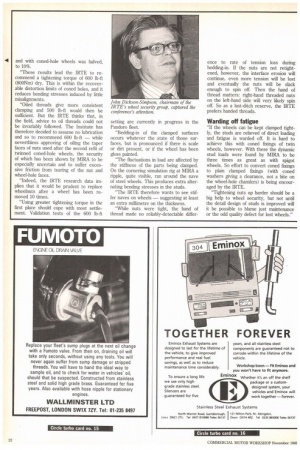
If you've noticed an error in this article please click here to report it so we can fix it.
John Dickson-Simpson had authoritative advice for engineers dealing with the problem of wheel servicing and said the IRTE wants stiffer naves on wheels
• An important and authoritative paper on wheel security was presented by John Dickson-Simpson, chairman of the Institute of Road Transport Engineers wheel security study group, which mounted a three-year research programme into the problem (Commercial Motor, 1 September).
"The research (funded by charitable donations from the industry as well as the 1RTE itself and the Department of Trade and Industry) has now been done," said Dickson-Simpson.
"The results are positive in every aspect except one: we still do not know how often wheel fixings should be checked to provide confidence in their security. "What the result has quantifiably revealed, however, is that the reserve against fatigue is too low, that relaxation of stud tension always occurs after wheel fitment and that wheel naves need to be stiffer.
"In none of the metallurgical examinations of broken studs had failure resulted directly from overtightening or from the materials being sub-standard.
"That, at least, is the situation with studs bought through manufacturers' outlets. In any case, genuine components have been quite well protected by recall campaigns on the occasions when defects have been discovered.
"Worry remains, however, about studs that are not sourced from the original manufacturers. There is no doubt that they can occasionally be sub-standard. If studs to the proper specification are liable to fatigue failure, that hardly leaves Much chance for studs that are sub-standard.
"Here seems an example where the fashionable worship of the costs-reduction
benefit of free competition in motor components can put safety at risk. 1 suggest that although no one should be prevented from competing in the spare parts market, there should be an obligation to comply with minimum requirements verifiable by random-sample performance testing.
"If the British Standards Institution will not do this, perhaps it is about time that the road transport industry established its own watchdog organisation, constituted in such a way that it cannot be accused of protectionism."
Apart from this aspect of quality control, he said, all studs are at present liable to fatigue failure if there should be only slight straying from normality. "A bit of grit, some roughness in the thread, a nut not tight enough, excessive brake heat, an overload, too much paint on the wheel, a little misalignment, gross overtightening: all such situations can increase the forces sufficiently to put a stud in the fatigue-risk range," he said.
"The reason is that fatigue resistance is affected by the fluctuations in stress and the mean stress compared with the material's ultimate strength. Fluctuations in stress are endured by an offset-nave wheel. The bigger the offset, the greater the fluctuations. The fewer the studs to carry the load, the greater the fluctuations.
"When Exeter University assessed the effect of fluctuating stud-loads in a typical, 6. 3m offset, wheel subject to a six-tonne dynamic load, every stud's load was calculated to increase by 4.1 tonnes and decrease by 3.1 tonnes in every revolution. If one nut were to work loose or a stud to break, the load fluctuations on adjacent studs were stepped up to 5.6 tonnes positive and 3.2 tonnes negative.
"The significance of these load fluctuations is apparent only by comparison with the maximum fluctuation determined by fatigue tests to be tolerable for infinite life — plus or minus 4.9 tonnes for a plain shank, 4.3 tonnes with a rolled thread on a waisted shank and 3.6 tonnes with a cut thread on a parallel shank." The IRTE draws two conclusions from these findings, said Dickson-Simpson.
• Only a rolled thread can assure free dom from fatigue when everything is tight and intact.
• Only by increasing the diameter of the thread and therefore increasing the crosssectional area can the mean stress be lowered enough to preserve fatigue resistance if the assembly not be perfect.
"The practical situation is not as scary as this mathematical indication of nil reserve, because they are based on the most severe loading," he said. "The actual fatigue life experienced depends on the incidence of heavy loadings from braking, turning, impacting and uneven load-sharing between wheels (particularly twins). No wonder, therefore, that failures are unpredictable in service.
Likely cure for failures "Therefore, the likely cure for fatigue failures of studs would seem to be modest redesign of the stud to include a 24min rolled metric-fine thread that runs out at a gentle flare to a shank 22inin diameter.
"As a refinement to that, if the shank had 24.5mm shoulders corresponding with the wheel position a coned-hole wheel could be fastened by plain, flat-washered, nuts in just the same way as a spigot located wheel; and there would be less, damage-prone, slop in the 26nun holes of spigot wheels.
"Keeping the fixings tight is a prerequisite to avoiding trouble. It was on this aspect that the Motor Industry Research Association concentrated. Its engineers began by strain-gauging a 30-ton four-axle rigid truck. They found that the greatest loads were imposed in cornering. Those loads were then simulated on test rigs in the MIRA laboratories.
"It was this testing that unmasked the process of wheel loosening.
"Settlement of the joint always occurred after wheel fitment, causing loss of stud tension and wheel-grip. Further loss of stuc. tension — between 4 and 6% — resulted from differential expansion when the assembly warmed up.
"At typical presently recommended tightening torque, the loss of stud tension was 10% with spigoted twin wheels and 20% with coned-hole wheels.
"As tightening torque increased, the loss of tension became less marked, so that at 500 lb-ft with oiled threads or 600 lb-ft with dry threads the stud-tension loss with spigoted wheels became almost zero and with coned-hole wheels was halved, to 10%.
"These results lead the IRTE to recommend a tightening torque of 600 lb-ft (800Nm) dry. This is within the recoverable distortion limits of coned holes, and it reduces bending stresses induced by little misalignments.
"Oiled threads give more consistent clamping and 500 lb-ft would then be sufficient. But the IRTE thinks that, in the field, advice to oil threads could not be invariably followed. The Institute has therefore decided to assume no lubrication and so to recommend 600 lb-ft — while neverthless approving of oiling the taper faces of nuts used after the second refit of twinned coned-hole wheels, the security of which has been shown by MIRA to be especially uncertain and to suffer excessive friction from tearing of the nut and wheel-hole faces.
"Indeed, the IRTE research data implies that it would be prudent to replace wheelnuts after a wheel has been removed 10 times.
"Using greater tightening torque in the first place should cope with most settlement. Validation tests of the 600 lb-ft setting are currently in progress in the Pandoro fleet.
"Bedding-in of the clamped surfaces occurs whatever the -state of those surfaces, but is pronounced if there is scale or dirt present, or if the wheel has been gloss painted.
"The fluctuations in load are affected by the stiffness of the parts being clamped. On the cornering simulation rig at MIRA a ripple, quite visible, ran around the nave of steel wheels. This produces extra alternating bending stresses in the studs. IRTE therefore wants to see stiffer naves on wheels — suggesting at least an extra millimetre on the thickness. "While nuts were tight, the hand of thread made no reliably-detectable differ ence to rate of tension loss during bedding-in. If the nuts are not retightened, however, the interface erosion will continue, even more tension will be lost and eventually the nuts will be slack enough to spin off. Then the hand of thread matters: right-hand threaded nuts on the left-hand side will very likely spin off. So as a last-ditch reserve, the IRTE prefers handed threads.
Warding off fatigue
"If the wheels can be kept clamped tightly, the studs are relieved of direct loading and fatigue is warded off. It is hard to achieve this with coned fixings of twin wheels, however. With these the dynamic stud loads were found by MIRA to be three times as great as with spigot wheels. So effort to convert coned fixings to plain clamped fixings (with coned washers giving a clearance, not a bite on the wheel-hole chamfers) is being encouraged by the IRTE.
"Tightening nuts up harder should be a big help to wheel security, but not until the detail design of studs is improved will it be possible to blame just maintenance or the odd quality defect for lost wheels."