Towards Better Performance
Page 62
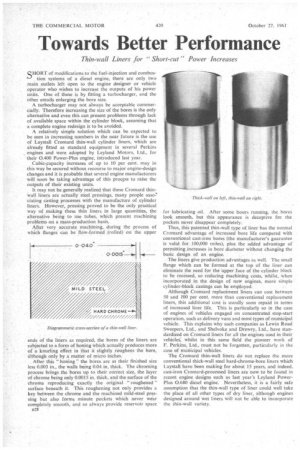
If you've noticed an error in this article please click here to report it so we can fix it.
Thin-wall Liners for "Short-cut" Power Increases
SHORT of modifications to the fuel-injection and combustion systems of a diesel engine, there are only two main _outlets left open to the engine designer or vehicle operator who wishes to increase the outputs of his power units. One of these is by fitting a turbocharger, and the other entails enlarging the bore size.
A turbocharger may not always be acceptable commercially. Therefore increasing the size of the bores is the only alternative and even this can present problems through lack of available space within the cylinder block, assuming that a complete engine redesign is to be avoided.
A relatively simple solution which can be expected to be seen in increasing numbers in the near future is the use of Laystall Cromard thin-wall cylinder liners, which are already fitted as standard equipment in several Perkins engines and were adopted by Leyland Motors, Ltd., for their 0.400 Power-Plus engine, introduced last year.
Cubic-capacity increases of up to 10 per cent. may in this way be secured without recourse to major engine-design changes and it is probable that several engine manufacturers will soon be taking advantage of this process to raise the outputs of their existing units.
It may not be generally realized that these Cromard thinwall liners are actually steel pressings, many people asso-' dating casting processes with the manufacture of cylinder liners. However, pressing proved to be the only practical way of making these thin liners in large quantities, the alternative being to use tubes, which present machining problems on a mass-production basis.
After very accurate machining, during the process of which flanges can be flow-formed (rolled) on the upper ends of the liners as required, the bores of the liners are subjected to a form of honing which actually produces more of a knurling effect in that it slightly roughens the bore, although only by a matter of micro inches.
After this "honing' the bores are at their finished size less 0.003 in., the walls being 0.04 in. thick. The chroming process brings the bores up to their correct size, the layer of chrome being only 0.0015 in. thick, and the surface of the chrome reproducing exactly the original " roughened " surface beneath it. This roughening not only provides a key between the chrome and the machined mild-steel pressing but also forms minute pockets which never wear completely smooth, and so always provide reservoir space 828 for lubricating oil. After some hours running, the bores look smooth, but this appearance is deceptive for the pockets never disappear completely.
Thus, this patented thin-wall type of liner has the normal Cromard advantage of increased bore life compared with conventional cast-iron bores (the manufacturer's guarantee is valid for 100,000 miles), plus the added advantage of permitting increases in bore diarneter without changing the basic design of an engine.
The liners give production advantages as well. The small flange which can be formed at the top of the liner can eliminate the need for the upper face of the cylinder block to be recessed, so reducing machining costs, whilst, when incorporated in the design of new engine, more simple cylinder-block castings can be employed.
Although Cromard replacement liners can cost between 50 and 100 per cent. more than conventional replacement liners, this additional cost is usually soon repaid in terms of increased liner life. This is particularly so in the case of engines of vehicles engaged on concentrated stop-start operation. such as delivery vans and most types of municipal vehicle. This explains why such companies as Lewin Road Sweepers, Ltd., and Shelvoke and Drewry,. Ltd., have standardized on Cromard liners for all the engines used in their vehicle, whilst in this same field the pioneer work of F. Perkins, Ltd., must not be forgotten, particularly in the case of municipal vehicles.
The Cromard thin-wall liners do not replace the more conventional thick-wall steel hard-chrome-bore liners Which Laystall have been making for about 15 years, and indeed. cast-iron Cromard-processed liners are now to be found in recent engine designs such as last year's Leyland PowerPlus 0.680 diesel engine-. Nevertheless, it is a fairly safe assumption that the thin-wall type of liner could well take the place of all other types of dry liner, although engines designed around wet liners will not be able to incorporate the thin-wall variety.