Be prepared!
Page 42
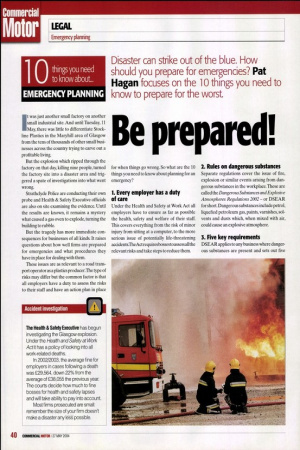
Page 43
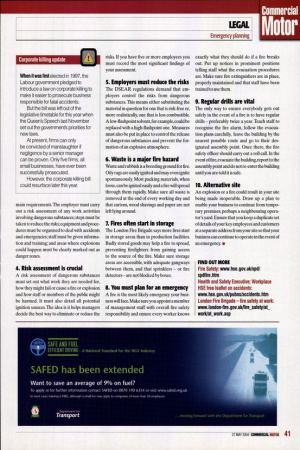
If you've noticed an error in this article please click here to report it so we can fix it.
Disaster can strike out of the blue. How should you prepare for emergencies? Pat Hagan focuses on the 10 things you need to
know to prepare for the worst.
It was just another small factory on another small industrial site. And until Tuesday, 11 May, there was little to differentiate Stockline Plastics in the Maryhill area of Glasgow from the tens of thousands of other small businesses across the country trying to carve out a profitable living.
But the explosion which ripped through the factory on that day, killing nine people, turned the factory site into a disaster area and triggered a spate of investigations into what went wrong.
Strathclyde Police are conducting their own probe and Health & Safety Executive officials are also on site examining the evidence. Until the results are known, it remains a mystery what caused a gas oven to explode, turning the building to rubble.
But the tragedy has more immediate consequences for businesses of all kinds. It raises questions about how well firms are prepared for emergencies and what procedures they have in place for dealing with them. These issues are as relevant to a road transport operator as a plastics producer.The type of risks may differ but the common factor is that all employers have a duty to assess the risks to their staff and have an action plan in place
for when things go wrong. So what are the 10 things you need to know about planning for an emergency? 1. Every employer has a duty of care
Under the Health and Safety at Work Act all employers have to ensure as far as possible the health, safety and welfare of their staff. This covers everything from the risk of minor injury from sitting at a computer, to the more serious issue of potentially life-threatening accidents.TheActrequiresbossestoassessallthe relevant risks and take steps to reduce them.
2. Rules on dangerous substances Separate regulations cover the issue of fire, explosion or similar events arising from dangerous substances in the workplace. These are called the Dangerous Substances and Explosive Atmospheres Regulations 2002 — or DSEAR for short. Dangerous substances include petrol, liquefied petroleum gas, paints, varnishes, solvents and dusts which, when mixed with air, could cause an explosive atmosphere. 3. Five key requirements DSEAR applies to any business where dangerous substances are present and sets out five
main requirements. The employer must carry out a risk assessment of any work activities involving dangerous substances; steps must be taken to reduce the risks; equipment and procedures must be organised to deal with accidents and emergencies; staff must be given information and training; and areas where explosions could happen must be clearly marked out as danger zones. 4. Risk assessment is crucial A risk assessment of dangerous substances must set out what work they are needed for, how they might fail or cause a fire or explosion and how staff or members of the public might be harmed. It must also detail all potential ignition sources. The idea is it helps managers decide the best way to eliminate or reduce the
risks. If you have five or more employees you must record the most significant findings of your assessment.
5. Employers must reduce the risks The DSEAR regulations demand that employers control the risks from dangerous substances. This means either substituting the material in question for one that is risk-free or, more realistically, one that is less combustible.
low-flashpoint solvent, for example, could be replaced with a high-flashpoint one. Measures must also be put in place to control the release of dangerous substances and prevent the formation of an explosive atmosphere.
6. Waste is a major fire hazard Waste and rubbish is a breeding ground for fire. Oily rags are easily ignited and may even ignite spontaneously. Most packing materials, when loose, can be ignited easily and a fire will spread through them rapidly. Make sure all waste is removed at the end of every working day and that cartons, wood shavings and paper are not left lying around. 7. Fires often start in storage
The London Fire Brigade says more fires start in storage areas than in production facilities. Badly stored goods may help a fire to spread, preventing firefighters from gaining access to the source of the fire. Make sure storage areas are accessible, with adequate gangways between them, and that sprinklers — or fire detectors — are not blocked by boxes. 8. You must plan for an emergency A tire is the most likely emergency your business will face. Make sure you appoint a member of management staff with overall fire safety responsibility and ensure every worker knows
exactly what they should do if a fire breaks out. Put up notices in prominent positions telling staff what the evacuation procedures are. Make sure fire extinguishers are in place, properly maintained and that staff have been trained to use them. 9. Regular drills are vital
The only way to ensure everybody gets out safely in the event of a fire is to have regular drills — preferably twice a year. Teach staff to recognise the fire alarm, follow the evacuation plans carefully, leave the building by the nearest possible route and go to their designated assembly point. Once there, the fire safety officer should carry out a roll call. In the event of fire, evacuate the building, report to the assembly point and do not re-enter the building until you are told it is safe. 10. Alternative site An explosion or a fire could result in your site being made inoperable. Draw up a plan to enable your business to continue from temporary premises, perhaps a neighbouring operator's yard. Ensure that you keep a duplicate set of details of your key employees and customers at a separate address from your site so that your business can continue to operate in the event of an emergency. • Accident investigation
The Health & Safety Executive has begun investigating the Glasgow explosion. Under the Health and Safety at Work Act it has a policy of looking into all work-related deaths.
In 2002/2003, the average fine for employers in cases following a death was £29,564, down 22% from the average of £38,055 the previous year. The courts decide how much to fine bosses for health and safety lapses and will take ability to pay into account.
Most firms prosecuted are small: remember the size of your firm doesn't make a disaster any less possible. Corporate killing update
When it was first elected in 1997, the Labour government pledged to introduce a law on corporate killing to make it easier to prosecute business responsible for fatal accidents.
But the bill was left out of the legislative timetable for this year when the Queen's Speech last November set out the government's priorities for new laws.
At present, firms can only be convicted of manslaughter if negligence by a senior manager can be proven. Only five firms, all small businesses, have ever been successfully prosecuted.
However, the corporate killing bill could resurface later this year. FIND OUT MORE Fire Safety: www.hse.gov.uk/spd/ spdfire.htm Health and Safety Executive; Workplace HSE free leaflet on accidents: www.hse.gov.uk/pubns/accidents.htm London Fire Brigade —fire safety at work: vinAnv.london-fire.gov.uk/fire_safety/at_ work/at_work.asp