Hitching a ride
Page 44
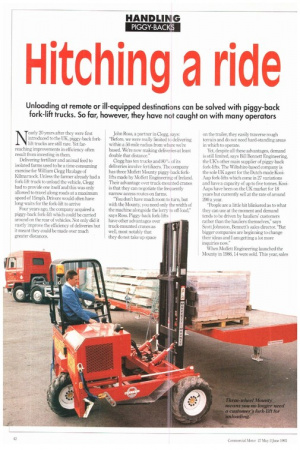
Page 45
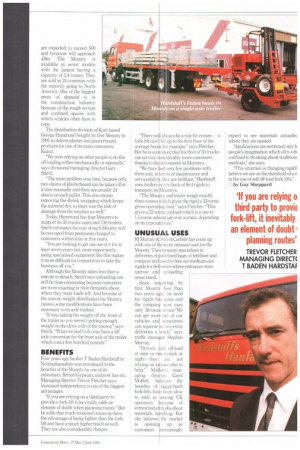
If you've noticed an error in this article please click here to report it so we can fix it.
Unloading at remote or ill-equipped destinations can be solved with piggy-back fork-lift trucks. So far, however, they have not caught on with many operators
Nearly 20 years after t hey were first introduced to the UK, piggy-back forklift trucks are still rare. Yet farreaching improvements in efficiency often result from investing in them.
Delivering fertilizer and animal feed to isolated farms used to be a tinw-consuming exercise for William Clegg Haulage of Kilmarnock. Unless the farmer already had a fork-lift truck to unload the vehicle, Clegg had to provide one itself and this was only allowed to travel along roads at a maximum speed of 15mph. Drivers would often have long waits for the fork-lift to arrive Four years ago, the company acquired a piggy-back fork-lift which could be carried around on the rear of vehicles. Not only did it vastly improve the efficiency of deliveries but it meant they could be made over much greater distances. John Ross, a partner in Clegg, says: "Before, we were really limited to delivering within a 50-mile radius from where we're based. We're now making deliveries at least double that distance."
Clegg has ten trucks and 80% of its deliveries involve fertilizers. The company has three Moffett Mounty piggy-back forklifts made by Moffett Engineering of Ireland. Their advantage over truck-mounted cranes is that they can negotiate the frequently narrow access routes on farms.
"You don't have much niorn to turn, but with the Mounty, you need only the width of the machine alongside the lorry to off-load," says Ross. Piggy-back fork-lifts have other advantages over truck-mounted cranes as well, most notably that they do not take up space on the trailer, they easily traverse rough terrain and do not need hard-standing areas in which to operate.
Yet, despite all these advantages, demand is still limited, says Bill Bennett Engineering, the UK's other main supplier of piggy-back fork-lifts. The Wiltshire-based company is the sole UK agent for the Dutch-made KooiAap fork-lifts which come in 27 variations and have a capacity of up to five tonnes. KooiAaps have been on the UK market for 18 years but currently sell at the rate of around 200 a year.
"People are a little hit blinkered as to what they can use at the moment and demand tends to be driven by hauliers' customers rather than the hauliers themselves," says Scott Johnston, Bennett's sales director. "But bigger companies are beginning to change their ideas and I am getting a lot more inquiries now."
When Moffett Engineering launched the Mounty in 1986, 14 were sold. This year, sales are expected to exceed 500 and turnover will approach am. The Mounty is available in seven models with the largest having a capacity of 2.4 tonnes. They are sold in 24 countries with the majority going to North America. One of the biggest areas of demand is in the construction industry because of the rough terrain and confined spaces with which vehicles often have to cope.
The distribution division of Kent-based George Hammond bought its first Mounty in 1991 to deliver plaster and plasterboard products for one of its main customers, Knauf.
"We were relying on other people to do the off-loading either mechanically or manually," says divisional managing director Gary Smith.
"The main problem was time, because only two sheets of plasterboard can be taken off at a time manually and there are usually 24 sheets on each pallet. This also means removing the shrink wrapping which keeps the material dry, so there was the risk of damage from the weather as well."
'May, Hammond has four Mountys to support its 35 tractor units and 130 trailers. Smith estimates the cost of each Mounty will be recouped from premiums charged to customers within four or five years.
"You are looking to get use out of it for at least seven years but, more importantly, using specialised equipment like this makes it more difficult for competitors to take the business off you."
Although the Mounty takes less than a minute to detach, Smith says unloading can still be time-consuming because customers are more exacting in their demands about where they want loads left. And because of the uneven weight distribution the Mounty causes, some modifications have been necessary to tri-axle trailers.
"It was taking the weight off the front of the trailer so you weren't getting enough weight on the drive axle of the tractor," says Smith. "What we had to do was have a lift axle conversion for the front axle of the trailer which cost a few hundred pounds."
BENEFITS
Four years ago haulier T Baden Hardstaff in Nottinghamshire was introduced to the benefits of the Mounty by one of its customers, British Gypsum, and now has six. Managing director Trevor Fletcher says increased independence is one of the biggest advantages.
"If you are relying on a third party to provide a fork-lift it inevitably adds an element of doubt when planning routes." But he adds that truck-mounted cranes do have the advantage of being lighter than the forklift and have a much higher reach as well. They are also considerably cheaper. "There wig always be a role for cranes — a fork-lift can't lift up to the first floor of the average house for example," says Fletcher. But he is convinced that his fleet of 35 trucks can service considerably more customers thanks to the investment in Mountys.
"We have had very few problems with them and, in tern is of maintenance and serviceability, they are brilliant." Hardstaff uses trailers on t 'ne back of 8x1 rigids to transport its Mountys.
"The Mount y and trailer weigh exactly three tonnes which gives the rigid a 32-tonne gross operating limit," says Fletcher. "This gives a V-tonne payload which is a one to 1.5-tonne advantage over a crane, depending on its type and size."
UNUSUAL USES
RJ Murray & Son of Carlisle has come up with one of the more unusual uses for the Mounty. Thecompany specialises in deliveries of palletised bags of fertiliser and compost and used to hire out medium-size rigids for deliveries where entrances were narrow and unloading areas small.
Since acquiring its first Mounty less than two years ago, he need for rigids has gone and the company n tw uses only 38-tonne artics."We can get more out of our vehicles and sometimes can squeeze in two extra deliveries a week," says traffic manager Stephen Murray.
"Drivers can off-load at nine or tan o'clock at night—they arc' not relying on anyone else to help." Moffett's managing director Carol Moffett, believes the benefits of piggy-back fork-lifts have been slow to sink in ,among UK operators beck use of entrenched attitudes about materials handling. But she believes tht. market is opening up as customers increasingly
expect to see materials unloadec where they are needed.
"Applications are restricted only b people's imagination which all to oft4 confined to thinking about traditionE methods," she says.
"This situation is changing rapidl believe we are on the threshold of a n in the use of self off-load fork-lifts." – by Guy Sheppard