A NOVEL BEARING FOR CHASSIS PARTS.
Page 12
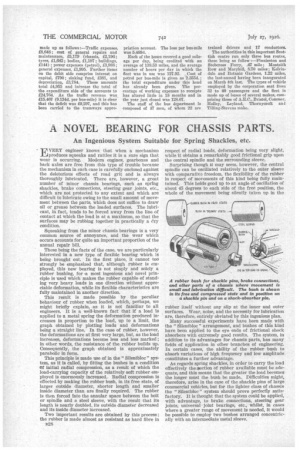
If you've noticed an error in this article please click here to report it so we can fix it.
An Ingenious System Suitable for Spring Shackles, etc.
-FAVERY engineer knows that when a mechanism 1 ' produces squeaks and rattles it is a Sure sign that wear is occurring. Modern engines, gearboxes and back axles are free from this type of trouble because the mechanism in each case is carefully enclosed against the deleterious effects of road grit and is always thoroughly lubricated. There are, however, a great number of minor chassis bearings, such as spring shackles, brake connections, steering gear joints, etc., which are not protected to any extent and which are difficult to lubricate owing to the small amount of movement between the parts, which does not suffice to draw oil or grease between the loaded surfaces. The lubricant, in fact, tends to be forced away from the line of contact at which the load is at a maximum, so that the surfaces may be rubbing together in practically a dry condition.
Squeaking from the minor chassis bearings is a very common source of annoyance, and the wear which occurs accounts for quite an important proportion of the annual repair bill.
These being the facts of the case, we are particularly interested in a new type of flexible bearing which being brought out. In the first place, it cannot too strongly be emphasized that, although rubber is employed, this new bearing is not simply and solely, a rubber bushing, for .a most ingenious and novel principle is used which makes the rubber capable of standing very heavy loads in one direction without appreciable deformation, while its flexible characteristics are fully maintained in another direction.
This result is made possible by the peculiar behaviour of rubber when loaded, which, perhaps, we might briefly explain, as it is not familiar to all engineers. It is a well-known fact that if a load is applied to a metal spring the deformation produced increases in proportion to the load, up to a limit, the graph obtained by plotting loads and deformations being a straight line. In the case of rubber, however, the deformations are at first very large, but, as the load increases, deformations become less and less marked ; in other words, the resistance of the rubber builds up. Consequently, the graph obtained is approximately parabolic in form.
This principle is made use of in the " Silentbloc " system, as it is called, by fitting the bushes in a condition It initial radial compression, as a result of which the load-carrying capacity of the relatively soft rubber employed is enormously increased. Radial compression is effected by making the rubber bush, in its free state, of larger outside diameter, shorter length and smaller inside diameter than are finally required. The rubber is then forced into the annular space between the bolt or spindle and a steel sleeve, with the result that its length is nearly doubled, its outside diameter decreased and its inside diameter increased.
Two important results are obtained by this process; the rubber is made almost as resistant as hard fibre in B28 respect of radial loads, deformation being very slight, while it obtains a remarkably good frictional grip upon the central spindle and the surrounding sleeve.
Surprising though it may seem, however, the central spindle can be oscillated relatively to the outer sleeve with comparative freedom, the flexibility of the rubber in respect of movements of this kind being fully maintained. This holds good up toan angle of oscillation of about 45 degrees to each side of the free position, the whole of the movement being silently taken up in the rubber itself without any slip at the inner and outer surfaces. Wear, noise, and the necessity for lubrication are, therefore, entirely obviated by this ingenious plan.
Many successful experiments have been made with the " Silentbloc " arrangement, and bushes of this kind have been applied to the eye ends of frictional shock absorbers with extremely good results. The system, in addition to its advantages for chassis parts, has many fields of application in other branches of engineering. In certain cases, the ability of the rubber bush to absorb variations of high frequency and low amplitude constitutes a further advantage.
As regards spring shackles, in order to carry the load effectively the section of rubber available must be adequate, and this means that the greater the load becomes the longer must the bush be made. Difficulties might, therefore, arise in the case of the shackle pins of large commercial vehicles, but for the lighter class of chassis the " Silentbloc " system should prove perfectly satisfactory. It is thought that the system could be applied, with advantage, to brake connections, steering gear joints, universal-joint bearings, etc., whilst, in cases where a greater range of movement is needed, it would be possible to employ two bushes arranged concentrically with an intermediate metal sleeve.