CRANE FRUEHAUF
Page 49
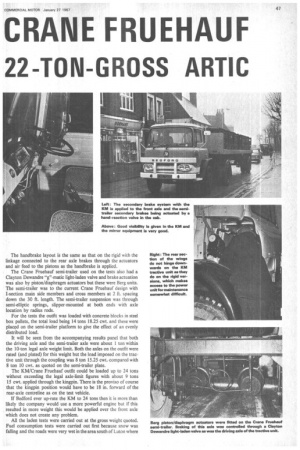
Page 48
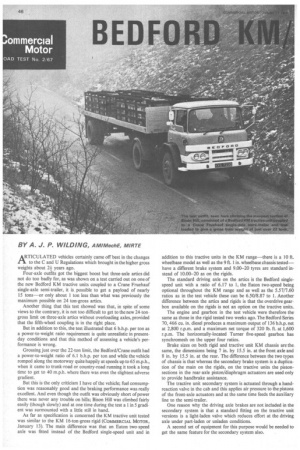
Page 50
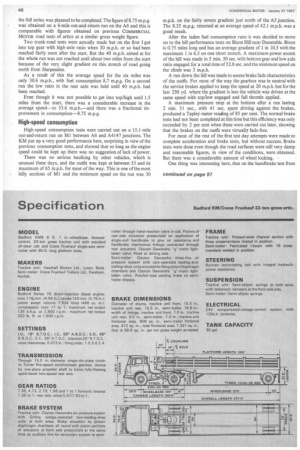
Page 53
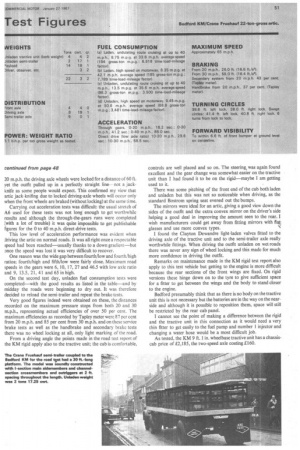
If you've noticed an error in this article please click here to report it so we can fix it.
22-TON-GROSS ARTIC
BY A. J. P. WILDING, ANUMechE, M1RTE AtTICULATED vehicles certainly came off best in the changes to the C and U Regulations which brought in the higher gross weights about 2+ years ago.
Four-axle outfits got the biggest boost but three-axle artics did not do too badly for, as was shown on a test carried out on one of the new Bedford KM tractive units coupled to a Crane Fruehauf single-axle semi-trailer, it is possible to get a payload of nearly 15 tons—or only about 1 ton less than what was previously the maximum possible on 24 ton-gross artics.
Another thing that this test showed was that, in spite of some views to the contrary, it is not too difficult to get to the new 24-tongross limit on three-axle artics without overloading axles, provided that the fifth-wheel coupling is in the right place.
But in addition to this, the test illustrated that 6 b.h.p. per ton as a power-to-weight ratio requirement is quite unrealistic in presentday conditions and that this method of assessing a vehicle's performance is wrong.
Grossing just over the 22-ton limit, the Bedford/Crane outfit had a power-to-weight ratio of 6.1 b.h.p. per ton and while the vehicle romped along the motorway quite happily at speeds up to 65 m.p.h., when it came to trunk-road or country-road running it took a long time to get to 40 m.p.h. where there was even the slightest adverse gradient.
But this is the only criticism I have of the vehicle; fuel consumption was reasonably good and the braking performance was really excellent. And even though the outfit was obviously short of power there was never any trouble on hills; Bison Hill was climbed fairly easily (though slowly) and at one time during the test a 1 in 5 gradient was surmounted with a little still in hand.
As far as specification is concerned the KM tractive unit tested was similar to the KM 16-ton-gross rigid (COMMERCIAL MOTOR, January 13). The main difference was that an Eaton two-speed axle was fitted instead of the Bedford single-speed unit and in addition to this tractive units in the KM range—there is a 10 ft. wheelbase model as well as the 9 ft. 1 in. wheelbase chassis tested have a different brake system and 9.00-20 tyres are standard instead of 10.00-20 as on the rigids.
The standard driving axle on the artics is the Bedford singlespeed unit with a ratio of 6.17 to 1, the Eaton two-speed being optional throughout the KM range and as well as the 5.57/7.60 ratios as in the test vehicle these can be 6.50/8.87 to 1. Another difference between the artics and rigids is that the overdrive gearbox available on the rigids is not an option on the tractive units.
The engine and gearbox in the test vehicle were therefore the same as those in the rigid tested two weeks ago. The Bedford Series 70, 466 Cu. in. diesel produces a maximum output of 136 b.h.p. net at 2,800 r.p.m. and a maximum net torque of 320 lb. ft. at 1,600 r.p.m. The horizontally-located Turner five-speed gearbox has synchromesh on the upper four ratios.
Brake sizes on both rigid and tractive unit KM chassis are the. same, the dimensions being 7 in. by 15.5 in. at the front axle and 8 in. by 15.5 in. at the rear. The difference between the two types of chassis is that whereas the secondary brake system is a duplication of the main on the rigids, on the tractive units the pistonsections in the rear-axle piston/diaphragm actuators are used only to provide handbrake assistance.
The tractive unit secondary system is actuated through a handreaction valve in the cab and this applies air pressure to the pistons of the front-axle actuators and at the same time feeds the auxiliary line to the semi-trailer.
One reason why the driving axle brakes are not included in the secondary system is that a standard fitting on the tractive unit versions is a light-laden valve which reduces effort at the driving axle under part-laden or unladen conditions.
A second set of equipment for this purpose would be needed to get the same feature for the secondary system also. The handbrake layout is the same as that on the rigid with the linkage connected to the rear axle brakes through the actuators and air feed to the pistons as the handbrake is applied.
The Crane Fruehauf semi-trailer used on the tests also had a Clayton Dewa.ndre "g"-matic light-laden valve and brake actuation was also by piston/diaphragm actuators but these were Berg units. The semi-trailer was to the current Crane Fruehauf design with I-section main side members and cross members at 2 ft. spacing down the 30 ft. length. The semi-trailer suspension was through semi-elliptic springs, slipper-mounted at both ends with axle location by radius rods.
For the tests the outfit was loaded with concrete blocks in steel box pallets, the total load being 14 tons 18.25 cwt. and these were placed on the semi-trailer platform to give the effect of an evenly distributed load.
It will be seen from the accompanying results panel that both the driving axle and the semi-trailer axle were about 1 ton within the 10-ton legal axle weight limit. Both the axles on the outfit were rated (and plated) for this weight but the load imposed on the tractive unit through the coupling was 8 ton 15.25 cwt. compared with 8 ton 10 cwt. as quoted on the semi-trailer plate.
The KM/Crane Fruehauf outfit could be loaded up to 24 tons without exceeding the legal axle-limit figures with about 9 tons 15 cwt. applied through the kingpin. There is the proviso of course that the kingpin position would have to be 18 in. forward of the rear-axle centreline as on the test vehicle.
If Bedford ever up-rate the KM to 24 tons then it is more than likely the company would use a more powerful engine but if this resulted in more weight this would be applied over the front axle which does not create any problem.
All the laden tests were carried out at the gross weight quoted. Fuel consumption tests were carried out first because snow was falling and the roads were very wet in the area south of Luton where
the full series was planned to be completed. The figure of 8.75 m.p.g. was obtained on a 6-mile out-and-return run on the A6 and this is comparable with figures obtained on previous COMMERCIAL MOTOR road tests of artics at a similar gross weight figure.
Two trunk-road tests were actually made but on the first I got into top gear with high-axle ratio when 30 m.p.h. or so had been reached fairly soon after the start. But the 40 m.p.h. aimed at for the whole run was not reached until about two miles from the start because of the very slight gradient on this stretch of road going north from Harpenden.
As a result of this the average speed for the six miles was only 30.6 m.p.h., with fuel consumption 8.7 m.p.g. On a second run the low ratio in the rear axle was held until 40 m.p.h. had been reached.
even though it was not possible to get into top/high until 1.5 miles from the start, there was a considerable increase in the average speed—to 33.6 m.p.h.—and there was a fractional improvement in consumption-8.75 m.p.g.
High-speed consumption High-speed consumption tests were carried out on a 15.1-mile out-and-return run on MI between A6 and A4147 junctions. The KM put up a very good performance here, surprising in view of the previous consumption tests, and showed that so long as the engine speed could be kept up there was no suggestion of lack of power.
There was no serious baulking by other vehicles, which is unusual these days, and the outfit was kept at between 55 and its maximum of 65 m.p.h. for most of the way. This is one of the most hilly sections of M1 and the minimum speed on the run was 30 m.p.h. on the fairly severe gradient just north of the A5 junction. The 8.35 m.p.g. returned at an average speed of 42.1 m.p.h. was a good result.
After the laden fuel consumption runs it was decided to move on to the hill performance tests on Bison Hill near Dunstable. Bison is 0.75 miles long and has an average gradient of 1 in 10.5 with the maximum 1 in 6.5 on one short stretch. A maximum-power ascent of the hill was made in 5 min. 50 sec. with bottom gear and low axle ratio engaged for a total time of 52.8 sec. and the minimum speed on the climb was 3 m.p.h.
A run down the hill was made to assess brake fade characteristics of the outfit. For most of the way the gearbox was in neutral with the service brakes applied to keep the speed at 20 m.p.h. but for the last 250 yd. where the gradient is less the vehicle was driven at the same speed with top/low engaged and full throttle applied.
A maximum pressure stop at the bottom after a run lasting 2 min. 51 sec., with 41 sec. spent driving against the brakes, produced a Tapley-meter reading of 85 per cent. The normal brake tests had not been completed at this time but this efficiency was only exceeded by 2 per cent when these were carried out later, showing that the brakes on the outfit were virtually fade-free.
For most of the rest of the first test day attempts were made to complete acceleration and brake tests, but without success. Brake tests were done even though the road surfaces were still very damp and reasonable figures, in view of the conditions, were obtained. But there was a considerable amount of wheel locking.
One thing was interesting here, that on the handbrake test from
20 m.p.h. the driving axle wheels were locked for a distance of 60 fl. yet the outfit pulled up in a perfectly straight line—not a jackknife as some people would expect. This confirmed my view that Etrtic jack-knifing due to locked driving-axle wheels will occur only when the front wheels are braked (without locking) at the same time.
Carrying out acceleration tests was difficult: the usual stretch of A6 used for these tests was not long enough to get worthwhile results and although the through-the-gears runs were completed with a lot of trouble) it was quite impossible to get publishable tures for the 0 to 40 m.p.h. direct-drive tests.
This low level of acceleration performance was evident when driving the artic on normal roads. It was all right once a respectable Teed had been reached—usually thanks to a down gradient—but Dnce the speed was lost it was very difficult to recover.
One reason was the wide gap between fourth/low and fourth/high ratios; fourth/high and fifth/low were fairly close. Maximum road speeds in the gears were 6, 10, 17, 27 and 46.5 with low axle ratio and 9, 13.5, 21, 41 and 65 in high.
On the second test day, unladen fuel consumption tests were completed—with the good results as listed in the table—and by midday the roads were beginning to dry out. It was therefore decided to reload the semi-trailer and repeat the brake tests.
Very good figures indeed were obtained on these, the distances recorded on the maximum pressure stops from both 20 and 30 m.p.h., representing actual efficiencies of over 50 per cent. The maximum efficiencies as recorded by Tapley meter were 87 per cent from 20 m.p.h. and 85 per cent from 30 m.p.h. and on these service brake tests as well as the handbrake and secondary brake tests there was no wheel locking at all, only light marking of the road.
From a driving angle the points made in the road test report of the KM rigid apply also to the tractive unit; the cab is comfortable, controls are well placed and so on. The steering, was again found excellent and the gear change was somewhat easier on the tractive unit than I had found it to be on the rigid—maybe I am getting used to it.
There was some pitching of the front end of the cab both laden and unladen but this was not so noticeable when driving, as the standard Bostrom spring seat evened out the bumps.
The mirrors were ideal for an attic, giving a good view down the sides of the outfit and the extra convex mirror on the driver's side helping a good deal in improving the amount seen to the rear. I wish manufacturers could get away from fitting mirrors with if glasses and use more convex types.
I found the Clayton Dewandre light-laden valves fitted to the driving axle of the tractive unit and to the semi-trailer axle really worthwhile fittings. When driving the outfit unladen on wet roads there was never any sign of wheel locking and this made for much more confidence in driving the outfit.
Remarks on maintenance made in the KM rigid test report also apply to this test vehicle but getting to the engine is more difficult because the rear sections of the front wings are fixed. On rigid versions these hinge down on to the tyre to give sufficient space for a fitter to get between the wings and the body to stand closer to the engine.
Bedford presumably think that as there is no body on the tractive unit this is not necessary but the batteries are in the way on the nearside and although it is possible to reposition them, space will still be restricted by the rear cab panel.
I cannot see the point of making a difference between the rigid and the tractive unit in this connection as it would need a very thin fitter to get easily to the fuel pump and number 1 injector and changing a water hose would be a most difficult job.
As tested, the KM 9 ft. 1 in. wheelbase tractive unit has a chassiscab price of £2,185, the two-speed axle costing £160.