A New Insulation System for Tankers
Page 33
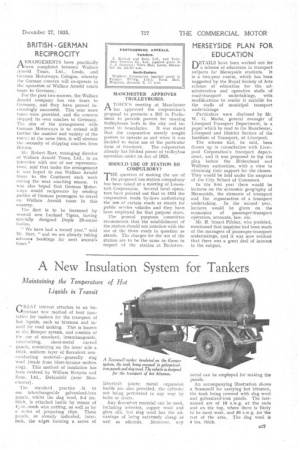
If you've noticed an error in this article please click here to report it so we can fix it.
GBEAT interest attaches to an important new method of heat insulation for tankers for the transport of hot liquids, such as bitumen and tar used for road making. This is known as the Kemper system, and consists of Site use of standard, interchangeable,
interlocking, sheet-metal curved panels, containing on the inner side a thick, uniform layer of flocculent nonconducting material—generally slag wool (made from blast-furnace molten sag). This method of insulation has been evolved by William Kenyon and Sons, Ltd., Dukinfield (near Manchester).
The standard practice is to use interchangeable galvanized-iron panels, whilst the slag wool, 3-4 ins. thick, is attached inside by means of 1.1,-in.-mesh wire netting, as well as by a series of projecting clips. These panels, as already indicated, interlock, the edges forming a series of
labyrinth joints; metal expansion bands are also provided, the cylinder not being perforated in any way by bolts or rivets.
Any flocculent material can be used, including asbestos, copper wool and glass silk, hut slag wool has the advantage of being extremely cheap as well as efficient. Moreover, any metal can be employed for making the panels.
An accompanying illustration shows a Scammell for carrying hot bitumen, the tank being covered with slag wool and galvanized-iron panels. The lastnamed are of 18 s.w.g. at the ends and on the top, where there is likely to be most wear, and 20 s.w.g. for -the rest of the area. The slag wool. is 4 ins. thick.