Raising the standards
Page 28
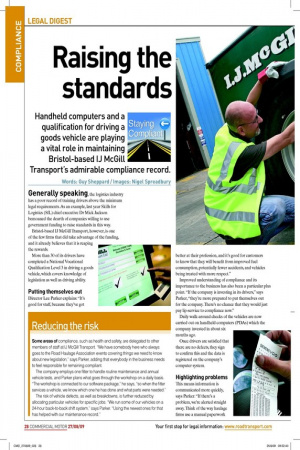
Page 29
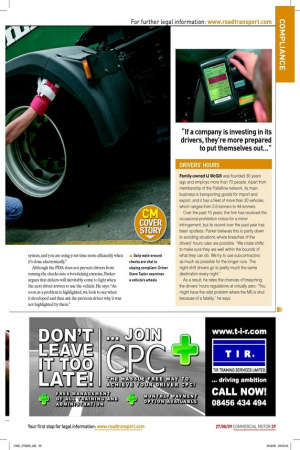
Page 30
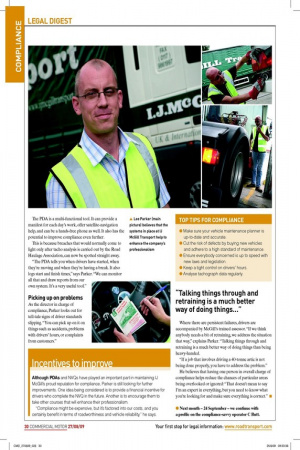
If you've noticed an error in this article please click here to report it so we can fix it.
Handheld computers and a qualification for driving a goods vehicle are playing a vital role in maintaining Bristol-based IJ McGill Transport’s admirable compliance record.
Words: Guy Sheppard / Images: Nigel Spreadbury Generally speaking, the logistics industry has a poor record of training drivers above the minimum
legal requirements. As an example, last year Skills for Logistics (SfL) chief executive Dr Mick Jackson bemoaned the dearth of companies willing to use government funding to raise standards in this way.
Bristol-based IJ McGill Transport, however, is one of the few irms that did take advantage of the funding, and it already believes that it is reaping the rewards.
More than 30 of its drivers have completed a National Vocational Qualiication Level 3 in driving a goods vehicle, which covers knowledge of legislation as well as driving ability.
Putting themselves out
Director Lee Parker explains: “It’s good for staff, because they’ve got better at their profession, and it’s good for customers to know that they will beneit from improved fuel consumption, potentially fewer accidents, and vehicles being treated with more respect.” Improved understanding of compliance and its importance to the business has also been a particular plus point. “If the company is investing in its drivers,” says Parker, “they’re more prepared to put themselves out for the company. There’s no chance that they would just pay lip-service to compliance now.” Daily walk-around checks of the vehicles are now carried out on handheld computers (PDAs) which the company invested in about six months ago.
Once drivers are satisied that there are no defects, they sign to conirm this and the data is registered on the company’s computer system.
Highlighting problems
This means information is communicated more quickly, says Parker. “If there’s a problem, we’re alerted straight away. Think of the way haulage irms use a manual paperwork system, and you are using your time more eficiently when it’s done electronically.” Although the PDA does not prevent drivers from turning the checks into a box-ticking exercise, Parker argues that defects will inevitably come to light when the next driver arrives to use the vehicle. He says: “As soon as a problem is highlighted, we look to see when it developed and then ask the previous driver why it was not highlighted by them.” The PDA is a multi-functional tool. It can provide a manifest for each day’s work, offer satellite-navigation help, and can be a hands-free phone as well. It also has the potential to improve compliance even further.
This is because breaches that would normally come to light only after tacho analysis is carried out by the Road Haulage Association, can now be spotted straight away.
“The PDA tells you when drivers have started, when they’re moving and when they’re having a break. It also logs start and inish times,” says Parker. “We can monitor all that and draw reports from our own system. It’s a very useful tool.”
Picking up on problems
As the director in charge of compliance, Parker looks out for tell-tale signs of driver standards slipping. “You can pick up on it on things such as accidents, problems with drivers’ hours, or complaints from customers.” Where there are persistent failures, drivers are accompanied by McGill’s trained assessor. “If we think anybody needs a bit of retraining, we address the situation that way,” explains Parker. “Talking things through and retraining is a much better way of doing things than being heavy-handed.
“If a job that involves driving a 40-tonne artic is not being done properly, you have to address the problem.”
He believes that having one person in overall charge of compliance helps reduce the chances of particular areas being overlooked or ignored: “That doesn’t mean to say I’m an expert in everything, but you need to know what you’re looking for and make sure everything is correct.” ■
● Next month – 24 September – we continue with a proSle on the compliance-savvy operator C Butt.
Reducing the risk
Some areas of compliance, such as health and safety, are delegated to other members of staff at IJ McGill Transport. “We have somebody here who always goes to the Road Haulage Association events covering things we need to know about new legislation,” says Parker, adding that everybody in the business needs to feel responsible for remaining compliant.
The company employs one fitter to handle routine maintenance and annual vehicle tests, and Parker plans what goes through the workshop on a daily basis. “The workshop is connected to our software package,” he says, “so when the fitter services a vehicle, we know which one he has done and what parts were needed.” The risk of vehicle defects, as well as breakdowns, is further reduced by allocating particular vehicles for specific jobs. “We run some of our vehicles on a 24-hour back-to-back shift system,” says Parker. “Using the newest ones for that has helped with our maintenance record.”
DRIVERS’ HOURS
Family-owned LJ McGill was founded 30 years ago and employs more than 70 people. Apart from membership of the Palletline network, its main business is transporting goods for import and export, and it has a fleet of more than 30 vehicles, which ranges from 3.5-tonners to 44-tonners.
Over the past 10 years, the firm has received the occasional prohibition notice for a minor infringement, but its record over the past year has been spotless. Parker believes this is partly down to avoiding situations where breaches of the drivers’ hours rules are possible. “We rotate shifts to make sure they are well within the bounds of what they can do. We try to use subcontractors as much as possible for the longer runs. The night-shift drivers go to pretty much the same destination every night.” As a result, he rates the chances of breaching the drivers’ hours regulations at virtually zero. “You might have the odd problem where the M5 is shut because of a fatality,” he says.
TOP TIPS FOR COMPLIANCE
● Make sure your vehicle maintenance planner is up-to-date and accurate.
● Cut the risk of defects by buying new vehicles and adhere to a high standard of maintenance.
● Ensure everybody concerned is up to speed with new laws and legislation.
● Keep a tight control on drivers’ hours.
● Analyse tachograph data regularly.
Incentives to improve
Although PDAs and NVQs have played an important part in maintaining IJ McGill’s proud reputation for compliance, Parker is still looking for further improvements. One idea being considered is to provide a financial incentive for drivers who complete the NVQ in the future. Another is to encourage them to take other courses that will enhance their professionalism.
“Compliance might be expensive, but it’s factored into our costs, and you certainly benefit in terms of roadworthiness and vehicle reliability,” he says.