ON THE MIND
Page 36
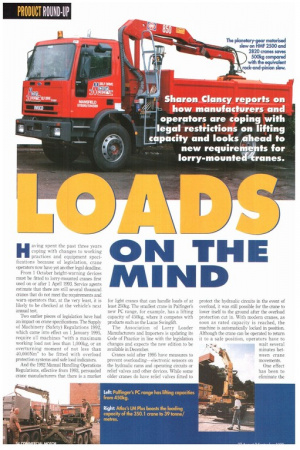
Page 37
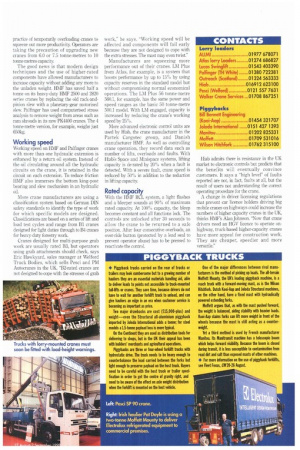
If you've noticed an error in this article please click here to report it so we can fix it.
Sharon Clancy reports on how manufacturers and operators are coping with legal restrictions on lifting pacify and looks /ahead to new requireirejnits for lorry-mounteiiiranes.
Having spent the past three years coping with changes to working practices and equipment specifications because of legislation, crane operators now have yet another legal deadline.
From 1 October height-warning devices must be fitted to lorry-mounted cranes first used on or after 1 April 1993. Service agents estimate that there are still several thousand cranes that do not meet the requirements and warn operators that, at the very least, it is likely to be checked at the vehicle's next annual test.
Two earlier pieces of legislation have had an impact on crane specifications. The Supply of Machinery (Safety) Regulations 1992, which came into effect on 1 January 1995, require all machines "with a maximum working load not less than 1,000kg, or an overturning moment of not less than 40,000Nin" to be fitted with overload protection systems and safe load indicators.
And the 1992 Manual Handling Operations Regulations, effective from 1993, persuaded crane manufacturers that there is a market for light cranes that can handle loads of at least 250kg. The smallest crane in Palfinger's new PC range, for example, has a lifting capacity of 450kg, where it competes with products such as the Lucas Swinglift.
The Association of Lorry Loader Manufacturers and Importers is updating its Code of Practice in line with the legislation changes and expects the new edition to be available in December.
Cranes sold after 1995 have measures to prevent overloading—electronic sensors on the hydraulic rams and operating circuits or relief valves and other devices. While some older cranes do have relief valves fitted to
protect the hydraulic circuits in the event of overload, it was still possible for the crane to lower itself to the ground after the overload protection cut in. With modern cranes, as soon as rated capacity is reached, the machine is automatically locked in position. Although the crane can be operated to return it to a safe position. nperators have to lo wait several minutes between crane movements.
One effect has been to eliminate the practice of temporarily overloading cranes to squeeze out more productivity. Operators are taking the precaution of upgrading new cranes from 6.0 or 7.5 tonne-metres to 10 tonne-metres capacity.
The good news is that modern design techniques and the use of higher-rated components have allowed manufacturers to increase capacity without adding any more to the unladen weight. HMF has saved half a tonne on its heavy-duty HMF 2500 and 2820 series cranes by replacing the old rack-andpinion slew with a planetary-gear motorised slew. Palfinger has used computerised stress analysis to remove weight from areas such as ram shrouds in its new PK4400 cranes. The 4 tonne-metre version, for example, weighs just 650kg.
Working speed
Working speed on lEVIF and Palfinger cranes with more than one hydraulic extension is enhanced by a return oil system. Instead of the oil circulating around all the hydraulic circuits on the crane, it is retained in the circuit on each extension. To reduce friction HMF also immerses the bottom king-post bearing and slew mechanism in an hydraulic oil.
More crane manufacturers are using a classification system based on German DIN safety standards to identify the type of work for which specific models are designed. Classifications are based on a series of lift and load test cycles and range from B1 cranes designed for light duties through to 134 cranes for heavy-duty forestry work.
Cranes designed for multi-purpose grab work are usually rated B3, but operators using grab attachments should check, says Eric Hawkyard, sales manager at Welford Truck Bodies, which sells Pesci and PM Autocranes in the UK. "B2-rated cranes are not designed to cope with the stresses of grab work," he says. "Working speed will be affected and components will fail early because they are not designed to cope with the extra stresses. The mast may even twist."
Manufacturers are squeezing more performance out of their cranes. LM Plus from Atlas, for example, is a system that boosts performance by up to 15% by using capacity reserves in the standard model but without compromising normal economical operations. The LM Plus 56 tonne-metre 560.1, for example, has the same power and speed ranges as the basic 50 tonne-metre 500.1 model. With LM engaged, capacity is increased by reducing the crane's working speed by 25%.
More advanced electronic control units are used by Hiab, the crane manufacturer in the Partek Cargotec group, and Danish manufacturer HMF. As well as controlling crane operation, they record data such as number of lifts, overloads and faults. With Hiab's Space and Minispace systems, lifting capacity is de-rated by 20% when a fault is detected. With a severe fault, crane speed is reduced by 50% in addition to the reduction in lifting capacity.
Rated capaci
With the IIMF RCL system, a light flashes and a bleeper sounds at 90% of maximum rated capacity. At 100% capacity, the bleep becomes constant and all functions lock. The controls are unlocked after 30 seconds to allow the crane to be returned to a safe position. After four consecutive overloads, an over-ride button (protected by a lead seal to prevent operator abuse) has to be pressed to reactivate the control. Hiab admits there is resistance in the UK market to electronic controls but predicts that the benefits will eventually convince customers. It says a "high level" of faults reported are not, in fact, faults at all, but the result of users not understanding the correct operating procedure for the crane.
A change in driver licensing regulations that prevent car licence holders driving big mobile cranes on highways could increase the numbers of higher capacity cranes in the UK, thinks lii4F's Alan Johnson. "Now that crane drivers need an HGV licence to operate onhighway, truck-based higher-capacity cranes have more appeal for construction work. They are cheaper, speedier and more versatile."
PIGGYBACK TRUCKS
• Piggyback trucks carried on the rear of trucks or trailers may look cumbersome but to a growing number of hauliers they are an essential materials handling aid, able to deliver loads to points not accessible to truck-mounted tail-lifts or cranes. They save time, because drivers do not have to wait for another forklift truck to unload, and can give hauliers an edge in an era when customer service is becoming as important as price.
Two major drawbacks are cost (lS,000-plus) and weight—even the Structural all-aluminium piggyback imported by Joloda International adds a tonne; for steel models a 1.5-tonne payload loss is more typical.
On the Continent they are used as distribution tools for delivering to shops. but in the UK their appeal has been with builders' merchants and agricultural operations.
Piggybacks are three or four-wheel forklift trucks with hydrostatic drive. The truck reeds to be heavy enough to counterbalance the load carried between the forks but light enough to preserve payload on the host truck. Buyers need to be careful with the host truck or trailer specification in order to get the centre of gavity right, and need to be aware of the effect on axle weight distribution
when L..1,144 ■.r. 1.IIC 101.11. ra 1111.11.1111.,. VII UM !Mak TV11161V. One of the major differences between rival manufacturers is the method of picking up loads. The all-terrain Moffett Mounty, the UK's leading piggyback machine, is a reach truck with a forward-moving mast., as is the Wilson Hitchfork. Butch lioni-Aap and Joloda Shamtural machines, on the other hand, have a fixed mast with hydraulically powered extending forks.
Moffett argues that, as with the mast pushed forward, the weight is balanced, aiding stability with heavier loads. Kooi-bap claims forks can lift more weight in front of the wheels because the mast is still acting as a counterweight
Yet a third method is used by french manufacturer Manitou. Its Manitransit machine has a telescopic boom which helps forward visibility. Because the boom is closed during transit, it is less susceptible to contamination from road dirt and salt than exposed masts of other machines.
• For more information on the use of piggyback forklifts. see Fleet FOCUS, CM 20-26 August