Our independent
Page 81
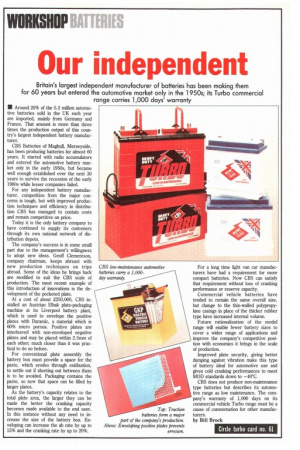
If you've noticed an error in this article please click here to report it so we can fix it.
Britain's largest independent manufacturer of batteries has been making them for 60 years but entered the automotive market only in the 1950s; its Turbo commercial range carries 1,000 days' warranty
• Around 20% of the 5.2 million automotive batteries sold in the UK each year are imported, mainly from Germany and France. That amount is more than three times the production output of this country's largest independent battery manufacturer.
CBS Batteries of Maghull, Merseyside, has been producing batteries for almost 60 years. It started with radio accumulators and entered the automotive battery market only in the early 1950s, but became well enough established over the next 30 years to survive the recession of the early 1980s while lesser companies failed.
For any independent battery manufacturer, competition from the major concerns is tough, but with improved production techniques and efficiency in distribution CBS has managed to contain costs and remain competitive on price.
Today it is the only battery company to have continued to supply its customers through its own national network of distribution depots.
The company's success is in some small part due to the management's willingness to adopt new ideas. Geoff Clementson, company chairman, keeps abreast with new production techniques on trips abroad. Some of the ideas he brings back are modified to suit the CBS scale of production. The most recent example of this introduction of innovations is the development of the pocketed plate.
At a cost of about £250,000, CBS installed an Austrian Elbak plate-packaging machine at its Liverpool battery plant, which is used to envelope the positive plates with Dararnic, a material which is 60% micro porous. Positive plates are interleaved with non-enveloped negative plates and may be placed within 2.5mm of each other, much closer than it was practical to do so before.
For conventional plate assembly the battery box must provide a space for the paste, which erodes through oxidisation, to settle out if shorting out between them is to be avoided. Packaging contains the paste, so now that space can be filled by larger plates.
As the battery's capacity relates to the total plate area, the larger they can be made the better the cranking capacity becomes made available to the end user. In this instance without any need to increase the size of the battery box. Enveloping can increase the ah rate by up to 15% and the cranking rate by up to 20%. For a long time light van car manufacturers have had a requirement for more compact batteries. Now CBS can satisfy that requirement without loss of cranking performance or reserve capacity.
Commercial vehicle batteries have tended to remain the same overall size, but change to the thin-walled polypropylane casings in place of the thicker rubber type have increased internal volume.
Future rationalisation of the model range will enable fewer battery sizes to cover a wider range of applications and improve the company's competitive position with economies it brings in the scale of production.
Improved plate security, giving better damping against vibration make this type of battery ideal for automotive use and gives cold cranking performances to meet MOD standards down to —40°C.
CBS does not produce non-maintenance type batteries but describes its automotive range as low maintenance. The company's warranty of 1,000 days on its commercial vehicle Turbo range must be a cause of consternation for other manufacturers.
by Bill Brock