New look fuE0 pump from CAV
Page 23
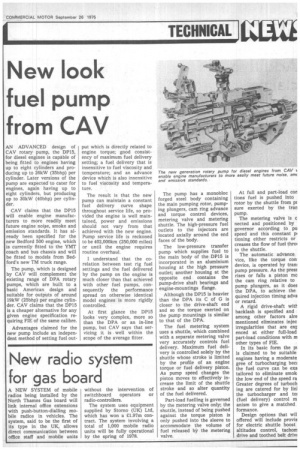
If you've noticed an error in this article please click here to report it so we can fix it.
AN ADVANCED design of CAV rotary pump, the 0P15, for diesel engines is capable of being fitted to engines having up to eight cylinders and producing up to 26kW (35bhp) per cylinder. Later versions of the pump are extcted to cater for engines, aga in having up to eight cylinders, but producing up to 30kW (40bhp) per cylinder.
CAV claims that the DP15 will enable engine manufacturers to more readily meet future engine noise, smoke and emission standards. It has already been specified for the new Bedford 500 engine, which is currently fitted to the YMT coach and bus chassis and will be fitted to Models from Bedford's new TM truck range.
The pump, which is designed by CAV will complement the existing range of DPA rotary pumps, which are built to a basic American design and suitable for outputs of around 19kW (25bhp) per engine cylinder. CAV claims that the DP15 is a cheaper alternative for any given engine specification requiring FIE of the same calibre.
Advantages claimed for the new pump include an independent method of setting fuel out put which is directly related to engine torque; good consistency of maximum fuel delivery setting; a fuel delivery that is insensitive to fuel viscosity and temperature; and an advance device which is also insensitive to fuel viscosity and temperature.
The result is that the new pump can maintain a constant fuel delivery curve shape throughout service life, so provided the engine is well maintained, power and emissions should not vary from that achieved with the new engine. Pump service life is reckoned to be 402,000km (250,000 miles) or until the engine requires routine overhaul, I understand that the corelation between test rig fuel settings and the fuel delivered by the pump on the engine is much closer than that achieved with other fuel pumps, consequently the performance spread on otherwise identical model engines is more rigidly controlled.
At first glance the DP15 looks very complex, more so than the DPA or an in-line pump, hut CAV says that servicing it is well within the scope of the average fitter. The pump has a monobloc forged steel body containing the main pumping rotor, pumping plungers, cam ring advance and torque control devices, metering valve and metering shuttle. The high-pressure fuel outlets to the injectors are located axially around the end faces of the body.
The low-pressure transfer pump which supplies fuel to the main body of the DP15 is incorporated in an aluminium housing at the high pressure outlet; another housing at the opposite end contains the pump-drive shaft bearings and engine-mountings flange.
Although the DP15 is heavier than the DPA its C of G is closer to the drive-shaft end and so the torque exerted on the pump mountings is similar to that of the DPA.
The fuel metering system uses a shuttle, which combined with a separate metering valve very accurately controls fuel delivery. Maximum fuel delivery is controlled solely by the shuttle whose stroke is limited by the profile of an engine torque or fuel delivery piston. As pump speed changes the piston moves to effectively increase the limit of the shuttle stroke and so alter quantity of the fuel delivered.
Part-load fuelling is governed by the metering valve only; the shuttle, instead of being pushed against the torque piston is only pushed into the sleeve to accommodate the volume of fuel released by the metering valve. At full and part-load cor tions fuel is pushed into rotor by the shuttle from pi sure exerted by the tran pump.
The metering valve is c nected and positioned by governor according to pu speed and this constant pi tioning either restricts or creases the flow of fuel throi to the shuttle.
The automatic advance vice, like the torque con. device, is operated by trail: pump pressure. As the press rises or falls a piston mo the cam ring relative to pump plungers, as it does the DPA, to achieve the quired injection timing adva or retard.
A rigid drive-shaft witt. backlash is specified and among other factors alre mentioned eliminates injec irregularities that are exc enced at either full-load part-load conditions with m other types of FIE.
In its basic form the pi is claimed to be suitable engines having a moderate gree of turbocharging beck the fuel curve can be exa tailored to eliminate smok the low end of the speed ra Greater degrees of turboch ing are catered for by lin] the turbocharger and toi (fuel delivery) control m anism to give a matched formance.
Design options that wil offered will include provis for electric shuttle boost altitudes control, tachorr drive and toothed belt drive