GIVE US EASIER )ELIVERIES
Page 124
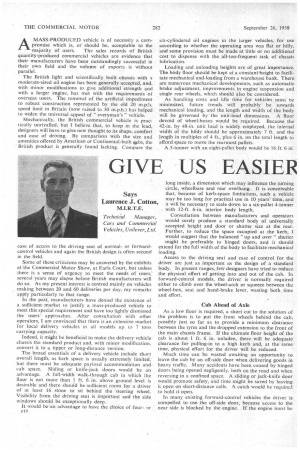
Page 125
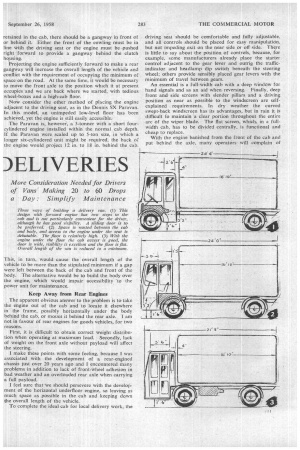
Page 126
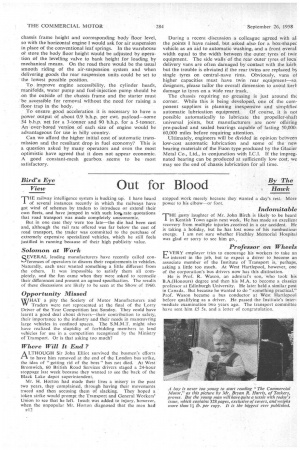
If you've noticed an error in this article please click here to report it so we can fix it.
AMASS-PRODUCED vehicle is of necessity a compromise which is, or should be, acceptable to the
majority of users. The sales records of British quantity-produced commercial vehicles are evidence that their manufacturers have been outstandingly successful in their own field and the volume of exports is without parallel.
The British light and scientifically built chassis with a moderate-sized oil engine has been generally accepted, and, with minor modifications to give additional strength and with a larger engine, has met with the requirements of overseas users. The removal of the artificial impediment to robust construction represented by the old 20 m.p.h. speed limit in Britain (now raised to 30 m.p.h.) has helped to widen the universal appeal of " everyman's " vehicle.
Mechanically, the British commercial vehicle is practically unrivalled, but I believe that, to keep in the lead, designers will have to give new thought to its shape, comfort and ease of driving. By comparison with the size and amenities offered by American or Continental-built gibs, the British product is generally found lacking. Compare the ease of access to the driving seat of normalor forwardcontrol vehicles and again the British design is often second in the field.
Some of these criticisms may be answered by the exhibits at the Commercial Motor Show, at Earls Court, but unless there is a sense of urgency to meet the needs of users, several years may elapse before British manufacturers will do so. As my present interest is centred mainly on vehicles making between 20 and 60 deliveries per day, my remarks apply particularly to that range.
In the past, manufacturers have denied the existence of a sufficient market to justify a mass-produced vehicle to. meet this special requirement and have too lightly dismissed the users' approaches. After consultation with other operators, I am convinced that there is an extensive market for local delivery vehicles in all models up to 7 tons carrying capacity.
Indeed, it might be beneficial to make the delivery vehicle chassis the standard product and, with minor modification, convert it to a tipper or long-distance version.
The broad essentials of a delivery vehicle include short overall length, as kerb space is usually extremely limited, but there must be adequate payload accommodation and cab space. Sliding or knife-jack doors would be an advantage. A full-width walk-through cab in which the floor is not more than 1 ft. 6 in. above ground level is desirable and there should be sufficient room for a driver of at least 16 stone to sit behind the steering wheel. Visibility from the driving seat is important and the side windows should be exceptionally deep.
It would be'an advantage to have the choice of fouror F10 six-cylindered oil engines in the larger vehicles, for use according to whether the operating area was flat or hilly, and some provision must be made at little or no additional cost to dispense with the all-too-frequent task of chassis lubrication. Loading and unloading heights are of great importance. The body floor should be kept at a constant -height to facilitate mechanical end-loading from a warehouse bank. There are numerous mechanical developments, such as automatic brake adjustment, improvements in engine suspension and single rear wheels, which should also be considered.
As handling costs and idle time for vehicles must be minimized, future trends will probably be towards mechanical loading, and the length and width of the body will be governed by the unit-load dimensions. A floor devoid of wheel-boxes would be required. Because the 42-in. by 48-in, unit load is widely employed, the internal width of the b6's:1y should be approximately 7 ft. and the length in multiples of 4 ft., plus 6 in. on the total length to afford space to move the rearmost pallets.
A 5-tonner with an eight-pallet body would be 16 ft. 6 in.
long inside, a dimension which may influence the turning circle, wheelbase and rear overhang. It is conceivable that, because of kerb-space limitations, such a vehicle may be too long for practical use in 10 years' time, and it will be necessary to scale down to a six-pallet 4-tonner with 12-ft. 6-in, interior body length.
Consultation between manufacturers and operators would surely produce a standard body of universally accepted height and door or shutter size at the rear. Further, to reduce the space occupied at the kerb, I would suggest that the balanced "up and over" shutter might be preferable to hinged doors, and it should extend for the full width of the body to facilitate mechanical loading.
Access to the driving seat and ease of control for the driver are just as important as the design of a standard body. In present ranges, few designers have tried to reduce the physical effort of getting into and out of the cab. In forward-co'ntrol models, the driver is normally required either to climb over the wheel-arch or squeeze between the wheel-box, seat and hand-brake lever, wasting both time and effort.
Cab Ahead of Axle As a low floor is required, a short cut to the solution of the problem is to put the front wheels behind the cab, possibly just so far as to provide a minimum clearance between the tyres and the dropped extension to the front of the main chassis frame. If the ultimate floor height of the cab is about 1 ft. 6. in. unladen, there will be adequate clearance for pulling-in to a high kerb and, at the same time, physical effort for the driver will be reduced.
Much time can be wasted awaiting an opportunity to leave the cab by an off-side door when delivering goods in heavy traffic. Many accidents have been caused by hinged doors being opened negligently, both on the road and when reversing in a confined space. A sliding or jack-knife door would promote safety, and time might be saved by leaving it open on short-distance calls. A catch would be required to hold it open.
In many existing forward-control vehicles the driver is compelled to use the off-side door, because access to the near side is blocked by the engine. If the engine must be retained in the cab, there should be a gangway in front of or behind it. Either the front of the cowling must be in line with the driving seat or the engine must be -pushed right •forward to provide a gangway behind the clutch housing.
Projecting the engine sufficiently forward to make a rear gangway will increase the overall length of the vehicle and conflict with the requirement of occupying the minimum of space on the road. At the same time, it would be necessary to move the front axle to the position which it at present occupies and we are back where we started, with tedious wheel-boxes and a high-cab floor.
Now consider the other method of placing the engine adjacent to the driving seat, as in the Dennis SX Paravan. In this model, an unimpeded low-level floor has been achieved, yet the engine is still easily accessible, The Paravan is, however, a 3-tonner with a short fourcylindered engine installed within the normal cab depth. If the Paravan were scaled up to 5-ton size, in which a longer six-cylindered unit might be required, the back or the engine would project 12 in. to 18 in. behind the cab.
This, in turn, would cause the overall length of the vehicle to be more than the stipulated minimum if a gap were left between the back of the cab and front of the body. The alternative would be to build the body over the engine, which would impair accessibility "to the power unit for maintenance.
Keep Away from Rear Engines The apparent obvious answer to the problem is to take the engine out of the cab and to locate it elsewhere in the frame, possibly horizontally under the body behind the cab, or mount it behind the rear axle. 1 am not in favour of rear engines for goods vehicles, for two reasons.
First, it is difficult to obtain correct weight distribution when operating at maximum load. Secondly, lack of weight on the front axle without payload will affect the steering.
I make these points with some feeling, because I was associated with the development of a rear-engined chassis just over 20 years ago and I encountered many problems in addition to lack of front-wheel adhesion in bad weather and an overloaded rear axle when carrying a full payload.
I feel sure that we should persevere with the development of the horizontal underfloor engine, so leaving as much space as possible in the cab and keeping down the overall length of the vehicle.
To complete the ideal cab for local delivery work, the driving seat should be comfortable and fully adjustable, and all controls should be placed for easy manipulation, but not impeding exit on the near side or off side. There is little to say about the position of controls, because, for example, some manufacturers already place the starter control adjacent to the gear lever and outrig the trafficindicator and headlamp dip switch beneath the steering wheel; others provide sensibly placed gear levers with the minimum of travel between gears.
An essential is a full-width cab with a deep window for hand signals and as an aid when reversing. Finally, deep front and side screens with slender pillars and a driving position as near as possible to the windscreen are selfexplained requirements. In dry weather the curved swept-back windscreen has its advantages, but in rain it is difficult to maintain a clear portion throughout the entire arc of the wiper blade. The flat screen, which, in a fullwidth cab, has to be divided centrally, is functional and cheap to replace.
With the engine banished from the front of the cab and put behind the axle, marry operators will coMplain of chassis frame height and corresponding body floor level, so with the horizontal engine 1 would ask for air suspension in place of the conventional leaf springs. In the warehouse or store the body floor height would be adjusted by operation of the levelling valve to bank height for loading by mechanical means. On the road there would be the usual smooth riding of the air-suspension system and when delivering goods the rear suspension units could be set to the lowest possible position. • To improve engine accessibility, the cylinder heads, manifolds, water pump and fuel-injection pump should be on the outside of the chassis frame and the starter must be accessible for removal without the need for raising a • floor, trap in the body.
To ensure good acceleration it is necessary to have a power output of about 0.9 b.h.p. per cwt. paYload--some 54 b.h.p. net for a 3-tormer and 90 b.h.p. for a 5-toriner. An 'over-bored version of each size of engine would be advantageous for use in hilly country.
Can we afford the higher initial cost of automatic transmission and the resultant drop in fuel economy? This is a question asked by many operators and even the most optimistic have agreed that it does not appear economic. A good constant-mesh gearbox seems to be most satisfactory. During a recent discussion a colleague agreed with all the points I have raised, but asked also for a box-shapec vehicle as an aid to automatic washing, and a front overall width equal to the width between the outer tyres of twin equipment. The side walls of the rear outer tyres of local delivery vans are of ten damaged by contact with the kerb but the trouble is obviated if the rear twins are replaced b3i single tyres on central-nave rims. Obviously, vans at higher capacities must have twin rear equipment--so, designers, please taffor the overall dimension to avoid kerb damage to tyres on a wide rear track.
The chassis requiring no greasing is just around thc corner. While this is being developed, one of the component suppliers is planning inexpensive and simplified automatic lubrication equipment. Of course, it is not possible automatically to lubricate the propeller-shaft universal joints, but manufacturers are now offering 'pre-packed and sealed bearings capable of lasting 50,00060,000 miles before requiring attention.
Ultimately, engineers will be divided in opinion between low-cost automatic lubrication and some of the new bearing materials of the Fuon type produced by the Glacier Metal Co., Ltd., in conjunction with I,C.I. If the impregnated bearing can be produced at sufficiently low cost, we may see the end of chassis lubrication for all time.