New Derusting
Page 37
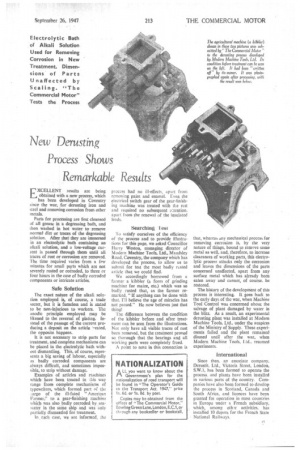
If you've noticed an error in this article please click here to report it so we can fix it.
Process Shows Remarkable Results
r XCELLENT results are being E., obtained with a new process,, which
has, been developed in Coventry since the war, for derusting iron and steel and removing corrosion from other metals.
Parts for processing are first cleansed of all grease in a degreasing bath, and then washed in hot water to remove normal dirt or traces of the degreasing solution. After that they are immersed in an electrolytic bath containing an alkali solution, and a low-voltage current is passed through them until all traces of rust or corrosion are removed. The time required varies from a few minutes for small parts which are not severely rusted or corroded, to three or four hours in the case of badly corroded components or intricate articles.
Safe Solution
The exact nature of the alkali solution employed is, of course, a trade secret, but it is furneless and is stated to be non-injurious to workers. The anodic principle employed may be likened to the reversal of plating. Insteadof the pas.sage of the current producing a deposit on the article 'reated, the opposite happens.
It is not necessary to strip parts for treatment, and complete mechanisms can he placed in the electrolytic bath without dismantling. This, of course, represents a big saving of labour, especially as badly corroded components are always difficult, and sometimes impossible, to strip without damage.
Examples of articles and machines whichhave been treated in ',his. way range from complete mechanisms of typewriters, which formed part of .the Jargo of the ill-fated 'American Farmer," to a gear-finishing machine which was also badly corroded. by .seawater in the same ship and was only partially dismantled for treatment.
In each case, we are informed, ',he
process had no ill-effects, apart from removing paint and enamel. Even the electrical switch gear of the gear-finishing machine was treated with the rest and required no subsequent attention. apart from the renewal of the insulated leads.
Searching less
To satisfy ourselves of the efficiency of the process and to provide illustrations for this page, we asked Councillor Harry Weston, managing director of Modern Machine Took, Ltd.,. Maudsley Road, Coventry, the company which has developed the process, to allow us to submit for test the most badly ri,sted article that we could find.
We accordingly borrowed from a farmer a kibbler (a form of grinding machine for maize, etc.) which was so badly Justed that, as the farmer remarked, "if anything Can be done with
that, believe the age of miracles has not passed." He now believes just that thing?
The difference between the condition of the kibbler before and after treatment can be seen from the illustrations, Not only have all visible traces of rust been removed, but the treatment proved so. thorough that the bearings and all working parts were completely freed. . A point to note in this. connection is that, whereas any mechanical process for removing corrosion is, by the very nature of things, bound toremove some metal as well, and, therefore, to increase clearances of working parts, this electrolytic process attacks only the corrosion and leaves the dimensions of the parts concerned unaffected, apart from any surface metal which. has. already been eaten away and cannot, of course, be restored..
The history of the development of this process is interesting. It goes back to the early days of the war, when Machine Tool Control was, concerned about the salvage of plant dameged by water in the blitz. As a result, an experimental derusting. plant was installed at Modern Machine Tools, Ltd., under the auspices of the Ministry of Supply. These experiments failed and. the plant remained disused untR after the war, when Modern Machine Toots, Ltd.. resumed experiments.
International Since then, an associate company, Derustit, Ltd., Victoria Street, London, S.W.1, has been formed to operate the process, and plants have been installed in various parts of the country. CornpanieS have also been formed to develop the process in Scotland, Canada and South Africa, and licences have been granted foi operation in most countries in Europe under a French subsidiary, which, among oth2r activities, has installed 10 depots for the French State National Railways.