FAULTLESS LUBE IS AUTOMATIC
Page 60
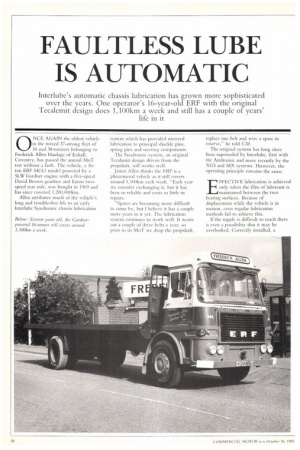
Page 61
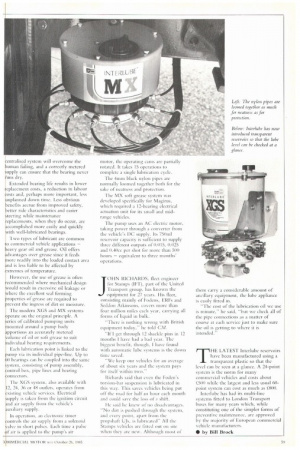
If you've noticed an error in this article please click here to report it so we can fix it.
Interlube's automatic chassis lubrication has grown more sophisticated over the years. One operator's 16-year-old ERF with the original Tecalemit design does 1,100km a week and still has a couple of years' life in it
0NCE AGAIN the oldest vehicle in the mixed 37-strong fleet of 16 and 38-tonners belonging to Frederick Allen Haulage of Exhall, Coventry, has passed the annual MoT test without a fault. The vehicle, a 16ton ERF 54GU model powered by a 5LW Gardner engine with a five-speed David Brown gearbox and Eaton twospeed rear axle, was bought in 1%9 and has since covered 1,200,000km.
Allen attributes much of the vehicle's long and trouble-free life to an early Interlube Syndromic chassis lubrication system which has provided metered lubrication to principal shackle pins, spring pins and steering components.
The Syndromic system, an original Tecalamit design driven from the propshaft, still works well.
James Allen thinks the ERF is a phenomenal vehicle as it still covers around 1,100km each week. "Each year we consider exchanging it. but it has been so reliable and costs so little in repairs.
"Spares are becoming more difficult to come by, but I believe it has a couple more years in it yet. The lubrication system continues to work well. It wears OM a couple of drive belts a year, so prior to its MoT we drop the propshaft, replace one belt and wire a spare in reserve," he told CM.
The original system has long since been superseded by Intertube. first with the Airdromic and more recently by the XGS and MX systems. However, the operating principle remains the same.
EFFECTIVE lubrication is achieved only when the film of lubricant is maintained between the two bearing surfaces. Because of displacement while the vehicle is in motion, even regular lubrication methods fail to achieve this.
If the nipple is difficult to reach there is even a possibility that it may be overlooked. Correctly installed, a
-entralised system will overcome the uman failing, and a correctly metered upply can ensure that the bearing never 'uns dry, Extended bearing life results in lower eplacement costs, a reduction in labour osts and, perhaps more important, less nplanned down tune. Less obvious cnefits accrue from improved safety, etter ride characteristics and easier teering while maintenance
eplacements-, when they do occur, are ccomplished more easily and quickly -th well-lubricated bearings.
1 wo types of lubricant are common o commercial vehicle applications — eavy gear oil and grease. Oil offers dvantages over grease since it feeds ore readily into the loaded contact area nd is less liable to be affected by .xtremes of temperature.
However, the use of grease is often ecommended where mechanical design mild result in excessive oil leakage or here the excellent seal forming roperties of grease are required to revent the ingress of dirt or moisture.
The modern XGS and MX systems perate on the original principle. A Cries of calibrated pumping units nounted around a pump body pportions an accurately metered olume of oil or soft grease to suit ndividual bearing requirements.
Each lubrication point is linked to the ump via its individual pipe-line. Up to 0 bearings can he coupled into the same ystem, consisting of pump assembly, ontrol box, pipe lines and bearing innectors.
The XGS system. also available with 2, 24, 36 or 48 outlets, operates from • xisting vehicle services. Electrical -upply is taken from the ignition circuit nd air supply from the vehicle's uxiliary supply.
In operation, an electronic timer • ontrols the air supply from a solenoid alve in short pulses. Each time a pulse f air is applied to the pump's air motor, the operating cams are partially rotated. It takes 15 operations to complete a single lubrication cycle.
The 4inin black nylon pipes are normally loomed together both for the sake of neatness and protection.
The MX soft grease system was developed specifically for Magirus. which required a 12-bearing electrical actuation unit for its small and midrange vehicles.
The pump uses an AC electric motor, taking power through a converter from the vehicle's DC supply. Its 750m1 reservoir capacity is sufficient to supply three different outputs of 0.015, 0.025 and 0.40cc per shot for inure than 500 hours — equivalent to three months' operations.
jOHN RICHARDS, fleet engineer for Stamps (1FT), part of the United Transport group, has known the equipment for 27 years. 1 is fleet, consisting mainly of Foclens, ERFs and Seddon Atkinsons, covers inure than four million miles each year, carrying all forms of liquid in bulk.
"There is nothing wrong with British equipment today,he told CM.
"If I get through 12 shackle pins in 11 months I have had a bad year. The biggest benefit, though. I have found ‘vith automatic lube systems is the down time saved.
"We keep our vehicles for an average of about six years and the system pays for itself within two...
Richards said that even the Fodelifs torsion-bar suspension is lubricated in this way. This saves vehicles being put off the road tbr half an hour each month and could save the loss of i shift.
I fe said he knew otno disadvantages. "No dirt is pushed through the system, and every point, apart I-rom the propshaft Ujs, is lubricated"' All the Stamps vehicles are fitted out on site when they are new. Although inost of" then) carry a considerable Amount of ancillary equipment, the laic appliance is easily fitted in.
"The cost of the lubrication oil we USe is minute,he said, "but we check all of the pipe connections as a matter of Course at each service jUst to make sure the oil is getting to where it is in THE LATEST hiterluhe reservoirs have been manufactured using a transparent plastic so that the level can be seen at a glance. A 24-point system is the norm for many commercial vehicles and costs about GOO while the latgest and less usual 60point system can cost as much as .1:800.
Intcrlube has had its multi-line systems fitted to London Transport buses for many years which, while constituting one of the simpler forms of preventive maintenance, are approved by the majority of European commercial vehicle manufacturers.
• by Bill Brock