DEMOUNTABLE DISTRIBUTION
Page 26

Page 27
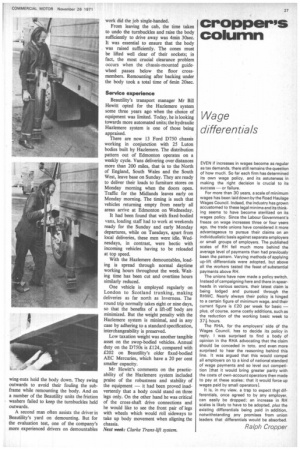
If you've noticed an error in this article please click here to report it so we can fix it.
by Alan Bunting, MIMechE
This week, the D-mount system, produced by the Hazlemere Motor Co. (Waltham Abbey) Ltd, of Highbridge Street, Waltham Abbey, Essex, as used by Beautility Ltd in its furniture distribution fleet.
Body swop test HAZLEMERE offers three lift-off body systems, of which the all-mechanical type A is the most popular and the simplest. For this reason the type A equipment was chosen for our evaluation test. It is important to bear in mind, however, that two hydraulically operated designs — one with the rams incorporated in the body corners enabling it to be lowered to ground level — are available from the company.
With the system tested, bodies are normally raised manually with a winding handle. This is achieved by using proprietary semitrailer landing legs suitably adapted with a spigot locating in sockets along the body base frame. Davies Magnet and Intertruck leg gear have been used — there is a mixture in use with Beautility. The Intertruck legs are favoured because of their lighter weight — an important factor when the leg has to be lifted into its socket. Unfortunately, the latest Intertruck legs being supplied by Hazlernere have wheels instead of feet. These provide less clearance between leftand right-hand legs with the result that rear tyres have been scuffed while backing under parked bodies.
Built into the floor above each pair of leg sockets is a full-width cross-shaft connecting the winding shafts of the two legs, as on a trailer landing gear. All winding is done from one side. This feature is more successful in theory than practice. During our test, considerable difficulty was experienced in engaging the drive shaft via the rather rudimentary pin-and-groove connection, especially on a pair of supposedly interchangeable new legs. The new legs were used following a weld fracture during the test, when one of the cross-shaft end connection collars broke away. Both Beautility and Hazlemere said it was a type of failure not previously experienced.
Nevertheless, it meant that the two rear legs had to be wound up and down individually, and our timed functional tests were eventually conducted on a different body. It was loaded with about 6 tons of Beautility's heavier furniture — a typical load in the 2300 cu ft Luton vans is 5 tons or less.
Beautility's application of the Hazlemere equipment is non-standard inasmuch that the support legs are wound using pneumatic power. Instead of the usual cranked winding handle, the company uses a Consolidated Pneumatic Power-Vane air gun, with a +in. Whitworth socket on its output shaft to fit the landing leg hexagons. This not only reduces the manual effort involved; it speeds the mounting and demounting sequences appreciably.
Normally, the legs are kept at Beautility's depot at Edmonton, North London. This has the disadvantage that bodies cannot be swopped away from base, in the event of a breakdown for example, without using a crane or other impractical means. There are two sockets at each corner of the body, enabling cheaper fixed-length slave legs to be used if the body is to be parked for any length of time. Because all lifting and lowering takes place in the legs, the Hazlemere vehicle chassis installation is extremely simple. It consists essentially of a sub-frame incorporating bolsters in line with the leg positions. Conical spigots 2in.-wide protrude down from the body floor to locate in circular sockets in the bolsters.
Hazlemere's method of ensuring accurate body-chassis alignment proved most effective. A 9in.-diameter guide wheel standing proud at the rear end of the chassis subframe is restrained in a 10in.-wide inverted channel under the body floor. On the front bulkhead a pair of "throated" guide plates ensure even more precise alignment. As the body is lowered the four cones engage to hold the body securely in both horizontal planes. In addition, two stout vertical "buffers" at the front end of the sub-frame withstand braking forces.
Four turnbuckles with large removal wing-nuts hold the body down. They swing outwards to avoid their fouling the subframe while remounting the body. And on a number of the Beautility units the friction washers failed to keep the turnbuckles held outwards.
A second man often assists the driver in Beautility's yard on demounting. But for the evaluation test, one of the company's more experienced drivers on demountables work did the job single-handed.
From leaving the cab, the time taken to undo the turnbuckles and raise the body sufficiently to drive away was 4min 30sec. It was essential to ensure that the body was raised sufficiently. The cones must be lifted well clear of their sockets; in fact, the most crucial clearance problem occurs when the chassis-mounted guidewheel passes below the floor cross members. Remounting after backing under the body took a total time of 6min 20sec.
Service experience Beautility's transport manager Mr Bill Hewitt opted for the Hazlemere system some three years ago when the choice of equipment was limited. Today, he is looking towards more automated units; the hydraulic Hazlemere system is one of those being appraised.
There are now 13 Ford D750 chassis working in conjunction with 25 Luton bodies built by Hazlemere. The distribution pattern out of Edmonton operates on a weekly cycle. Vans delivering over distances more than 200 miles, that is to the North of England, South Wales and the South West, leave base on Sunday. They are ready to deliver their loads to furniture stores on Monday morning when the doors open. Traffic for the Midlands leaves early on Monday morning. The timing is such that vehicles returning empty from nearly all areas arrive at Edmonton on Wednesday.
It had been found that with fixed-bodied vans, loading staff had to work at weekends ready for the Sunday and early Monday departures, while on Tuesdays, apart from local deliveries, these men were idle. Wednesdays, in contrast, were hectic with incoming vehicles having to be reloaded at top speed.
With the Hazlemere demountables, loading is spread through normal daytime working hours throughout the week. Waiting time has been cut and overtime hours similarly reduced.
One vehicle is employed regularly on London to Scotland trunking, making deliveries as far north as Inverness. The round trip normally takes eight or nine days, so that the benefits of a lift-off body are minimized. But the weight penalty with the Hazlemere system is minimal, and in any case by adhering to a standard specification, interchangeability is preserved.
Low taxation weight was another tangible asset on the swop-bodied vehicles. Annual duty on the D750s is £124, compared with £202 on Beautility's older fixed-bodied AEC Mercuries, which have a 20 per cent smaller capacity.
Mr Hewitt's comments on the practicability of the Hazlemere system included praise of the robustness and stability of the equipment — it had been proved inadvertently that a body could stand on three legs only. On the other hand he was critical of the cross-shaft drive connections and he would like to see the front pair of legs with wheels which would foil sideways to take up body movement when aligning the chassis.
Next week: Clarke Trans-lift system.