GET THE LOW DOWN
Page 50
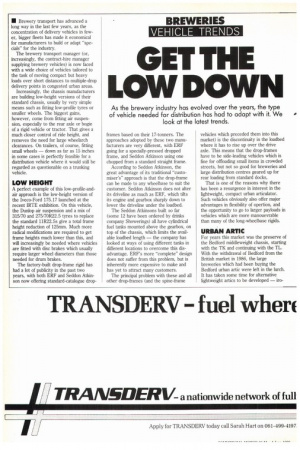
Page 51
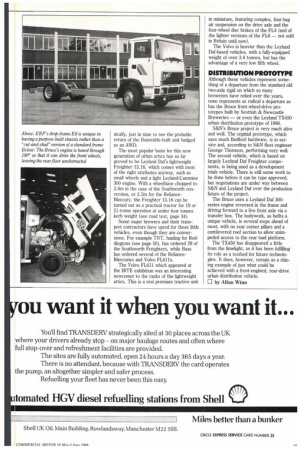
If you've noticed an error in this article please click here to report it so we can fix it.
As the brewery industry has evolved over the years, the type of vehicle needed for distribution has had to adapt with it. We look at the latest trends.
• Brewery transport has advanced a long way in the last few years, as the concentration of delivery vehicles in fewer, bigger fleets has made it economical for manufacturers to build or adapt "specials" for the industry.
The brewery transport manager (or, increasingly, the contract-hire manager supplying brewery vehicles) is now faced with a wide choice of vehicles tailored to the task of moving compact but heavy loads over short distances to multiple-drop delivery points in congested urban areas.
Increasingly, the chassis manufacturers are building low-height versions of their standard chassis, usually by very simple means such as fitting low-profile tyres or smaller wheels. The biggest gains, however, come from fitting air suspension, especially to the rear axle or bogie of a rigid vehicle or tractor. That gives a much closer control of ride height, and removes the need for large wheelarch clearances. On trailers, of course, fitting small wheels — down as far as 15 inches in some cases is perfectly feasible for a distribution vehicle where it would still be regarded as questionable on a trunking vehicle.
LOW HEIGHT
A perfect example of this low-profile-andair approach is the low-height version of the Iveco-Ford 175.17 launched at the recent IRTE exhibition. On this vehicle, the Dunlop air suspension and a mix of 315/70 and 275/70R22.5 tyres to replace the standard 11R22.6s give a total frame height reduction of 125mm. Much more radical modifications are required to get frame heights much lower than this, and will increasingly be needed where vehicles are fitted with disc brakes which usually require larger wheel diameters than those needed for drum brakes.
The factory-built drop-frame rigid has had a lot of publicity in the past two years, with both ERF and Seddon Atkinson now offering standard-catalogue drop frames based on their 17-tonners. The approaches adopted by these two manufacturers are very different, with ERF going for a specially-pressed dropped frame, and Seddon Atkinson using one chopped from a standard straight frame.
According to Seddon Atkinson, the great advantage of its traditional "customiser's" approach is that the drop-frame can be made to any wheelbase to suit the customer. Seddon Atkinson does not alter its driveline as much as ERF, which tilts its engine and gearbox sharply down to lower the driveline under the loadbed.
The Seddon Atkinsons built so far (some 12 have been ordered by drinks company Showerings) all.have cylindrical fuel tanks mounted above the gearbox, on top of the chassis, which limits the available loadbed length — the company has looked at ways of using different tanks in different locations to overcome this disadvantage. ERF's more "complete" design does not suffer from this problem, but is inherently more expensive to make and has yet to attract many customers.
The principal problem with these and all other drop-frames (and the spine-frame vehicles which preceded them into this market) is the discontinuity in the loadbed where it has to rise up over the drive axle. This means that the drop-frames have to be side-leading vehicles which is fine for offloading small items in crowded streets, but not so good for breweries and large distribution centres geared up for rear loading from standard docks, That is one of the reasons why there has been a resurgence in interest in the lightweight, compact urban articulator. Such vehicles obviously also offer major advantages in flexibility of opertion, and the opportunity to go to larger payloads in vehicles which are more tnanouevrable than many of the long-wheelbase rigids.
URBAN ARTIC
For years this market was the preserve of the Bedford middleweight chassis, starting with the TK and continuing with the TL. With the withdrawal of Bedford from the British market in 1986, the large breweries which had been buying the Bedford urban artic were left in the lurch. It has taken some time for alternative lightweight artics to be developed — iro nically, just in time to see the probable return of the Dunstable-built unit badged as an AWD.
The most popular basis for this new generation of urban artics has so far proved to be Leyland Daf's lightweight Freighter 13.16, which comes with most of the right attributes anyway, such as small wheels and a light Leyland/Cummins 300 engine. With a wheelbase chopped to 2.8m in the case of the Southworth conversion, or 2.5m for the RelianceMercury, the Freighter 13.16 can be turned out as a practical tractor for 19 or 21-tonne operation at under four tonnes kerb weight (see road test, page 34).
Some major brewers and their transport contractors have opted for these little vehicles, even though they are conversions. For example TNT, hauling for Boddingtons (see page 50), has ordered 29 of the Southworth Freighters, while Bass has ordered several of the RelianceMercuries and Volvo FL611s.
The Volvo FL611 which appeared at the IRTE exhibition was an interesting newcomer to the ranks of the lightweight artics. This is a real premium tractive unit in miniature, featuring complex, four-bag air suspension on the drive axle and the four-wheel disc brakes of the FL4 (and of the lighter versions of the FL6 — not sold in Britain until now).
The Volvo is heavier than the Leyland Daf-based vehicles, with a fully-equipped weight of over 3.8 tonnes, but has the advantage of a very low fifth wheel.
DISTRIBUTION PROTOTYPE
Although these vehicles represent something of a departure from the standard old two-axle rigid on which so many breweries have relied over the years, none represents as radical a departure as has the Bruce front-wheel-drive prototypes built by Scottish & Newcastle Breweries — or even the Leyland TX450 urban distribution prototype of 1986.
S&N's Bruce project is very much alive and well. The orginial prototype, which uses much Bedford hardware, is in service and, according to S&N fleet engineer George Thomson, performing very well. The second vehicle, which is based on largely Leyland Daf Freighter components, is being used as a development trials vehicle. There is still some work to be done before it can be type approved, but negotiations are under way between S&N and Leyland Daf over the production future of the project.
The Bruce uses a Leyland Daf 300series engine reversed in the frame and driving forward to a live front axle via a transfer box. The bodywork, as befits a unique vehicle, is several steps ahead of most, with no rear corner pillars and a cantilevered roof section to allow unimpeded access to the rear load platform.
The TX450 has disappeared a little from the limelight, as it has been fulfilling its role as a testbed for future technologies. It does, however, remain as a shining example of just what could be achieved with a front-engined, rear-drive urban distribution vehicle.
El by Allan Winn