Get the best benefits overall from expense on protective clothing
Page 111
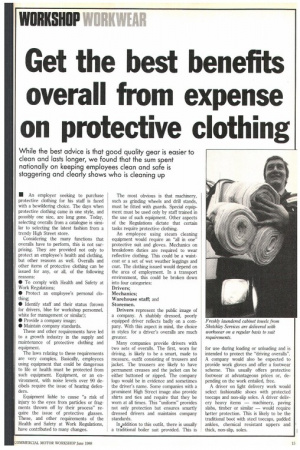
Page 112
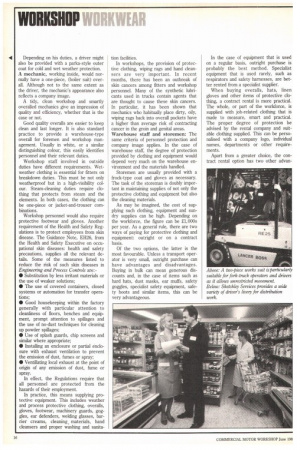
Page 113
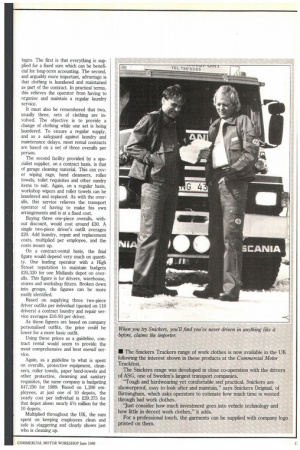
If you've noticed an error in this article please click here to report it so we can fix it.
While the best advice is that good quality gear is easier to clean and lasts longer, we found that the sum spent nationally on keeping employees clean and safe is staggering and clearly shows who is cleaning up
MI An employer seeking to purchase protective clothing for his staff is faced with a bewildering choice. The days when protective clothing came in one style, and possibly one size, are long gone. Today, selecting overalls from a catalogue is similar to selecting the latest fashion from a trendy High Street store.
Considering the many functions that overalls have to perform, this is not surprising. They are provided not only to protect an employee's health and clothing, but other reasons as well. Overalls and other items of protective clothing can be issued for any, or all, of the following reasons: • To comply with Health and Safety at Work Regulations; • Protect an employee's personal clothing; • Identify staff and their status (brown for drivers, blue for workshop personnel, white for management or similar); • Provide a company image; • Maintain company standards.
These and other requirements have led to a growth industry in the supply and maintenance of protective clothing and equipment.
The laws relating to these requirements are very complex. Basically, employees using equipment that could be dangerous to life or health must be protected from such equipment. Equipment, or an environment, with noise levels over 90 decibels require the issue of hearing defenders.
Equipment liable to cause "a risk of injury to the eyes from particles or fragments thrown off by their process" require the issue of protective glasses. These, and other requirements of the Health and Safety at Work Regulations, have contributed to many changes.
The most obvious is that machinery, such as grinding wheels and drill stands, must be fitted with guards. Special equipment must be used only by staff trained in the use of such equipment. Other aspects of the Regulations dictate that certain tasks require protective clothing.
An employee using steam cleaning equipment would require an "all in one" protective suit and gloves. Mechanics on breakdown duties are required to wear reflective clothing. This could be a waistcoat or a set of wet weather leggings and coat. The clothing issued would depend on the area of employment. In a transport environment, this could be broken down into four categories:
Drivers; Mechanics; Warehouse staff; and Storemen.
Drivers represent the public image of a company. A shabbily dressed, poorly equipped driver reflects badly on a company. With this aspect in mind, the choice in styles for a driver's overalls are much greater.
Many companies provide drivers with two sets of overalls. The first, worn for driving, is likely to be a smart, made to measure, outfit consisting of trousers and jacket. The trousers are likely to have permanent creases and the jacket can be either buttoned or zipped. The company logo would be in evidence and sometimes the driver's name. Some companies with a .prominent High Street image also provide shirts and ties and require that they be worn at all times. This "uniform" provides not only protection but ensures smartly dressed drivers and maintains company standards.
In.addition to this outfit, there is usually a traditional boiler suit provided. This is
for use during loading or unloading and is intended to protect the "driving overalls". A company would also be expected to provide work gloves and offer a footwear scheme. This usually offers protective footwear at advantageous prices or, depending on the work entailed, free.
A driver on light delivery work would select fashionable shoes with protected toecaps and non-slip soles. A driver delivery heavy items — machinery, paving slabs, timber or similar — would require better protection. This is likely to be the traditional boot with steel toecaps, padded ankles, chemical resistant uppers and thick, non-slip, soles. Depending on his duties, a driver might also be provided with a parka-style outer coat for cold and wet weather protection. A mechanic, working inside, would normally have a one-piece, (boiler suit) overall. Although not to the same extent as the driver, the mechanic's appearance also reflects a company image.
A tidy, clean workshop and smartly overalled mechanics give an impression of quality and efficiency, whether that is the case or not.
Good quality overalls are easier to keep clean and last longer. It is also standard practice to provide a warehouse-type overall for foremen and workshop management. Usually in white, or a similar distinguishing colour, this easily identifies personnel and their relevant duties.
Workshop staff involved in outside duties have different requirements. Wetweather clothing is essential for fitters on breakdown duties. This must be not only weatherproof but in a high-visibility colour. Steam-cleaning duties require clothing that protects from steam and the elements. In both cases, the clothing can be one-piece or jacket-and-trouser combinations.
Workshop personnel would also require protective footwear and gloves. Another requirement of the Health and Safety Regulations is to protect employees from skin disease. The Guidance Note, EH26, from the Health and Safety Executive on occupational skin diseases: health and safety precautions, supplies all the relevant details. Some of the measures listed to reduce the risk of such skin diseases in Engineering and Process Controls are: • Substitution by less irritant materials or the use of weaker solutions; • The use of covered containers, closed systems or automation for transfer operations; • Good housekeeping within the factory generally with particular attention to cleanliness of floors, benches and equipment, prompt attention to spillages and the use of no-dust techniques for cleaning up powder spillages; • Use of splash guards, chip screens and similar where appropriate; • Installing an enclosure or partial enclosure with exhaust ventilation to prevent the emission of dust, fumes or spray; • Ventillating local exhaust at the point of origin of any emission of dust, fume or spray.
In effect, the Regulations require that all personnel are protected from the hazards of their employment.
In practice, this means supplying protective equipment. This includes weather and process protective clothing, overalls, gloves, footwear, machinery guards, goggles, ear defenders, welding glasses, barrier creams, cleaning_ materials, hand cleansers and proper washing and sanita tion facilities.
In workshops, the provision of protective clothing, wiping rags and hand cleansers are very important. In recent months, there has been an outbreak of skin cancers among fitters and workshop personnel. Many of the synthetic lubricants used in trucks contain agents that are thought to cause these skin cancers. In particular, it has been shown that mechanics who habitually place dirty, oily, wiping rags back into overall pockets have a higher than average risk of contracting cancer in the groin and genital areas.
Warehouse staff and storemen: The same criteria of personnel protection and company image applies. In the case of warehouse staff, the degree of protection provided by clothing and equipment would depend very much on the warehouse environment and the materials handled.
Storemen are usually provided with a frock-type coat and gloves as necessary. The task of the storeman is doubly important in maintaining supplies of not only the protective clothing and equipment but also the cleaning materials.
As may be imagined, the cost of supplying such clothing, equipment and sundry supplies can be high. Depending on the workforce, the figure can be 21,000s per year. As a general rule, there are two ways of paying for protective clothing and equipment: outright or on a contract basis.
Of the two options, the latter is the most favourable. Unless a transport operator is very small, outright purchase can have advantages and disadvantages. Buying in bulk can mean generous discounts and, in the case of items such as hard hats, dust masks, ear muffs, safety goggles, specialist safety equipment, safety boots and similar items, this can be very advantageous. In the case of equipment that is used on a regular basis, outright purchase is probably the best method. Specialist equipment that is used rarely, such as respirators and safety harnesses, are better rented from a specialist supplier.
When buying overalls, hats, linen gloves and other items of protective clothing, a contract rental is more practical. The whole, or part of the workforce, is supplied with job-related clothing that is made to measure, smart and practical. The proper degree of protection be advised by the rental company and suitable clothing supplied. This can be personalised with a company logo, individual names, departments or other requirements.
Apart from a greater choice, the contract rental option has two other advan tages. The first is that everything is supplied for a fixed sum which can be benefi cial for long-term accounting. The second, and arguably more important, advantage is that clothing is laundered and maintained as part of the contract. In practical terms, this relieves the operator from having to organise and maintain a regular laundry service.
It must also be remembered that two, usually three, sets of clothing are involved. The objective is to provide a change of clothing while one set is being laundered. To ensure a regular supply, and as a safeguard against laundry and maintenance delays, most rental contracts are based on a set of three overalls per person.
The second facility provided by a specialist supplier, on a contract basis, is that of garage cleaning material. This can cov er wiping rags, hand cleansers, roller towels, toilet requisites and other sundry items to suit. Again, on a regular basis, workshop wipers and roller towels can be laundered and replaced. As with the over alls, this service relieves the transport operator of having to make his own arrangements and is at a fixed cost Buying three one-piece overalls, without discount, would cost around 230. A single two-piece driver's outfit averages 220. Add laundry, repair and replacement costs, multiplied per employee, and the costs mount up.
On a contract-rental basis, the final figure would depend very much on quanti ty. One leading operator with a High Street reputation to maintain budgets 220,320 for one Midlands depot on over alls. This figure is for drivers, warehouse, stores and workshop fitters. Broken down into groups, the figures can be more easily identified.
Based on supplying three two-piece driver outfits per individual (quoted on 110 drivers) a contract laundry and repair service averages 216.93 per driver.
As these figures are based on company personalised outfits, the price could be lower for a more basic outfit
Using these prices as a guideline, contract rental would seem to provide the most comprehensive and best overall service.
Again, as a guideline to what is spent on overalls, protective equipment, clean sers, roller towels, paper hand-towels and other protective, cleansing and sanitary requisites, the same company is budgeting 247,250 for 1989. Based on 1,200 employees, at just one of 10 depots, the yearly cost per individual is 239.375 for that depot alone; nearly £1/2 million for the 10 depots.
Multiplied throughout the UK, the sum spent on keeping employees clean and safe is staggering and dearly shows just who is cleaning up.