Braking problems reviewed by six experts
Page 45
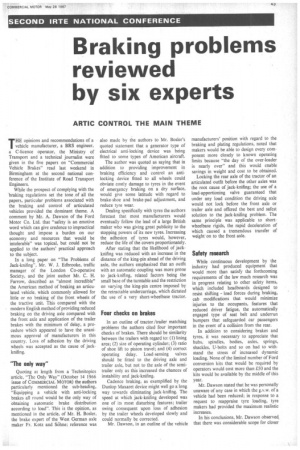
Page 46
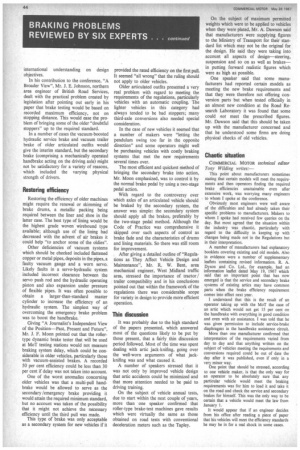
If you've noticed an error in this article please click here to report it so we can fix it.
ARTIC CONTROL THE MAIN THEME
THE opinions and recommendations of a
vehicle manufacturer, a BRS engineer, a C-licence operator, the Ministry of Transport and a technical journalist were given in the five papers on "Commercial Vehicle Brakes" read last weekend in Birmingham at the second national conference of the Institute of Road Transport Engineers.
While the prospect of complying with the braking regulations set the tone , of all the papers, particular problems associated with the braking and control of articulated vehicles provided the dominant theme. A comment by Mr. A. Dawson of the Ford Motor Co. Ltd. that "safety is an emotive word which can give credence to impractical thought and impose a burden on our economy and resources that would be intolerable" was topical, but could not be applied to the authors' practical approach to the subject.
In a long paper on "The Problems of Jack-knifing", Mr. W. J. Edbrooke, traffic manager of the London Co-operative Society, and the joint author Mr. C. H. Farrow, described as "almost incredible" the American method of braking an articulated vehicle, which commonly allowed for little or no braking of the front wheels of the tractive unit. This compared with the modern English method of providing reduced braking on the driving axle compared with the front axle and application of the trailer brakes with the minimum of delay, a procedure which appeared to have the unanimous approval of manufacturers in this country. Loss of adhesion by the driving wheels was accepted as the cause of jackknifing.
"The only way"
Quoting at length from a Technitopics article, "The Only Way" (October 14 1966 issue of COMMERCIAL MOTOR) the authors particularly mentioned the sub-heading, "Equipping a vehicle with anti-locking brakes all round would be the only way of obtaining automatic brake distribution according to load". This is the opinion, as mentioned in the article, of Mr. H. Bosler, the brake expert of the West German axle maker Fr. Kotz and Saline; reference was also made by the authors to Mr. Bosler's quoted statement that a generator type of electrical anti-locking device was being fitted to some types of American aircraft.
The author was quoted as saying that in addition to providing improvement in braking efficiency and control an antilocking device fitted to all wheels could obviate costly damage to tyres in the event of emergency braking on a dry surface, would give some latitude with regard to brake-shoe and brake-pad adjustment, and reduce tyre wear.
Dealing specifically with tyres the authors forecast that most manufacturers would eventually follow the lead of a large British maker who was giving great publicity to the stopping powers of its new tyres. Increasing the adhesion of tyres would, however, reduce the life of the covers proportionately.
After stating that the likelihood of jackknifing was reduced with an increase in the distance of the king-pin ahead of the driving axle, the authors emphasized that an outfit with an automatic coupling was more prone to jack-knifing, related factors being the small base of the turntable and the restriction on varying the king-pin centre imposed by the retractable undercarriage, which dictated the use of a very short-wheelbase tractor.
Four checks on brakes
In an outline of tractor /trailer matching problems the authors cited four important checks of brakes. There should be similarity between the trailers with regard to: (1) lining area; (2) size of operating cylinder; (3) ratio of shoe lift to piston travel; and (4) correct operating delay. Load-sensing valves should be fitted to the driving axle and trailer axle, but not to the axle of the semitrailer only as this increased the chances of instability and jack-knifing.
Cadence braking, as exemplified by the Dunlop Maxaret device might well go a long way towards eliminating jack-knifing. The speed at which jack-knifing developed was one of its most disturbing features; trailer swing consequent upon loss of adhesion by the trailer wheels developed slowly and could normally be corrected.
Mr. Dawson, in an outline of the vehicle manufacturers' position with regard to the braking and plating regulations, noted that makers would be able to design every component more closely to known operating limits because "the day of the over-loader is nearly over" and this would enable savings in weight and cost to be obtained.
Locking the *rear axle of the tractor of an articulated outfit before the other axles was the root cause of jack-knifing; the use of a load-apportioning valve guaranteed that under any load condition the driving axle would not lock before the front axle or trailer axle and offered the best and safest solution to the jack-knifing problem. The same principle was applicable to shortwheelbase rigids, the rapid deceleration of which caused a tremendous transfer of weight on to the front axle.
Safety research
While continuous development by the industry had produced equipment that would more than satisfy the forthcoming requirements of the law much research was in progress relating to other safety items, which included headboards designed to resist shifting load forces during braking, cab modifications that would minimize injuries to the occupants, features that reduced driver fatigue, the automatically engaged type of seat belt and underrun bumpers that safeguarded car passengers in the event of a collision from the rear.
In addition to considering brakes and tyres, it was necessary to appreciate that hubs, spindles, bodies, axles, springs, shackles, U-bolts and so on had to withstand the stress of increased dynamic loading. None of the limited number of Ford conversion kits that would be required by operators would cost more than £50 and the kits would be available by the middle of this year.
Mr. Dawson stated that he was personally unaware of any case in which the g.v.w. of a vehicle had been reduced; in response to a request to reappraise tyre loading, tyre makers had provided the maximum realistic increases.
In his conclusions, Mr. Dawson observed. that there was considerable scope for closer international understanding on design objectives.
In his contribution to the conference, "A Broader View", Mr. J. E. Johnson, northern area engineer of British Road Services, dealt with the practical problem created by legislation after pointing out early in his paper that brake testing would be based on recorded maximum efficiency, not on stopping distance. This would ease the problem of bringing some of the older "doubtful stoppers" up to the required standard.
In a number of cases the vacuum-boosted hydraulic service brake and vacuum trailer brake of older articulated outfits would give the interim standard, but the secondary brake (comprising a mechanically operated handbrake acting on the driving axle) might not be satisfactory for a variety of reasons, which included the varying physical strength of drivers.
Restoring efficiency
Restoring the efficiency of older machines might require the renewal or skimming of brake drums, a metallic packing being required between the liner and shoe in the latter case. The best type of lining would be the highest grade woven• wirebound type available; although use of the lining had decreased with the advent of air brakes it could help "to anchor some of the oldies".
Other deficiencies of vacuum systems which should be checked included flattened copper or metal pipes, deposits in the pipes, a faulty vacuum gauge and a worn servo. Likely faults in a servo-hydraulic system included incorrect clearance between the servo push rod and the hydraulic operating piston and also expansion under pressure of flexible pipes. It was often possible to obtain a larger-than-standard master cylinder to increase the efficiency of an hydraulic system. The simplest way of overcoming the emergency brake problem was to boost the handbrake. '
Giving "A Journalist's Independent View of the Position—Past, Present and Future", Mr. J. F. Moon pointed out that the rollertype dynamic brake tester that will be used at MoT testing stations would not measure braking system delay, which could be considerable in older vehicles, particularly those with vacuum-assisted brakes. A recorded 50 per cent efficiency could be less than 30 per cent if delay was not taken into account.
One of the worst anomalies concerning older vehicles was that a multi-pull handbrake would be allowed to serve as the secondary /emergency brake providing it would attain the required minimum standard, but no account was taken of the possibility that it might not achieve the necessary efficiency until the third pull was made. This type of brake was only acceptable as a secondary system for new vehicles if it provided the rated efficiency on the first pull. It seemed "all wrong" that the ruling should not apply to older vehicles.
Older articulated outfits presented a very real problem with regard to meeting the requirements of the regulations, particularly vehicles with an automatic coupling. The lighter vehicles in this category had always tended to be bad stoppers; many third-axle conversions also needed special consideration.
In the case of new vehicles it seemed that a number of makers were "letting the pendulum swing too far in the opposite direction" and some operators might well be purchasing vehicles with costly braking systems that met the new requirements several times over.
The most efficient and quickest method of bringing the secondary brake into action, Mr. Moon emphasized, was to control it by the normal brake pedal by using a two-stage pedal action.
With regard to the controversy over which axles of an articulated vehicle should be braked by the secondary system, the answer was simple: the secondary system should apply all the brakes, preferably by the two-stage pedal method. Although the Code of Practice was comprehensive it skipped over such aspects of control as brake fade and the characteristics of drums and lining materials. So there was still room for improvement.
After giving a detailed outline of "Regulations as They Affect Vehicle Design and Maintenance", Mr. R. W. Bent, area mechanical engineer, West Midland traffic area, stressed the importance of tractor / trailer compatibility and in his conclusions pointed out that within the framework of the regulations there was considerable scope for variety in design to provide more efficient operation.
Thin discussion
It was probably due to the high standard of the papers presented, which answered most of the questions likely to be put by those present, that a fairly thin discussion period followed. Most of the time was spent dealing with artic jack-knifing, going over the well-worn arguments of what jackknifing was and what caused it.
A number of speakers stressed that it was not only by improved vehicle design that attic accidents could be minimized and that more attention needed to be paid to driving training.
On the subject of vehicle annual tests, due to start within the next couple of years, more than one speaker confirmed that roller-type brake-test machines gave results which were virtually the same as those obtained on road tests with conventional deceleration meters such as the Tapley. On the subject of maximum permitted weights which were to be applied to vehicles when they were plated, Mr. A. Dawson said that manufacturers were supplying figures to the Ministry of Transport for their standard list which may not be the original for the design. He said they were taking into account all aspects of design—steering, suspension and so on as well as brakes— in putting forward realistic figures which were as high as possible.
One speaker said that some manufacturers had reported certain models as meeting the new brake requirements and that they were therefore not offering conversion parts but when tested officially in an almost new condition at the Road Research Laboratory it was found that some could not meet the prescribed figures. Mr. Dawson said that this should be taken up with the manufacturer concerned and that he understood some firms are doing physical checks of old vehicles.
Chaotic situation
COMMERCIAL MOTOR technical editor Tony Wilding writes:— This point about manufacturers sometimes stating that certain models will meet the requirements and then operators finding the required brake efficiencies unattainable even after extensive work, was worrying many engineers to whom I spoke at the conference. Obviously most engineers were well aware of the difficulties and had already taken their specific problems to manufacturers. Makers to whom I spoke had received few queries on the day. But most agreed that the situation within the industry was chaotic, particularly with regard to the difficulty in keeping up with changes being made not in the Regulations but in their interpretation. A number of manufacturers had explanatory booklets covering existing and old models. Also in evidence were a number of supplementary leaflets containing revised information. R. A. Dyson and Co. Ltd., for example, had an information leaflet dated May 19, 1967 which said that an important point that has now emerged is that the service and secondary brake systems of existing artics may have common parts when the brake efficiency requirement comes into effect next year. I understand that this is the result of an operator taking up with the MoT the case of an attic which would not get 15 per cent on the handbrake with everything in good condition and even with air assistance. I was told that he was given permission to include service-brake diaphragms in the handbrake assistance circuit. More than one manufacturer confirmed that interpretation of the requirements varied from day to day and that anything written on the subject of vehicles meeting the requirements and conversions required could be out of date the day after it was published, even if only in a very minor way. One point that should be stressed, according to one vehicle maker, is that the only way for an operator to be absolutely sure that any particular vehicle would meet the braking requirements was for him to load it and take it on the road and check the service and secondary brakes for himself. This was the only way to be certain that a vehicle would meet the law from January 1. It would appear that if an engineer decides from his office after reading a piece of paper that his vehicles will meet the efficiency standards he may be in for a real shock in some cases.