It's containers by road for France, forecast the experts
Page 39
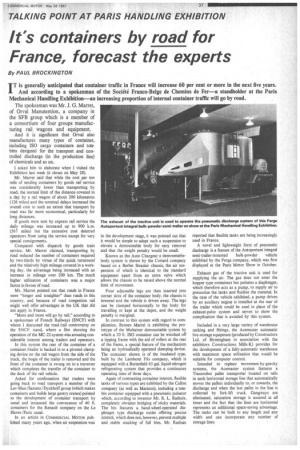
If you've noticed an error in this article please click here to report it so we can fix it.
By PAUL BROCKINGTON
IT is generally anticipated that container traffic in France will increase 60 per cent or more in the next five years. And according to a spokesman of the Societe Franco-Belge de Chemins de Fer—a standholder at the Paris Mechanical Handling Exhibition—an increasing proportion of internal container traffic will go by road.
The spokesman was Mr. J. G. Marret, of Orval Manutention, a company in the SFB group which is a member of a consortium of four groups manufacturing rail wagons and , equipment.
And it is significant that Orval also manufactures many types of container, including ISO cargo containers and tote bins designed for the transport and controlled discharge (in the production line) of chemicals and so on.
I asked him to elaborate when I visited the Exhibition last week (it closes on May 28).
Mr. Marret said that while the cost per ton mile of sending containers by goods rail service was considerably lower than transporting by road, the normal limit of the distance covered in a day by a rail wagon of about 200 kilometres (126 miles) and the terminal delays increased the overall cost to such an extent that transport by road was far more economical, particularly for long distances.
If goods were sent by express rail service the daily mileage was increased up to 900 k.m. (567 miles) but the excessive cost deterred operators from using the service except for very special consignments.
Compared with dispatch by goods train service, Mr. Marret claimed, transporting by road reduced the number of containers required by two-thirds by virtue of the quick tumround and the relatively high mileage covered in a working day, the advantage being increased with an increase in mileage over 200 km. The much higher utilization of containers was a major factor in favour of road.
Mr. Marret pointed out that roads in France were "longer and straighter" than roads in this country, and because of road congestion rail might well offer advantages in the UK that did not apply in France.
"More and more will go by rail," according to a spokesman of French Railways (SNCF) with whom I discussed the road/rail controversy on the SNCF stand, where a film showing the operation of the MC-22 system Was arousing considerable interest among traders and operators.
In this system the rear of the container of a container /trailer is backed in to a pivoted clamping device on the rail wagon from the side of the truck, the bogie of the trailer is removed and the front of the container is swung on to a traverser which completes the transfer of the container to the deck of the rail vehicle.
Asked for confirmation that traders were going back to road transport a member of the Lev-Man /Sameto /Dyckhoff group (which makes containers and builds large gantry cranes) pointed to the development of container transport by canal and instanced the conveyance of 40 ft. containers for the Renault company on the Le Havre /Paris canal.
In an article in COMMERCIAL MOTOR published many years ago, when air suspension was
in the development stage, it was pointed out that it would be simple to adapt such a suspension to elevate a demountable body for easy removal and that the weight penalty would be small.
Known as the Auto Chargeur a demountablebody system is shown by the Cottard company based on a Berliet Stradair chassis, the air suspension of which is identical to the standard equipment apart from an extra valve which allows the chassis to be raised above the normal limit of movement.
Four adjustable legs are then inserted into corner slots of the container body, the chassis is lowered and the vehicle is driven away. The legs can be clamped horizontally to the body for travelling or kept at the depot, and the weight penalty is marginal.
In contrast to this system with regard to complication, Bennes Marrel is exhibiting the prototype of the Multainer demountable system by which a 20 ft. ISQ container can be winched off a tipping frame with the aid of rollers at the rear of the frame, a special feature of the mechanism being an hydraulically operated clamping device. The container shown is of the insulated type, built by the Lamberet Fits company, which is equipped with a Butterfield 65 gal. liquid-nitrogen refrigerating system that provides a continuous operating time of three days.
Again of contrasting container interest, flexible tanks of various types are exhibited by the Callon company (as well as Marston), including a totebin container equipped with a pneumatic pulsator which, according to inventor Mr. R. L. Rathuis, completely obviates bridging of sticky materials. The bin features a hand-wheel-operated diaphragm type discharge outlet offering precise control, which does not, however, prevent multiple and stable stacking of full bins. Mr. Rathuis reported that flexible tanks are being increasingly used in France.
A novel and lightweight form of pneumatic discharge is a feature of the Autoportant integral semi-trailer-mounted bulk-powder vehicle exhibited by the Ferga company, which was first displayed at the Paris Motor Show in October.
Exhaust gas of the tractive unit is used for supplying the air. The gas does not enter the hopper type containers but pulsates a diaphragm, which therefore acts as a pump, to supply air to pressurize the tanks and fluidize the material. In the case of the vehicle exhibited, a pump driven by an auxiliary engine is installed at the rear of the trailer which could be used in place of the exhaust-pulse system and serves to show the complication that is avoided by this system.
Included in a very large variety of warehouse racking and fittings, the Acemaster automatic live-storage equipment (produced by Constructors Ltd. of Birmingham in association with the exhibitors Constructions Mills-K) provides for the development of a fully-automatic warehouse with maximum space utilization that would be suitable for computer control.
Intended to replace movement-by-gravity systems, the Acemaster system features a Transrobot pallet transporter located on rails in each horizontal storage line that automatically moves the pallets individually to, or towards, the discharge end when the last pallet in the line is collected by fork-lift truck. Gangways are eliminated, saturation storage is assured at all times and the fact that the lines are horizontal represents an additional space-saving advantage. The racks can be built to any length and any width and can incorporate any number of storage lines.