Efficiency drive
Page 32

Page 33
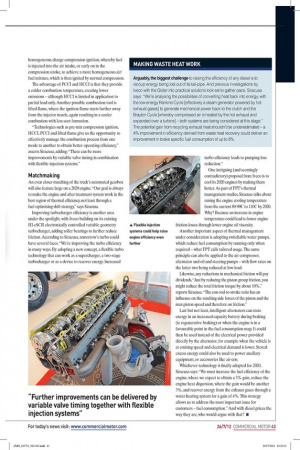
If you've noticed an error in this article please click here to report it so we can fix it.
Iveco plans to raise the brake thermal efficiency of its heavy truck diesel engines by 10% come 2020. So how exactly is it going to do it? CM reveals the Italian’s future diesel plans...
Words: Brian Weatherley
At CM, we’ve seen many concept trucks throughout the years, but something about the Iveco Glider (pictured below), unveiled at the 2010 IAA Show, struck us as different – in particular that its primary engineering focus was all about raising diesel engine eficiency. Post-IAA, however, the Glider dropped off our radar and we wondered if that was it for the concept truck.
But at the recent unveiling of Iveco’s HI-eSCR Euro-6 engine range (CM 17 May), Massimo Siracusa, Fiat Powertrain Industrial’s vice-president for product engineering, revealed a bold strategy to improve the brake thermal eficiency (BTE) of Iveco’s heavy truck diesel engines to an unheard of 55% by 2020. And some of the kit seen on the Glider may feature in Fiat Powertrain’s (FPT) maximum eficiency drive.
Put simply, BTE is the ratio between the energy available at the engine’s lywheel and the energy available in the fuel in the tank. It’s also worth remembering where diesel engine thermal eficiency sits – and what’s holding it back. Today the best heavy truck engines barely achieve more than 45% – with more than half of all the energy created through burning fuel being lost as waste heat through the exhaust pipe, cooling system or radiated from the block; or through mechanical “parasitic” losses to the air compressor, water and steering pumps and alternator; or due to frictional losses in the engine itself.
So Iveco’s plan to regain 10% of those losses before this decade is out is impressive. “Our development programme for the next years will bring our engines to a thermal eficiency of more than 50% by 2020,” promises Siracusa, who also insists: “The 10% gap will be illed – it’s a challenging objective in such a short period of time. To achieve this ambitious target we need to achieve the best results in more than just one area.” One obvious starting point is to raise the engine’s baseline combustion eficiency – by 3% in the case of Iveco’s 2020 diesels. “We expect innovation will be driven by customers’ needs to reduce fuel consumption and operating costs,” conirms Siracusa.
Iveco’s diesel engineers are exploring innovative multimode combustion solutions, based on a blend of processes including partial charge compression ignition (PCCI), used in conjunction with conventional compression ignition. To PCCI is added HCCI, or homogeneous charge compression ignition, whereby fuel is injected into the air intake, or early on in the compression stroke, to achieve a more homogeneous air/ fuel mixture, which is then ignited by normal compression.
The advantage of PCCI and HCCI is that they provide a colder combustion temperature, creating lower emissions – although HCCI is limited in application to partial load only. Another possible combustion tool is lifted lame, where the ignition lame starts further away from the injector nozzle, again resulting in a cooler combustion with less soot formation.
“Technologies such as pre-mix compression ignition, HCCI, PCCI and lifted lame give us the opportunity to effectively manage the combustion process from one mode to another to obtain better operating eficiency,” asserts Siracusa, adding: “There can be more improvements by variable valve timing in combination with lexible injection systems.”
Matchmaking
An even closer matching of the truck’s automated gearbox will also feature large on a 2020 engine. “Our goal is always to make the engine and after-treatment system work in the best region of thermal eficiency, not least through a fuel-optimising shift strategy,” says Siracusa.
Improving turbocharger eficiency is another area under the spotlight, with Iveco building on its existing HI-eSCR electronically controlled variable geometry turbocharger, adding roller bearings to further reduce friction. According to Siracusa, tomorrow’s turbo could have several faces. “We’re improving the turbo eficiency in many ways. By adopting a new concept, a lexible turbo technology that can work as a supercharger, a two-stage turbocharger or as a device to recover energy. Increased turbo eficiency leads to pumping loss reduction.” One intriguing (and seemingly contradictory) proposal from Iveco is to cool its 2020 engines by making them hotter. As part of FPT’s thermal management studies, Siracusa talks about raising the engine cooling temperature from the current 80-90C to 110C by 2020. Why? Because an increase in engine temperature could lead to lower engine friction losses through lower engine oil viscosity.
Another important aspect of thermal management under consideration is adopting switchable water pumps, which reduce fuel consumption by running only when required – what FPT calls tailored usage. The same principle can also be applied to the air compressor, alternator and oil and steering pumps – with low rates on the latter two being reduced at low load.
Likewise, any reductions in mechanical friction will pay dividends. “Just by reducing the piston group friction, you might reduce the total friction torque by about 10%,” reports Siracusa. “The con-rod-to-stroke ratio has an inluence on the resulting side forces of the piston and the max piston speed and therefore on friction.” Last but not least, intelligent alternators can store energy in an increased capacity battery during braking (ie regenerative braking) or when the engine is in a favourable point in the fuel consumption map. It could then be used instead of the electrical power provided directly by the alternator, for example when the vehicle is at cruising speed and electrical demand is lower. Stored excess energy could also be used to power ancillary equipment, or accessories like air-con.
Whichever technology is inally adopted for 2020, Siracusa says: “We must increase the fuel eficiency of the engine, where we expect to obtain a 3% gain, reduce the engine heat dispersion, where the gain would be another 3%, and recover energy from the exhaust gases through a water-heating system for a gain of 4%. This strategy allows us to address the most important issue for customers – fuel consumption.” And with diesel prices the way they are, who would argue with that? n
MAKING WASTE HEAT WORK
Arguably, the biggest challenge to raising the efficiency of any diesel is to recoup energy being lost out of its tail-pipe. And previous investigations by Iveco with the Glider into practical solutions look set to gather pace. Siracusa says: “We’re analysing the possibilities of converting heat back into energy, with the low-energy Rankine Cycle [effectively a steam generator powered by hot exhaust gases] to generate mechanical power back to the clutch and the Brayton Cycle [whereby compressed air is heated by the hot exhaust and expanded over a turbine] – both systems are being considered at this stage.” The potential gain from recycling exhaust heat shouldn’t be underestimated – a 4% improvement in efficiency derived from waste heat recovery could deliver an improvement in brake specific fuel consumption of up to 8%.