Trailers: should they lag behind?
Page 64
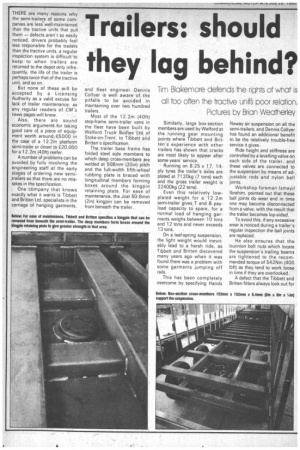
Page 65
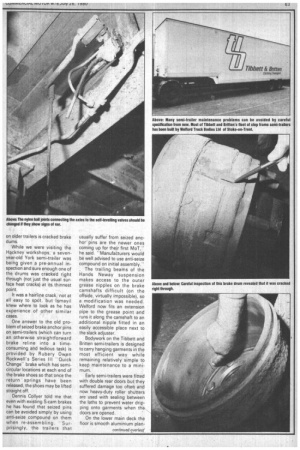
Page 66
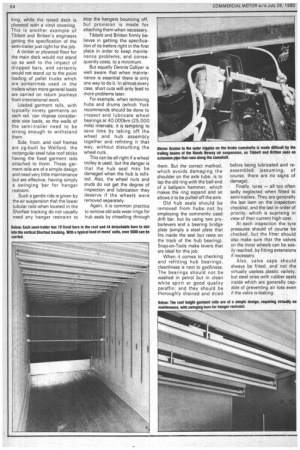
If you've noticed an error in this article please click here to report it so we can fix it.
Tim Blakemore defends he rights of what is all too often the tractive untt poor relation. Pictures by Brian Wea erley
THERE are many reasons why the semi-trailers of some companies are less well-maintained than the tractive units that pull them — defects aren't so easily noticed, drivers probably feel less responsible for the trailers than the tractive units, a regular inspection system is difficult to keep to when trailers are returned to the depot only infrequently, the life of the trailer is perhaps twice that of the tractive unit, and so on.
But none of these will be accepted by a Licensing Authority as a valid excuse for lack of trailer maintenance, as any regular readers of CM 's news pages will know.
Also, there are sound economic argument § for taking good care of a piece of equipment worth around £5000 in the case of a 12.2m platform semi-trailer or closer to £20,000 for a 12.2m (40f1) reefer.
A number of problems can be avoided by fully involving the engineering staff at the early stages of ordering new semitrailers so that there are no mistakes in the specification.
One company that knows exactly what it wants is Tibbett and Britten Ltd, specialists in the carriage of hanging garments. and fleet engineer Dennis Collyer is well aware of the pitfalls to be avoided in maintaining over two hundred trailers.
Most of the 12.2m (40ft) step-frame semi-trailer vans in the fleet have been built by Welford Truck Bodies Ltd of Stoke-on-Trent, to Tibbett and Britten's specification.
The trailer base frame has folded steel side mambers to which deep cross-members are welded at 508mm (20in) pitch and the full-width fifth-wheel rubbing plate is braced with longitudinal members forming boxes around the kingpin retaining plate. For ease of maintenance, the Jost 50.8mm (2in) kingpin can be removed from beneath the trailer. Similarly, large box-section members are used by Welford at the running gear mounting points where Tibbett and Britten's experience with other trailers has shown that cracks are most likely to appear after some years' service.
Running on 8.25 x 17, 14ply tyres the trailer's axles are plated at 7120kg (7 tons) each and the gross trailer weight is 22400kg (22 tons).
Even this relatively lowplated weight for a 12.2m semi-trailer gives T and B pay load capacity to spare, for a normal load of hanging gar ments weighs between 10 tons and 12 tons and never exceeds 13 tons.
On a leaf-spring suspension, the light weight would inevit ably lead to a harsh ride, as Tibbett and Britten discovered many years ago when it was found there was a problem with some garments jumping off rails.
This has been completely overcome by specifying Hands Neway air suspension on all the semi-trailers, and Dennis Collyer has found an additional benefit to be the relatively trouble-free service it gives.
Ride height and stiffness are controlled by a levelling valve on each side of the trailer, and these valves are connected to the suspension by means of ad-. justable rods and nylon ball joints.
Workshop foreman lsmayil Ibrahim, pointed out that these ball joints do wear and in time one may become disconnected from a valve, with the result that the trailer becomes lop-sided.
To avoid this, if any excessive wear is noticed during a trailer's regular inspection the ball joints are replaced.
He also ensures that the trunnion bolt nuts which locate the suspension's trailing beams are tightened to the recommended torque of 542N m (400 ibft) as they tend to work loose in time if they are overlooked.
A defect that the Tibbett and Britten fitters always look out for on older trailers is cracked brake durns.
While we were visiting the Hackney workshops, a seven year-old York semi-trailer was being given a pre-annual inspection and sure enough one of the drums was cracked right through (not just the usual surface heat cracks) at its thinnest point.
It was a hairline crack, not at all easy to spot, but lsmayil knew where to look as he has experience of other similar cases.
One answer to the old problem of seized brake anchor pins on semi-trailers (which can turn an otherwise straightforward brake reline into a time consuming and tedious task) is provided by Rubery Ow.en Rockwell's Series III "Quick
Changebrake which has semi
circular locations at each end of the brake shoes so that once the return springs have been released, the shoes may be lifted straight off.
Dennis Collyer told me that even with existing S-cam brakes he has found that seized pins can be avoided simply by using anti-seize compound on them when re-assembling. "Surprisingly, the trailers that usually suffer from seized anchor pins are the newer ones coming up for their first MoT,"' he said. "Manufacturers would be well advised to use anti-seize compound on initial assembly."
The trailing beams of the Hands Neway suspension makes access to the outer grease nipples on the brake camshafts difficult (on the offside, virtually impossible), so a modification was needed. VVelford now fits an extension pipe to the grease point and runs it along the camshaft to an additional nipple fitted in an easily accessible place next to the slack adjuster.
Bodywork on the Tibbett and Britten semi-trailers is designed to carry hanging garments in the most efficient way while remaining relatively simple to keep maintenance to a minimum.
Early semi-trailers were fitted with double rear doors but they suffered damage too often and now heavy-duty roller shutters are used with sealing between the laths to prevent water dripping onto garments when the doors are opened.
On the lower main deck the floor is smooth aluminium plan king, while the raised deck is plywood with a vinyl covering. This is another example of Tibbett and Britten's engineers getting the specification of the semi-trailer just right for the job.
A timber or plywood floor for the main deck would not stand up so well to the impact of dropped bars, and certainly would not stand up to the point loading of pallet trucks which are sometimes used in the trailers when more general loads are carried on return journeys from international work.
Loaded garment rails, with typically ninety garments on each rail, can impose considerable side loads, so the walls of the semi-trailer need to be strong enough to withstand them.
• Side, front, and roof frames are jig-built by Welford, the rectangular steel tube roof sticks having the fixed garment rails attached to them. These gar ment rails are of a simple design and need very little maintenance but are effective, having simply a swinging bar for hanger restraint.
Such a gentle ride is given by the air suspension that the lower tubular rails when located in the Shorfast tracking do not usually need any hanger restraint to stop the hangers bouncing off, but provision is made for attaching them when necessary. Tibbett and Britten firmly believes in getting the specification of its trailers right in the first place in order to keep maintenance problems, and consequently costs, to a minimum.
But equally Dennis Collyer is well aware that when mainte nance is essential there is only one way to do it. In almost every case, short cuts will only lead to more problems later.
For example, when removing hubs and drums (which York recommends should be done to inspect and lubricate wheel bearings at 40,000km (25,000 mile) intervals, it is tempting to save time by taking off the wheel and hub assembly together and refitting it that way, without disturbing the wheel nuts..
This can be.all right if a wheel trolley is used, but the danger is that the hub seal may be damaged when the hub is refitted. Also, the wheel nuts and studs do not get the degree of inspection and lubrication they deserve if the wheels were removed separately.
Again, it is common practice to remove old axle wear rings for hub seals by chiselling through them. But the correct method, which avoids damaging the shoulder on the axle tube, is to tap the old ring with the ball end of a ballpein hammer, which makes the ring 'expand and so allows it to be pulled off the axle.
Old hub seals should be removed from hubs not by employing the commonly used drift bar, but by using two prybelievers and a bearing bridge plate (simply a steel plate that fits inside the seal but rests on the track of the hub bearing). Snap-on-Tools make levers that are ideal for this job.
When it comes to checking and refitting hub bearings, cleanliness is next to godliness. The bearings should not be washed in petrol but in clean white spirit or good quality paraffin; and they should be thoroughly drained and dried before being lubricated and reassembled (assuming, of course, there are no signs of damage).
Finally, tyres — all too often sadly neglected when fitted to semi-trailers. They are generally the last item on the inspection checklist, and the last in order of priority, which is suprising in view of their current high cost.
At each inspection the tyre pressures should of course be checked, but the fitter should also make sure that the valves on the inner wheels can be easily reached, by fitting extensions if necessary.
Also, valve caps should always be fitted, and not the virtually useless plastic variety, but steel ones with rubber seals inside which are generally capable of preventing air loss even if the valve is leaking.