From the Drawing Boer
Page 48
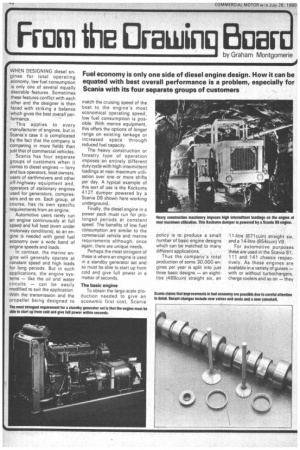
Page 49
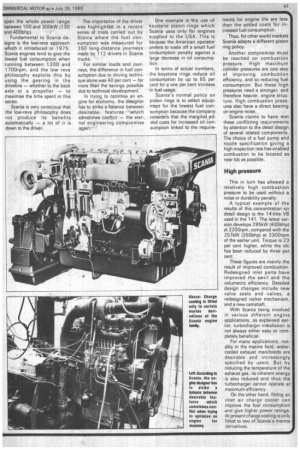
If you've noticed an error in this article please click here to report it so we can fix it.
by Graham Montgomerie
WHEN DESIGNING diesel engines for total operating economy, low fuel consumption is only one of several equally desirable features. Sometimes these features conflict with each other and the designer is then faced with striking a balance which gives the best overall performance.
This applies to every manufacturer of engines, but in. Scania's case it is complicated by the fact that the company is competing in more fields than just that of commercial vehicles.
Scania has four separate groups of customers when it comes to diesel engines — lorry and bus operators, boat owners, users of earthmovers and other off-highway equipment and, operators of stationary engines used for generators, compressors and so on. Each group, of course, has its own specific requirements from an engine.
Automotive users rarely run an engine continuously at full speed and full load (even under motorway conditions), so an engine is needed with good fuel economy over a wide band of engine speeds and loads.
In contrast, the marine engine will generally operate at constant speed and high loads for long periods. But in such applications, the engine systems — like the oil and water circuits — can be easily modified to suit the application. With the transmission and the propeller being designed to match the cruising speed of the boat to the engine's most economical operating speed, low fuel consumption is possible. With marine equipment, this offers the options of longer range on existing tankage or increased space through reduced fuel capacity.
The heavy construction or forestry type of operation imposes an entirely different duty cycle with high intermittent loadings at near maximum utilisation over one or more shifts per day. A typical example of this sort of use is the Kockums 412T dumper powered by a Scania D8 shown here working underground.
Finally, the diesel engine in a power pack must run for prolonged periods at constant speed. The benefits of low fuel consumption are similar to the commercial vehicle and marine requirements although, once again, there are unique needs.
Perhaps the most stringent of these is where an engine is used in a standby generator set and so must be able to start up from cold and give full power in a matter of seconds.
The basic engine To obtain the large-scale production needed to give an economic first cost, Scania policy is to produce a small number of basic engine designs which can be matched to many different applications.
Thus the company's total production of some 30,000 engines per year is split into just three basic designs — an eightlitre (488cuin) straight six, an 11-litre (671cuin) straight six, and a 14-litre (854cuin) V8.
For automotive purposes these are used in the Scania 81, 111 and 141 chassis respectively. As these engines are available in a variety of guises — with or without turbochargers, charge coolers and so on — they span the whole power range between 100 and 300kW (130 and 400bhp).
Fundamental to Scania designs is the low-revs approach which it introduced in 1975, Scania engines tend to give the lowest fuel consumption when running between 1200 and 1700rpm, and the low revs philosophy exploits this by using the gearing in the driveline — whether to the back axle or a propeller — to maximise the time spent in this sector.
Scania is very conscious that the low-revs philosophy does not produce its benefits automatically — a lot of it is down to the driver. The importance of the driver was highlighted in a recent series of trials carried out by Scania where the fuel consumption was measured for 350 long-distance journeys made by 112 drivers in Scania trucks.
For similar loads and journeys, the difference in fuel consumption due to driving technique alone was 40 per cent — far more than the savings possible due to technical development.
In trying to optimise an engine for economy, the designer has to strike a balance between desirable features which sometimes conflict — the eternal engineering compromise again. One example is the use of keystone piston rings which Scania uses only for engines supplied to the USA. This is because the American operator prefers to trade off a small fuel consumption penalty against a large decrease in oil consumption.
In terms of actual numbers, the keystone rings reduce oil consumption by up to 65 per cent for a one per cent increase in fuel usage.
Scania's normal policy on piston rings is to select equipment for the lowest fuel consumption because the company considers that the marginal added costs for increased oil consumption linked to the require ments for engine life are less than the added costs for increased fuel consumption.
Thus, for other world markets Scania adapts a different piston ring policy.
Another compromise must be reached on combustion pressure. High maximum cylinder pressures are one way of improving combustion efficiency, and so reducing fuel consumption. But these high pressures need a stronger, and therefore heavier, engine structure. High combustion pressures also have a direct bearing on engine noise.
Scania claims to have met these conflicting requirements by attention to the detail design of several related components. The choice of a fuel pump and nozzle specification giving a high inspection rate has enabled combustion to be located as near tde as possible.
High pressure
This in turn has allowed a relatively high combustion pressure to be used without a noise or durability penalty.
A typical example of the results of this concentration on detail design is the 14-litre V8 used in the 141. The latest version develops 295kW (400bhP) at 2200rpm, compared with the 257kW (350bhp) at 2300rpm of the earlier unit. Torque is 23 per cent higher, while the sfc has been reduced by three per cent.
These figures are mainly the result of improved combustion. Redesigned inlet ports have improved the swirl and the volumetric efficiency. Detailed design changes include new valve seats and valves, a redesigned rocker mechanism, and a new camshaft.
With Scania being involved in various different engine applications, as explained earlier, turbocharger installation is not always either easy or completely beneficial_ For many applications, notably in the marine field, watercooled exhaust rnanifoleds are desirable and increasingly specified by users. But by reducing the temperature of the exhaust gas, its inherent energy is also reduced and thus the turbocharger cannot operate at maximum efficiency.
On the other hand, fitting an inlet air charge cooler can improve the fuel consumption and give higher power ratings. At present charge cooling is only fitted to two of Scania's marine derivatives_