Secrets of Henley Tyre Production
Page 48
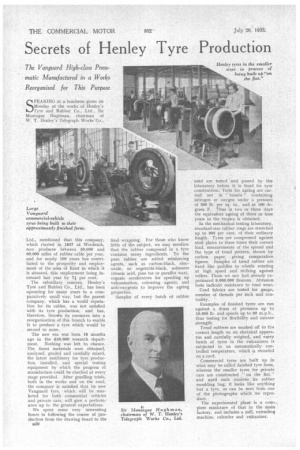
If you've noticed an error in this article please click here to report it so we can fix it.
SPEAKING at a luncheon given on brIonday at the works of Henley's Tyre and Rubber Co., Ltd., Sir Montague Hughman, chairman of W. T. Henley's Telegraph.Works Co.,
Ltd., mentioned that this company, which started in 1837 at Woolwich, now produces between 50,000 and 60,000 miles of rubber cable per year, and for nearly 100 years has contributed to the prosperity and employment of the area of Kent in which it is situated, this employment being increased last year by 74per cent.
The subsidiary concern, Henley's Tyre and Rubber Co., Ltd.', has been operating for many years in a comparatively small Way, but the parent company, which has a world reputation for its cables, was not satisfied with its tyre production, and has, therefore, thrown its resources into a reorganization of this branch to enable it to produce a tyre which would be second to none.
The new era was born 18 months ago in the £40,000 research department. Nothing was left to chance. The finest materials were obtained, analysed, graded and carefully mixed, the latest machinery for tyre production installed, and special testing equipment by which the progress of manufacture could be checked at every stage provided. After gruelling trials, both in the works and on the road, the company is satisfied that its new Vanguard tyre, which will be marketed for both commercial vehicles and private cars, will give a performance up to the greatest expectations.
We spent some very interesting hours in following the course of production from the drawing board to the B30 final wrapping. For those who know little of the subject, we may mention that the rubber compound in a tyre contains many ingredients. To the pure rubber are added reinforcing agents, such as carbon-black, zincoxide, or vegetable-black, softeners (stearic acid, pine tar or paraffin wax), organic accelerators for speeding up vulcanization, colouring agents, and anti-oxygents to improve the ageing properties.
Samples of every batch of rubber used are tested and passed by the laboratory before it is freed for tyre construction. Tests for ageing are carried out in " bombs " containing nitrogen or oxygen under a pressure of 300 lb. per sq. in., and at 160 degrees F. Thus in two or three days the equivalent ageing of three or four years in the tropics is obtained.
In the mechanical testing laboratory, standard-size rubber rings are stretched up to 900 per cent, of their ordinary length. Tyres are compressed against steel plates to three times their correct load, measurements of the spread and the type of tread pattern, shown by carbon paper, giving comparative figures. Samples of tread rubber are fixed like paddles to wheels rotating at high speed and striking against rollers. Those we saw had already experienced 9,000,000 flexions. Abrasion tests indicate resistance to road wear.
Cord fabrics are tested for gauge, number of threads per inch and centrality.
Examples of finished tyres are run against a drum at pressures up to 1,0,000 lb. and speeds up to 90 m.p.h., thus testing for flexibility and carcase strength.
Tread rubbers are marked off to the correct length on an electrical apparatus and carefully weighed, and euery batch of tyres in the vulcanizers is subjected to an automatically controlled temperature, which is recorded on a card.
Commercial tyres are built up in what may he called finished tyre form, whereas the smaller tyres for private cars are constructed " on the flat," and until each receives its rubber moulding bag, it looks like anything but a tyre, as can be seen from one of the photographs which we repro' duce.
• The experimental plant is a complete miniature of that in the main factory, and includes a mill, extruding machine, calender and vulcanizer.