OPERATOR PROFILE CONOCO
Page 41
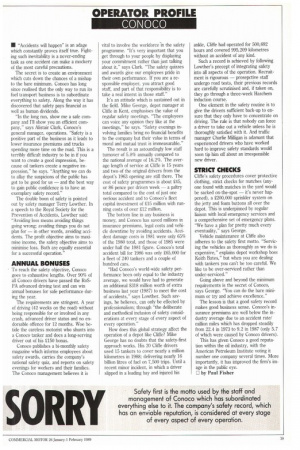
If you've noticed an error in this article please click here to report it so we can fix it.
• "Accidents will happen" is an adage which constantly proves itself true. Fighting such inevitability is a never-ending task as one accident can make a mockery of the most careful precautions.
The secret is to create an environment which cuts down the chances of a mishap to the bare minimum. Conoco has long since realised that the only way to run its fuel transport business is to subordinate everything to safety. Along the way it has discovered that safety pays financial as well as human dividends.
"In the long run, show me a safe company and I'll show you an efficient company," says Alistair Clark, Conoco's general manager, operations. "Safety is a positive part of the business as it leads to lower insurance premiums and trucks spending more time on the road. This is a terribly difficult industry to be in if you want to create a good impression, because oil tankers create a negative impression," he says. "Anything we can do to allay the suspicions of the public has got to be good for us — and the best way to gain public confidence is to have an exemplary safety record."
The double boon of safety is pointed out by safety manager Terry Lowther. In a speech to the Royal Society for the Prevention of Accidents, Lowther said: "Avoiding loss means avoiding things going wrong; avoiding things you do not plan for — in other words, avoiding accidents. The profit objective aims to maximise income, the safety objective aims to minimise loss. Both are equally essential for a successful operation."
ANNUAL BONUSES
To reach the safety objective, Conoco goes to exhaustive lengths. Over 90% of all Conoco drivers have passed the RoSPA advanced driving test and can win annual bonuses for safe performance during the year.
The requirements are stringent. A year of driving (42 weeks on the road) without being responsible for or involved in any crash, advanced driver status and no endorsable offence for 12 months. Woe betide the careless motorist who shunts into a Conoco tanker and does a long-serving driver out of his £150 bonus.
Conoco publishes a hi-monthly safety magazine which informs employees about safety awards, carries the company's national safety quiz, and reports on safety evenings for workers and their families. The Conoco management believes it is
vital to involve the workforce Inthe safety programme. "It's very important that you get through to your people by displaying your commitment rather than just talking about it," says Clark. "The safety quizzes and awards give our employees pride in their own performance. If you are a responsible employer, you attract good staff, and part of that responsibility is to take a real interst in those staff."
It's an attitude which is sustained out in the field. Mike George, depot manager at Cliffe in Kent, emphasises the value of regular safety meetings. "The employees can voice any opinion they like at the meetings," he says. "Safety evenings involving families bring no financial benefits to the company but their value in terms of moral and mutual trust is immeasurable."
The result is an astoundingly low staff turnover of 5.8% annually compared to the national average of 16.2%. The average length of service at Ode is 15 years and two of the original drivers from the depot's 1963 opening are still there. The cost of safety programmes is about £45, or 86 pence per driven week — a paltry total compared to the cost of just one serious accident and to Conoco's fleet capital investment of £15 million with running costs of over £12 million.
The bottom line in any business is money, and Conoco has saved millions in insurance premiums, legal costs and vehicle downtime by avoiding accidents. Accident damage costs in 1981 were only 65% of the 1980 total, and those of 1985 were under half the 1981 figure. Conoco's total accident bill for 1986 was only £65,000 for a fleet of 240 tankers and a couple of hundred cars.
"Had Conoco's world-wide safety performance been only equal to the industry average, we would have had to generate an additional $318 million worth of extra business last year (1987) to meet the cost of accidents," says Lowther. Such savings, he believes, can only be effected by professionalism; through "the deliberate and methodical inclusion of safety considerations at every stage of every aspect of every operation."
How does this global strategy affect the operation of a depot like Cliffe? Mike George has no doubts that the safety-first approach works. His 20 Cliffe drivers used 15 tankers to cover nearly a million kilometres in 1988; delivering nearly 16 billion litres of fuel on 7,500 trips. Until a recent minor incident, in which a driver slipped in a loading bay and injured his ankle, Cliffe had operated for 500,692 hours and covered 995,209 kilometres without an accident of any kind.
Such a record is achieved by following Lowther's precept of integrating safety into all aspects of the operation. Recruitment is rigourous — prosepctive staff undergo road tests, their previous records are carefully scrutinised and, if taken on, they go through a three-week Hazchem induction course.
One element in the safety routine is to give the drivers sufficient back-up to ensure that they only have to concentrate on driving. The rule is that nobody can force a driver to take out a vehicle unless he is thoroughly satisfied with it. And traffic manager Charlie Milligan is adamant that experienced drivers who have worked hard to improve safety standards would soon tip him off about an irresponsible new driver.
STRICT CHECKS
Cliffe's safety procedures cover protective clothing, strict checks for matches (anyone found with matches in the yard would be sacked on-the-spot — it's never happened), a £200,000 sprinkler system on the jetty and foam buttons all over the depot. This is underpinned by regular liaison with local emergency services and a comprehensive set of emergency plans. "We have a plan for pretty much every eventuality," says George.
Vehicle maintenance at Cliffe also adheres to the safety first motto. "Servicing the vehicles as thoroughly as we do is expensive," explains depot workshop boss Keith Bates," but when you are dealing with tankers you can't be too careful. We like to be over-serviced rather than under-serviced."
Going above and beyond the minimum requirements is the secret of Conoco, says George. "You can do the bare minimum or try and achieve excellence."
The lesson is that a good safety record makes good business sense. Conoco's insurance premiums are well below the industry average due to an accident rate/ million miles which has dropped steadily from 22.4 in 1973 to 9.2 in 1987 (only 5.7 of which were caused by Conoco drivers).
This has given Conoco a good reputation within the oil industry, with the American Petroleum Institute voting it number one company several times. More importantly, it has improved the firm's image in the public eye.
El by Paul Fisher