Take a deep breath
Page 114
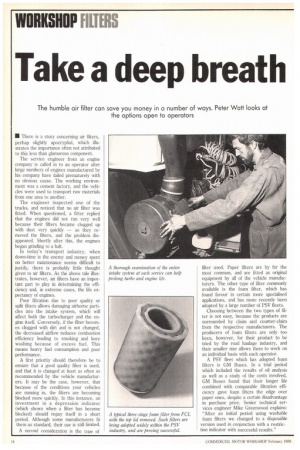
Page 115
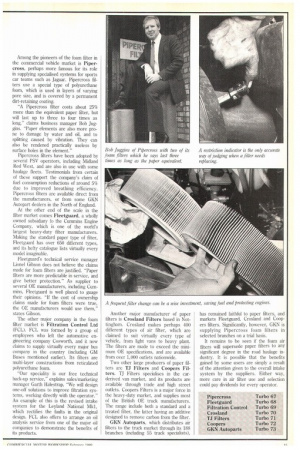
If you've noticed an error in this article please click here to report it so we can fix it.
• There is a story concerning air filters, perhap slightly apocryphal, which illustrates the importance often not attributed to this less than glamorous component.
The service engineer from an engine company is called in to an operator after large numbers of engines manufactured by his company have failed prematurely with no obvious cause. The working environment was a cement factory, and the vehicles were used to transport raw materials from one area to another.
The engineer inspected one of the trucks, and noticed that no air filter was fitted. When questioned, a fitter replied that the engines did not run very well because their filters became clogged up with dust very quickly — so they removed the filters, and the problem disappeared. Shortly after this, the engines began grinding to a halt.
In today's transport industry, when down-time is the enemy and money spent on better maintenance seems difficult to justify, there is probably little thought given to air filters. As the above tale illustrates, however, air filters have an important part to play in determining the efficiency and, in extreme cases, the life expectancy of engines.
Poor filtration due to poor quality or split filters allows damaging airborne particles into the intake system, which will affect both the turbocharger and the engine itself, Conversely, if the filter becomes clogged with dirt and is not changed, the decreased airflow reduces combustion efficiency leading to smoking and bore washing because of excess fuel. This means heavy fuel consumption and poor performance.
A first priority should therefore be to ensure that a good quality filter is used, and that it is changed at least as often as recommended by the vehicle manufacturers. It may be the case, however, that because of the conditions your vehicles are running in, the filters are becoming blocked more quickly. In this instance, an investment in a depression indicator (which shows when a filter has become blocked) should repay itself in a short period. Although some manufacturers fit them as standard, their use is still limited.
A second consideration is the type of
A typical three-stage foam filler from FCL with the top lid removed. Such filters are being adopted widely within the PSV industry, and are proving successful.
filter used. Paper filters are by far the most common, and are fitted as original equipment by all of the vehicle manufacturers. The other type of filter commonly available is the foam filter, which has found favour in certain more specialised applications, and has more recently been adopted by a large number of PSV fleets.
Choosing between the two types of filter is not easy, because the products are surrounded by claim and counter-claim from the respective manufacturers. The producers of foam filters are only too keen, however, for their product to be tried by the road haulage industry, and their smaller size allows them to work on an individual basis with each operator.
A PSV fleet which has adopted foam filters is GM Buses. In a trial period which included the results of oil analysis as well as a study of the costs involved, GM Buses found that their longer life combined with comparable filtration efficiency gave foam filters the edge over paper ones, despite a certain disadvantage in purchase price. Senior technical services engineer Mike Greenwood explains: "After an initial period using washable foam filters we changed to a disposable version used in conjunction with a restriction indicator with successful results."
Among the pioneers of the foam filter in the commercial vehicle market is Piper cross, perhaps more famous for its role
in supplying specialised systems for sports car teams such as Jaguar. Pipercross fil ters use a special type of polyurethane foam, which is used in layers of varying pore size, and is covered by a permanent dirt-retaining coating.
"A Pipercross filter costs about 25% more than the equivalent paper filter, but will last up to three to four times as long," claims business manager Bob Jug gins. "Paper elements are also more prone to damage by water and oil, and to splitting caused by vibration. They can also be rendered practically useless by surface holes in the element."
Pipercross filters have been adopted by several PSV operators, including Midland Red West, and are also in use with some haulage fleets. Testimonials from certain of these support the company's claim of fuel consumption reductions of around 5% due to improved breathing efficiency. Pipercross filters are available direct from the manufacturers, or from some GKN Autopart dealers in the North of England.
At the other end of the scale in the filter market comes Fleetguard, a wholly owned subsidiary fo the Cummins Engine Company, which is one of the world's largest heavy-duty filter manufacturers. Making the standard paper type of filter, Fleetguard has over 650 different types, and its hefty catalogue lists virtually every model imaginable.
Fleetguard's technical service manager Lionel Gibson does not believe the claims made for foam filters are justified. "Paper filters are more predictable in service, and give better protection." As supplier to several OE manufacturers, including Cummins, Fleetguard is well placed to guage their opinions. "If the cost of ownership claims made for foam filters were true, the OE manufacturers would use them," states Gibson.
The other major company in the foam filter market is Filtration Control Ltd (FCL). FCL was formed by a group of employees who left the automotive engineering company Cosworth, and it now claims to supply virtually every major bus company in the country (including GM Buses mentioned earlier). Its filters are multi-layer constructions from reticulated polyurethane foam.
"Our speciality is our free technical back-up service," explains sales/marketing manager Garth Halestrap, "We will design one-off solutions to improve filtration systems, working directly with the operator." An example of this is the revised intake system for the Leyland National Mk 1, which rectifies the faults in the original design. FCL also offers to arrange an oil analysis service from one of the major oil companies to demonstrate the benefits of its products.
Another major manufacturer of paper filters is Crosland Filters based in Nottingham. Crosland makes perhaps 400 different types of air filter, which are claimed to suit virtually every type of vehicle, from light vans to heavy plant. The filters are made to exceed the minimum OE specifications, and are available from over 1,000 outlets nationwide.
Two other large producers of paper filters are TJ Filters and Coopers Filters, TJ Filters specialises in the carderived van market, and its products are available through trade and high street outlets. Coopers Filters is a major force in the heavy-duty market, and supplies most of the British OE truck manufacturers. The range include both a standard and a treated filter, the latter having an additive designed to remove carbon from the filter.
GKN Autoparts, which distributes air filters to the truck market through its 188 branches (including 55 truck specialists),
has remained faithful to paper filters, and markets Fleetguard, Crosland and Coopers filters. Significantly, however, GKN is supplying Pipercross foam filters in selected branches on a trial basis.
It remains to be seen if the foam air filters will supersede paper filters to any significant degree in the road haulage industry. It is possible that the benefits gained by some users are simply a result of the attention given to the overall intake system by the suppliers. Either way, more care in air filter use and selection could pay dividends for every operator.