The multi-purpose body option is now the trend
Page 61
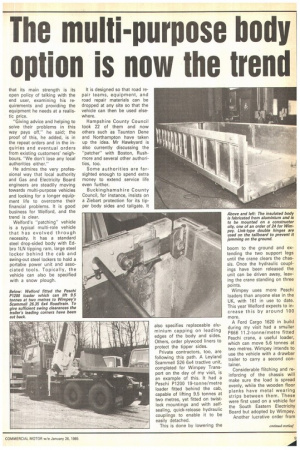
Page 62
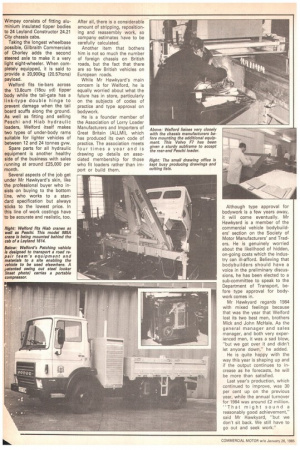
If you've noticed an error in this article please click here to report it so we can fix it.
that its main strength is its open policy of talking with the end user, examining his requirements and providing the equipment he needs at a realistic price.
"Giving advice and helping to solve their problems in this way pays off," he said; the proof of this, he added, is in the repeat orders and in the inquiries and eventual orders from existing customers' neighbours. "We don't lose any local authorities either."
He admires the very professional way that local authority and Gas and Electricity Board engineers are steadily moving towards multi-purpose vehicles and looking for a longer equipment life to overcome their financial problems. It is good business for Welford, and the trend is clear.
Welford's "patching" vehicle is a typical multi-role vehicle that has evolved through necessity. It has a standard steel drop-sided body with Edbro 1LN tipping ram, large steel locker behind the cab and swing-out steel lockers to hold a portabie power unit and associated tools. Topically, the vehicle can also be specified with a snow plough. It is designed so that road repair teams, equipment, and road repair materials can be dropped at any site so that the vehicle can then be used elsewhere.
Hampshire County Council took 22 of them and now others such as Taunton Dene and Northampton have taken up the idea. Mr Hawkyard is also currently discussing the "patcher" with Boston, Rushmore and several other authorities, too.
Some authorities are farsighted enough to spend extra money to extend service life even further.
Buckinghamshire County Council, for instance, insists on a Ziebart protection for its tipper body sides and tailgate. It also specifies replaceable aluminium capping on leading edges of the body and sides. Others, order plywood liners to protect the tipper sides.
Private contractors, too, are following this path. A Leyland Scammell S26 6x4 tractive unit, completed for Wimpey Transport on the day of my visit, is an example of this. It had a Peschi P1200 19-tonne/metre loader fitted behind the cab, capable of lifting 9.5 tonnes at two metres, yet fitted on twistlock mountings and with selfsealing, quick-release hydraulic couplings to enable it to be easily detached.
This is done by lowering the boom to the ground and extending the two support legs until the crane clears the chassis. Once the hydraulic couplings have been released the unit can be driven away, leaving the crane standing on three points.
Wimpey uses more Peschi loaders than anyone else in the UK, with 161 in use to date. This year We'ford expects to increase this by around 100 more.
A Ford Cargo 1620 in build during my visit had a smaller P666 11.2-tonne/metre fitted Peschi crane, a useful loader, which can move 5.6 tonnes at two metres. Wimpey intends to use the vehicle with a drawbar trailer to carry a second container.
Considerable flitching and reinforcing of the chassis will make sure the load is spread evenly, while the wooden floor planks have metal wearing strips between them. These were first used on a vehicle for the South Eastern Electricity Board but adopted by Wimpey.
Another lucrative order from Wimpey consists of fitting aluminium insulated tipper bodies to 24 Leyland Constructor 24.21 City chassis cabs.
Taking the longest wheelbase possible, Gilbraith Commercials of Charley adds the second steered axle to make it a very light eight-wheeler. When completely equipped, it is said to provide a 20,900kg (20.57tons) payload.
Welford fits tie-bars across the 13.8cum (18cu yd) tipper body while the tail-gate has a link-type double hinge to prevent damage when the tail board scuffs along the ground. As well as fitting and selling Peschi and Hiab hydraulic loaders, Welford Itself makes two types of under-body rams suitable for lighter vehicles of between 12 and 24 tonnes gvw.
Spare parts for all hydraulic equipment is another healthy side of the business with sales cunning at around £25,000 per month.
Several aspects of the job get under Mr Hawkyard's skin, like the professional buyer who insists on buying to the bottom line, who works to a standard specification but always sticks to the lowest price. In this line of work costings have to be accurate and realistic, too.
After all, there is a considerable amount of stripping, repositioning and reassembly work, so company estimates have to be carefully calculated.
Another item that bothers him is not so much the number of foreign chassis on British roads, but the fact that there are so few British vehicles on European roads.
While Mr Hawkyard's main concern is for Welford, he is equally worried about what the future has in store, particularly on the subjects of codes of practice and type approval on bodywork.
He is a founder member of the Association of Lorry Loader Manufacturers and Importers of Great Britain (ALLMI), which has produced its own code of practice. The association meets four times a year and is drawing up details on associated membership for those who fit loaders rather than import or build them. Although type approval for bodywork is a few years away, it will come eventually. Mr Hawkyard is a member of the commercial vehicle bodybuilders' section on the Society of Motor Manufacturers' and Traders. He is genuinely worried about the likelihood of hidden, on-going costs which the industry can ill-afford. Believing that bodybuilders should have a voice in the preliminary discussions, he has been elected to a sub-committee to speak to the Department of Transport, before type approval for bodywork comes in.
Mr Hawkyard regards 1984 with mixed feelings because that was the year that Welford lost its two best men, brothers Mick and John McHale. As the general manager and sales manager, and both very experienced men, it was a sad blow, "but we got over it and didn't let anyone down," he added.
He is quite happy with the way this year is shaping up and if the output continues to increase as he forecasts, he will be more than satisfied.
Last year's production, which continued to improve, was 30 per cent up on the previous year, while the annual turnover for 1984 was around £2 million. "That might sound a reasonably good achievement," said Mr Hawkyard, "but we don't sit back. We still have to go out and seek work."