Safety measures: (111) 'Just a bob-a-job'
Page 41
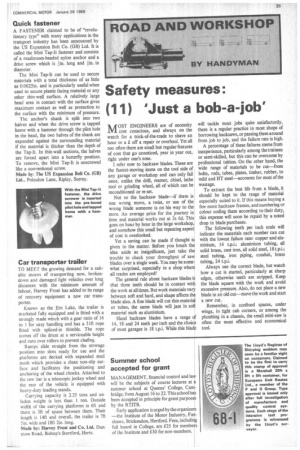
If you've noticed an error in this article please click here to report it so we can fix it.
MOST ENGINEERS are of necessity cost conscious, and always on the watch for a trick-of-the-trade to shave an hour or a £ off a repair or overhaul. Yet all too often there are small but regular features of cost that go unnoticed, year in year out, right under one's nose.
I refer now to hacksaw blades. These are the fastest-moving items on the tool side of, any garage or workshop and can only fail " once, unlike the drill, reamer, chisel, lathel tool or grinding wheel, all of which can be reconditioned or re-set.
Not so the hacksaw blade—if there is ' one wrong move, a twist, or use of the r wrong blade someone is on his way to the store. An average price for the journey in time and material works out at 2s 6d. This goes on hour by hour in the large workshop,. and somehow this small but repeating aspectl of cost is overlooked.
Yet a saving can be made if thought is given to the matter. Before you brush the idea aside as insignificant, just take the trouble to check your throughput of saW blades over a single week. You may be some what surprised, especially in a shop where all trades are employed!
The general rule about hacksaw blades is that three teeth should be in contact with the work at all times. But work materials vary between soft and hard, and shape affects the blade also. A fine blade will cut thin material or tubes, the same blade will jam in soft material such as aluminium.
Hand hacksaw blades have a range of 14, 18 and 24 teeth per inch and the choice of most garages is 18 t.p.i. While this blade will tackle most jobs quite satisfactorily, there is a regular practice in most shops of borrowing hacksaws, or passing them around from job to job, and the failure rate is high.
A percentage of these failures stems from inexperience, particularly among the trainees or semi-skilled, but this can be overcome by professional tuition. On the other hand, the wide range of materials to be cut—from bolts, rods, tubes, plates, timber, rubber, to mild and HT steel—accounts for most of the wastage.
To extract the best life from a blade, it should be kept to the range of material especially suited to it. If this means buying a few more hacksaw frames, and numbering or colour coding them according to their duty, this expense will soon be repaid by a noted drop in blade purchases.
The following teeth per inch scale will indicate the materials each number can cut with the lowest failure rate: copper and aluminium, 14 t.p.i.; aluminium tubing, all solid brass, cast iron, all solid steel, 18 t.p.i.; steel tubing, iron piping, conduit, brass tubing, 24 t.p.i.
Always use the correct blade, but watch how a cut is started, particularly at sharp edges, otherwise teeth are stripped. Keep the blade square with the work and avoid excessive pressure. Also, do not place a new blade in an old cut—move the work and start a new cut.
Remember, in confined spaces, under wings, in tight cab corners, or among the plumbing in a chassis, the small mini-saw is often the most effective and economical tool.