New All-metal Double-deck Body Construction
Page 34
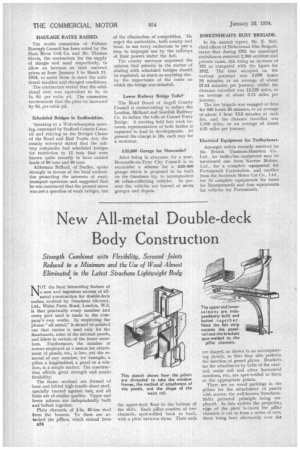
Page 35
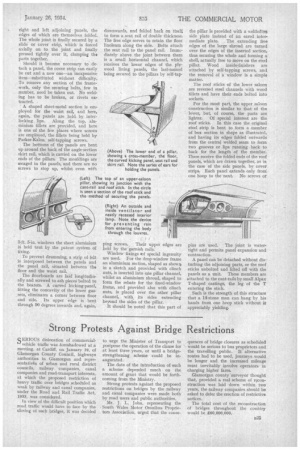
If you've noticed an error in this article please click here to report it so we can fix it.
NOT the least interesting feature of a new and ingenious system of allmetal construction for double-deck bodies, evolved by Strachans (Acton), Ltd., Wales Farm Road, London, W.3, is that practically every member and every part used is made in the company's own works. In employing the phrase "all metal," it should be pointed out that timber is used only for the floorboards, some of the internal panels, and fillets in certain of the frame members. Furthermore, the number of screws employed as a means for attachment of panels, etc-, is low, yet the removal of any member, for example, a pillar, a longitudinal, a panel or a window, is a simple matter. The construction affords great strength and ample The frame sections are formed of bent and folded high-tensile sheet steel, specially treated against rust, and all bolts are of similar quality. Upper and lower saloons are independently built and bolted together. Plain channels a 1-in. 45-ton steel form the bearers. To these are attached the pillars, which extend from
the upper-deck floor to the bottom of the skirt. Each pillar consists of two channels, spot-welded back to back, with a plate between them. Their ends are shaped, as shown in an accompanying sketch, so that they also perform the function of gusset plates. Brackets for the attachment by bolts of the cantrail, waist rail and other horizontal members, etc., are spot-welded to them at the appropriate points.
There are no wood packings in the pillars for the attachment of panels with screws, the well-known ,StrachansMeltz patented principle being employed.In this system the projecting edge of the plate b6ween the pillar channels is cut to form a series of ears, these being bent alternately over the
right and left adjoining panels, the edges of which are themselves folded. The whole joint is finally secured by a slide or cover strip, which is forced axially on to the joint and finally pressed tightly over it, clamping the parts together.
Should it become necessary to detach a panel, the cover strip can easily be cut and a new one—an inexpensive item—substituted without difficulty. To remove any section of the framework, only the securing bolts, few in number, need be taken out, No welding has to be broken, or rivets extracted.
A shaped sheet-metal section is employed for the waist rail, and here, again, the panels are held by inter
locking lips. Along the top, aluminium fillets are provided, and here is one of the few places where screws are employed, the fillets being held by Parker-Kalon self-tapping screws.
The bottoms of the panels are bent up around the back of the angle-section skirt rail, which is carried on the lower ends of the pillars. The mouldings are swaged in the panels, and there are no screws to stop up, whilst even with
3-ff. 5-in. windows the sheet aluminium is held taut by the patent system. of fixing.
To prevent drumming, a strip of felt is interposed between the panels and the panel rail, situated between the floor and the waist rail.
The floorboards are laid longitudinally and screwed to ash pieces bolted to the bearers. A curved kicking-panel, fitting the concavity of the lower gussets,' eliminates a corner between floor and side. Its upper edge is bent through 90 degrees inwards and, again, downwards, and folded bacir on itself to form a seat rail of double thickness. The free edge serves to retain the floor linoleum along the side. Bolts attach the seat rail to the panel railImmediately above the joint between them is a small horizontal channel, which receives the lower edges of the plywood lining panels, the last-named being secured to the pillars by self-tap ping screws., Their upper edges are held by the garnish rails.
Window fixings dot special ingenuity are used. For the drop-window frame an aluminium section, shaped as shown, in a sketch and provided with clinch nuts, is inserted into one pillar channel, whilst an aluminium shroud, shaped to form the rebate for the fixed-window frame, and provided also with clinch nuts, is placed over the other pillar channel, with its sides extending beyond the sides of the pillar.
It should be noted that this part of the pillar is provided with a weldedkrn side plate instead of an eared inter mediate plate. The extending free edges of the large shroud are turned over the edges of the inserted section, thus securing the whole and forming a shell, actually free to move on the steel pillar. Wood inside-finishers are attached by self-tapping screws, and the removal of a window is a simple matter.
The roof sticks of the lower saloon are reversed steel channels with wood fillets and have their ends bolted into sockets.
For the most part, the upper saloon construction is similar to that of the lower, but, of course, the parts are lighter. Of special interest are the roof sticks. In this case the original steel strip is bent to form a member of box section in shape as illustrated. and having its edges folded outwards from the central welded seam to form two grooves or lips running back to back for the length of the member. • These receive the folded ends of the roof panels, which are drawn together, as in the case of the side panels, by cover strips. Each panel extends only from one hoop to the next. No screws or pins are used. The joint is watertight and permits panel expansion and contraction.
A panel can be detached without dis, turbing the adjoining parts, or the roof sticks unbolted and lifted off with the panels as a unit. These members are attached to the cant-rails by: small Alpax T-shaped castings, the leg of the T entering the stick.
Such is the strength of this structure that a 14-stone man can hang by his hands from one hoop stick without it appreciably yielding.