A New Hydraulic Press for Assembling Torque Tubes.
Page 18
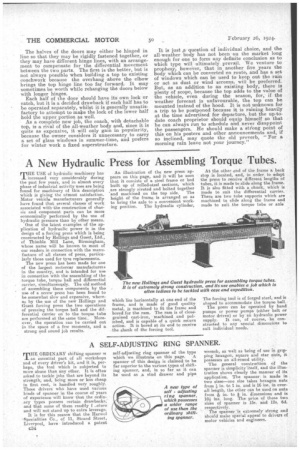
If you've noticed an error in this article please click here to report it so we can fix it.
THE USE of hydraulic machinery has increased very considerably during the past few years, and in almost every phase of industrial activity uses are being found for machinery of this description which is giving the utmost satisfaction. Motor vehicle manufacturers generally have found that several classes of work associated with the construction of chassis and component parts can be more economically performed by the use of hydraulic pressure than by other means.
One of the latest examples of the application of hydraulic power is in the design of a forcing press which is being constructed by Hollings and Guest, Ltd., of Thimble Mill Lane, Birmingham, whose name will be known to most of our readers in connection with the manufacture of all classes of press, particularly those used for tyre replacements. The new press has been made for one of the largest motorcar manufacturers in the country, and is intended for use in connection with the assembling of the torque tube, torque ball and differential carrier, simultaneously. The old method of assembling these components by the use of a screw press has been found to be somewhat slow and expensive, whereas by the use of the new Hollings and Guest forcing press the two operations of pressing the torque ball and the differential carrier on to the torque tube are performed at the same time.. Moreover, the operation can be carried out in the space of a few moments, and a strong and sound job results. . An illustration of the new press appears on this page, and it will be seen that, it consists of a steel frame or bed built up of rolled-steel sections, which are strongly riveted and bolted together and machined on the top side. The height of the frame is arranged so as to bring the axle to a convenient work ing position. The hydraulic cylinder, which lies horizontally at one end of the frame, and is made of good quality metal, is machined to fit the frame and bored for the ram. The ram is of closegrained cast-iron, machined and polished, and is capable of a quick return action. It is bored at its end to receive the shank of the forcing tool. At the other end of the frame a back stop is located, and, in order to adapt the press to receive different lengths of tubes, it is made to slide along the frame. It is also fitted with a chuck, which is made to suit the differential carrier_ There are two tube supports which are machined to slide along the frame and made to suit the torque tube or axle The forcing tool is of forged steel, and is shaped to accommodate the torque ball. The press can be operated by hand pumps or power pumps (either belt or motor driven) or by an hydraulic power
supply. It can, of course, be construoted to any special dimensions to suit individual needs.