Delivering the bread
Page 12
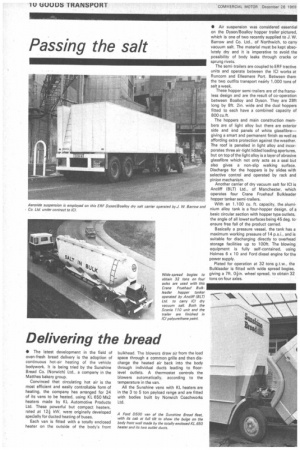
If you've noticed an error in this article please click here to report it so we can fix it.
• The latest development in the field of oven-fresh bread delivery is the adoption of continuous hot-air heating of the vehicle bodywork. It is being tried by the Sunshine Bread Co. (Norwich) Ltd., a company in the Matthes bakery group.
Convinced that circulating hot air is the most efficient and easily controllable form of heating, the company has arranged for 24 of its vans to be heated, using KL 650 Mk2 heaters made by KL Automotive Products Ltd. These powerful but compact heaters, rated at 124kW, were originally developed specially for ducted heating of buses.
Each van is fitted with a totally enclosed heater on the outside of the body's front bulkhead. The blowers draw air from the load space through a common grille and then discharge the heated air back into the body through individual ducts leading to floorlevel outlets. A thermostat controls the blowers automatically, according to the temperature in the van.
All the Sunshine vans with KL heaters are in the 3 to 5 ton payload range and are fitted with bodies built by Norwich Coachworks Ltd.
A Ford 0500 van of the Sunshine Bread fleet, with its cab at full tilt to show the bulge on the body front wall made by the totally enclosed KL. 650 heater and its two outlet ducts.
• Air suspension was considered essential on the Dyson/8°211°y hopper trailer pictured, which is one of two recently supplied to J. W.
Barrow and Co. Ltd., of Northwich, to carry vacuum salt. The material roust be kept abso lutely dry and it is imperative to avoid the possibility of body leaks through cracks or sprung rivets.
The semi-trailers are coupled to ER F tractive units and operate between the ICI works at Runcorn and Ellesmere Port. Between them the two outfits transport nearly 1,000 tons of salt a week.
These hopper semi-trailers are of the frameless design and are the result of co-operation between Boalloy and Dyson. They are 28ft long by 8ft. 2in wide and the dual hoppers fitted to each have a combined capacity of 800 cu.ft.
The hoppers and main construction members are of light alloy but there are exterior side and end panels of white glassfibre giving a smart and permanent finish as well as affording extra protection against the weather.
The roof is panelled in light alloy and incor porates three air-tight lidded loading apertures, but on top of the light alloy is a layer of abrasive glassfibre which not only acts as a seal but also gives a non-slip walking surface. Discharge for the hoppers is by slides with selective control and operated by rack and pinion mechanism.
Another carrier of dry vacuum salt for ICI is Ancliff (BLT) Ltd., of Manchester, which operates four Crane Fruehauf Bulkleader hopper tanker semi-trailers.
With an 1,100 Cu. ft. capacity, the aluminium alloy tank is a four-hopper design, of a basic circular section with hopper type outlets, the angle of all lower surfaces being 45 deg. to ensure free fall of the product carried.
Basically a pressure vessel, the tank has a maximum working pressure of 14 psi., and is suitable for discharging directly to overhead storage facilities up to 100ft. The blowing equipment is fully self-contained, using Holmes 6 x 10 and Ford diesel engine for the power supply.
Plated for operation at 32 tons g.t.w., the Bulkleader is fitted with wide spread bogies, giving a 7ft. Olin. wheel spread, to obtain 32 tons on four axles.