25 Years of Research
Page 61
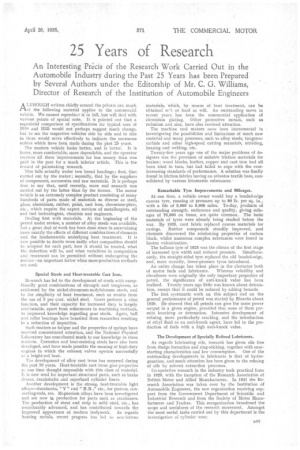
If you've noticed an error in this article please click here to report it so we can fix it.
An Interesting PrLis of the Research Work Carried Out in the Automobile Industry during the Past 25 Years has been Prepared by Several Authors under the Editorship of Mr. C. G., Williams, Director of Research of the Institution of Automobile Engineers
Pl A LTHOUGH written chiefly around the private car, much
of the following material applies to the commercial vehicle. We cannot reproduca it in full, but will deal with various points of special note. It is pointed out that a superficial comparison of specifications for typical cars of 191.0 and 1935 would not perhaps suggest much change, but to see the respective vehicles side by side and to ride in them would serve effectively to indicate the enormous strides which have been made during the Past 25 years.
The modern vehicle looks better, and is better. It is faster, more comfortable, more dependable, and the operator receives all these improvements for less money than was paid in the past for a much inferior article. This is the reward of painstaking research.
This falls actually under two broad headings: first, that carried out by the maker ; secondly, that by the suppliers of components, accessories and raw materials. It is perhaps true to say that, until recently, more real research was carried out by the latter than by the former. The motor vehicle is an extremely complex product consisting of many hundreds of parts made of materials as diverse as steel, glass, aluminium, rubber, paint, cast iron, chromium-plats, etc., which require the expert. services of metallurgists, oil and fuel technologists, chemists and engineers.
Dealing first with materials. At the beginning of the period under review, a number of alloy steels was available, but a great deal of work has been done since in ascertaining more exactly the effects of different combinations of elements and the fundamentals underlying heat treatment. It is now possible to decide more easily what composition should be adopted for each part, how it should be treated, what the distortion will be, and what variations in composition and treatment can be permitted without endangering the. service—an important factor when mass-production methods are used.
Special Steels and Heat-treatable Cast Iron.
Research has led to the development of steels with exceptionally good combinations of strength and toughness, as evidenced by the nickel-chromium-molybdenum steels, and to the simplicity of heat treatment, such as results from the use of 3 per cent, nickel steel. Gears perform a vital junction, and their capacity for increased duty is largely attributable, apart from refinements in machining methods, to improved knowledge regarding gear steels. Again, ball and roller bearings have benefited from researches resulting in a reduction of impurities.
Such matters as fatigue and the properties of springs have received concentrated attention, and the National Physical laboratory has contributed much to our knowledge in these matters. Corrosion and heat-resisting steels have also been developed, and have made possible the running of high-duty engines in which the exhaust valves operate successfully at a bright-red heat.
The development of alloy cast irons has occurred during the past 10 years. Heat-treatable cast irons give properties as one time thought impossible with this class of material. It is now used for important structural parts, such as brake drums, crankshafts and superhard cylinder liners.
Another development isthe strong, heat-treatable light alloys—duralurnin, " Y" and " R.R.," etc., for pistons, connecting-rods, etc. Magnesium alloys have been investigated and are now ist production for parts such as crankcases. The production of sheet and strip in mild steel, etc., has considerably advanced, and has contributed towards the improved appearance of modern bodywork. As regards bearing metals, recent progress has led to non-ferrous
materials, which, by means of heat treatment, can be obtained sn't or hard at will. An outstanding move in recent years has been the commercial application of chromium plating. Other protective metals, such as cadmium and zinc, have also received attention.
The machine tool makers nave been instrumental in investigating the possibilities and limitations of much new material and many processes, such as alloy steels, tungstencarbide and other high-speed cutting materials, nitriding, brazing and welding, etc.
Twenty-five years ago one of the major problems of designers Was the provision of suitable friction materials for brakes ; wood blocks, leather, copper and cast iron had all been tried in turn, but had failed to cope with the everincreasing standards of performance. A solution was finally found in friction fabrics having an asbestos textile base, consolidated by various bitumastic substances.'
Remarkable Tyre Improvements and Mileages.
At one time, a vehicle owner would buy a beaded-edge canvas tyre, running at pressures up to 80 lb. per sq. in., with a life of 3,000 to 5,000 miles. To-day, products of outstanding strength, endurance and quality, giving mileages of 70,000 on buses, are quite common. The basic materials of tyres were already being studied before the war. By 1920, cord fabric replaced canvas materials for casings. Rubber compounds steadily improved, and chemists discovered the reinforcing properties of carbon black, whilst numerous complex substances were found to hasten vulcanization.
The balloon tyre of 1923 was the climax of the first stage of increased tyre width and reduced pressure. Simultaneously, the straight-sided tyre replaced the old beaded-edge, and, more recently, lower-pressure tyres introduced.
An entire change has taken place in the character both of motor fuels and lubricants. Whereas volatility and cleanliness were originally the only important properties of petrol, the significance of anti-knock value has been realized. Twenty years ago little was known about detonation, except that it could be reduced by adding benzoic.
The first systematic work on this subject and on the general performance of petrol was started by Ricardo about 1929. He showed that all petrols can give the same power output in a given engine, provided that none of them permits knocking or detonation. Intensive development of refining, more particularly cracking, and the introduction of ethyl fluid as an anti-knock agent, have led -Lo the production of fuels with a high anti-knock value.
The Development of Specially Refined Lubricants.
As regards lubricating oils, research has given oils free from sludge formation and ring-sticking, together with easystarting characteristics and low consumption. One of the outstanding developments in lubricants is that of hydrogenation, and much attention has been given to the refining of oils by solvent extraction processes.
Co-operative research in the industry took practical form in 1920, with the inception of the Research Association of British Motor and Allied Manufacturers. In 1931 the Research Association was taken over by the Institution of Automobile Engineers, the new organization receiving support from the Government Department of Scientific and Industrial Research and from the Society of Motor Manufacturers and Traders. This reorganization broadened the scope and usefulness of the research movement. Amongst the most useful tasks carried out by this department is the investigation of cylinder wear.