PRICING OUT A WORKSHOP
Page 118
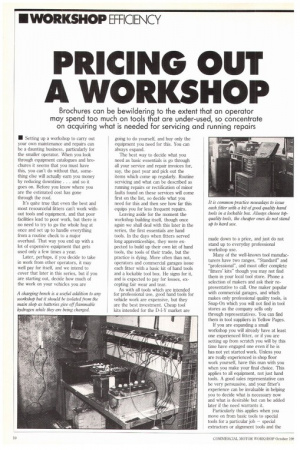
Page 119
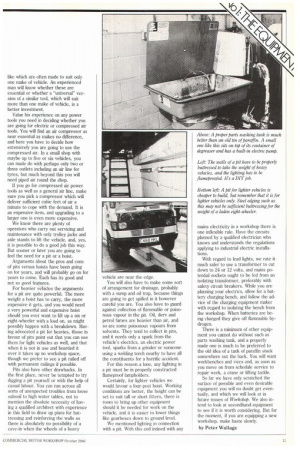
If you've noticed an error in this article please click here to report it so we can fix it.
Brochures can be bewildering to the extent that an operator may spend too much on took that are under-used, so concentrate on acquiring what is needed for servicing and running repairs
• Setting up a workshop to carry out your own maintenance and repairs can be a daunting business, particularly for the smaller operator. When you look through equipment catalogues and brochures it seems that you must have this, you can't do without that, something else will actually earn you money by reducing downtime . . . and so it goes on. Before you know where you are the estimated cost has gone through the roof.
It's quite true that even the best and most resourceful fitters can't work without tools and equipment, and that poor facilities lead to poor work, but there is no need to try to go the whole hog at once and set up to handle everything from a routine check to a major overhaul. That way you end up with a lot of expensive equipment that gets used only a few times a year.
Later, perhaps, if you decide to take in work from other operators, it may well pay for itself, and we intend to cover that later in this series, but if you are starting out, decide how much of the work on your vehicles you are going to do yourself, and buy only the equipment you need for this. You can always expand.
The best way to decide what you need as basic essentials is go through all your service and repair invoices for, say, the past year and pick out the items which come up regularly, Routine servicing and what can be described as running repairs or rectification of minor faults found on these services will come first on the list, so decide what you need for this and then see how far this equips you for less frequent repairs.
Leaving aside for the moment the workshop building itself, though once again we shall deal with this later in the series, the first essentials are hand tools. In the days when fitters served long apprenticeships, they were expected to build up their own kit of hand tools, the tools of their trade, but the practice is dying. More often than not, operators and commercial garages issue each fitter with a basic kit of hand tools and a lockable tool box. He signs for it, and is expected to pay for losses, excepting fair wear and tear.
As with all tools which are intended for professional use, good hand tools for vehicle work are expensive, but they are the best investment. Cheap tool kits intended for the D-I-Y market are made down to a price, and just do not stand up to everyday professional workshop use.
Many of the well-known tool manufacturers have two ranges, "Standard" and "professional", and most offer complete "fitters' kits" though you may not find them in your local tool store. Phone a selection of makers and ask their representative to call. One maker popular with commercial garages, and which makes only professional quality tools, is Snap-On which you will not find in tool stores as the company sells only through representatives. You can find them in toot suppliers in Yellow Pages, If you are expanding a small workshop you will already have at least one experienced fitter, or if you are setting up from scratch you will by this time have engaged one even if he is has not yet started work. Unless you are really experienced in shop floor work yourself, have this man with you when you make your final choice. This applies to all equipment, not just hand tools. A good sales representative can be very persuasive, and your fitter's experience can be invaluable in helping you to decide what is necessary now and what is desirable but can be added later if the need warrants it.
Particularly this applies when you move on from basic tools to special tools for a particular job — special extractors or alignment tools and the like which are often made to suit only one make of vehicle. An experienced man will know whether these are essential or whether a "universal" version of a similar tool, which will suit more than one make of vehicle, is a better investment.
Value his experience on any power tools you need in deciding whether you are going for electric or compressed air tools. You will find an air compressor as near essential as makes no difference, and here you have to decide how extensively you are going to use the compressed air. In a small shop with maybe up to five or six vehicles, you can made do with perhaps only two or three outlets including an air line for tyres, but much beyond this you will need piped air round the shop.
If you go for compressed air power tools as well as a general air line, make sure you pick a compressor which will deliver sufficient cubic feet of air a minute to cope with the demand. It is an expensive item, and upgrading to a larger one is even more expensive.
We know there are plenty of operators who carry out servicing and maintenance with only trolley jacks and axle stands to lift the vehicle, and, yes, it is possible to do a good job this way. But sooner or later you are going to feel the need for a pit or a hoist.
Arguments about the pros and cons of pits versus hoists have been going on for years, and will probably go on for years to come. Each has its good and not so good features.
For heavier vehicles the arguments for a pit are quite powerful. The more weight a hoist has to carry, the more expensive it gets, and you would need a very powerful and expensive hoist should you ever want to lift up a six or eight-wheeler with a load on, as might possibly happen with a breakdown. Having advocated a pit for heavies, those in favour of pits point out that you can use them for light vehicles as well, and that when it is not in use and boarded it over it takes up no workshop space, though we prefer to see a pit railed off with permanent railings if possible.
Pits also have other drawbacks. In the first place, never be tempted to try digging a pit yourself or with the help of casual labour. You can nui across all sorts of unexpected troubles from loose subsoil to high water tables, not to mention the absolute necessity of having a qualified architect with experience in this field to draw up plans for buttressing and reinforcing the walls so there is absolutely no possibility of a cave-in when the wheels of a heavy vehicle are near the edge.
You will also have to make some sort of arrangement for drainage, probably with a sump and oil trap, because things are going to get spilled in it however careful you are. You also have to guard against collection of flammable or poisonous vapour in the pit. Oil, dery and petrol fumes are heavier than air, and so are some poisonous vapours from solvents. They tend to collect in pits, and it needs only a spark from the vehicle's electrics, an electric power tool, sparks from a grinder or someone using a welding torch nearby to have all the constituents for a horrific accident.
For this reason a lone, any lighting in a pit must be in properly constructed flameproof lampholders.
Certainly, for lighter vehicles we would favour a four-post hoist. Working conditions are better, the height can be set to suit tall or short litters, there is room to bring up other equipment should it be needed for work on the vehicle, and it is easier to lower things like gearboxes down to ground level.
We mentioned lighting in connection with a pit. With this and indeed with any mains electricity in a workshop there is one inflexible rule. Have the circuits planned by a qualified electrician who knows and understands the regulations applying to industrial electric installations.
With regard to lead lights, we rate it much safer to use a transformer to cut down to 24 or 12 volts, and mains potential sockets ought to be fed from an isolating transformer, preferably with safety circuit breakers. While you are planning your electrics, allow for a battery charging bench, and follow the advice of the charging equipment maker with regard to isolating the bench from the workshop. When batteries are being charged they give off flammable hydrogen.
There is a minimum of other equipment you cannot do without such as parts washing tank, and a properly made one is much to be preferred to the old idea of a tank of paraffin stuck somewhere out the back. You will want workbenches and vices and, as soon as you move on from schedule service to repair work, a crane or lifting tackle.
So far we have only scratched the surface of possible and even desirable equipment you will no doubt get eventually, and which we will look at in future issues of Workshop. We also intend to look at secondhand equipment to see if it is worth considering_ But for the moment, if you are equipping a new workshop, make haste slowly.
by Peter Wallage