TRAFFIC CONTROL
Page 64
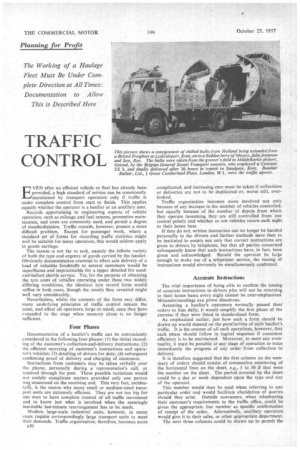
Page 67
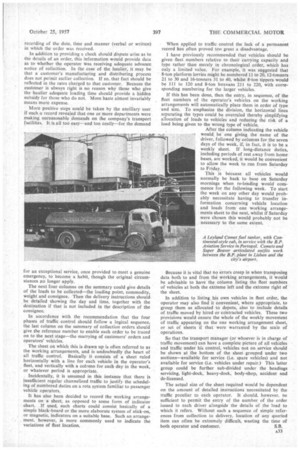
If you've noticed an error in this article please click here to report it so we can fix it.
EVEN after an efficient vehicle or fleet has already been provided, a high standard of service can be consistently maintained by transport operators only if traffic is under complete control from start to finish. This applies equally whether the operator is a haulier or an ancillary user.
Records appertaining to engineering aspects of vehicle operation, such as mileage and fuel returns, preventive maintenance, and costs are commonly used, and permit a degree of standardization. Traffic records, however, present a. more difficult problem. Except for passenger works where a standard set of forms for recording traffic statistics might well be suitable for many operators, this would seldom apply in goods carriage.
The reason is not far to seek, namely the infinite variety of both the type and urgency of goods carried by the haulier. Obviously documentation essential to effect safe delivery of a load of valuable foodstuffs to several customers would be superfluous and impracticable for a tipper detailed for sandand-ballast shuttle service. Yet, for the purpose of obtaining the tyre costs of vehicles operating under these two widely differing conditions, the identical tyre record form would suffice in both cases, though the results they revealed might well vary considerably.
Nevertheless, Whilst the contents of the form may differ, many underlying principles of traffic control remain the same, and affect all operators, large or small, once they have expanded to the stage when memory 'alone • is no longer sufficient.
Four Phases Documentation of a .haulier's traffic can be conveniently considered in the following four phases: (1) the initial recording of the customer's collection-and-delivery instructions; (2) the efficient marrying of customer's instructions and. operator's vehicles; (3) detailing of drivers for duty; (4) subsequent confirming proof of delivery and charging of customers.
Instructions from customers may be taken verbally over the phone, personally during a representative's call, or received through the post. These possible variations would not unduly complicate matters provided only one person wal concerned on the receiving end. This very fact, incidentally, is the reason why many small or medium-sized transport units are extremely efficient. They are not too big for one man to have complete control of all traffic movement and to know just what is involved when the seemingly inevitable last-minute rearrangement has to be made.
Modern large-scale industrial units, however, in many cases require correspondingly large transport units to meet their demands. Traffic organization, therefore, becomes more B30 complicated, and increasing care must be taken if collections or deliveries are not to be duplicated or, worse still, over looked. • Traffic organization becomes more involved not only because of any increase in the number of vehicles controlled. but equally because of the number of depots from which they operate (assuming they' are still controlled from one central point); and whether or not vehicles return each night to their home base.
If they do not, written instruction can no longer be handed personally to the drivers and further methods have then to be instituted to ensure not only that correct instructions are given to drivers by telephone, but that all parties concerned subsequently know that such instructions have, in fact, been given and acknowledged. Should the operator be large enough to make use of a teleprinter service, the issuing of instructions would obviously be simultaneously confirmed.
Accurate Instructions
The vital importance of being able to confirm the issuing of accurate instructions to drivers who will not be returning to their home bases every night cannot be over-emphasized. Misunderstandings can prove disastrous.
Assuming a haulier's customers normally passed their' orders to him daily, it would simplify the first phase of the exercise if they were listed in standardized form.
As emphasized earlier, just how such a form should be drawn up would depend on the peculiarities of each haulier's traffic. It is the essence of all such operations, however, that each phase should follow in logical sequence if consistent efficiency is to be maintained. Moreover, to meet any eventuality, it must be possible at any stage of operation to trace immediately the progress of any order from collection to delivery, It is therefore suggested that the first column on the summary of orders should consist of consecutive numbering of the horizontal lines on the sheet, e.g., I to 50 if that were the number on the sheet. The period covered by the sheet could be a day or week dependent upon the type and size of the operator.
This number would then be used when referring to any particular order and would facilitate elucidation of queries should they arise. Outside canvassers, when telephoning their customer's requirements to the traffic office, could be given the appropriate line number as specific confirmation of receipt of the order. Alternatively, ancillary operators would give it to their sales, or other appropriate department.
The next three columns could he drawn up to permit the
recording of the date, time and manner (verbal or written) in which the order was received.
In addition to providing a check should dispute arise as to the details of an order, this information would provide data as to whether the operator Was receiving adequate advance notice of collection. In the case of the haulier, it may be that a customer's manufacturing and distributing process does not permit earlier collection. If so, that fact should be reflected in the rates charged to that customer. Because the customer is always right is no reason why those who give the haulier adequate loading time should provide a hidden subsidy for those who do not. More haste almost invariably means more expense.
More positive steps could be taken by the ancillary user if such a record revealed that one or more departments were making unreasonable demands on the company's transport facilities. It is all too easy—and too costly—for the demand for an exceptional service, once provided to meet a genuine emergency, to become a habit, though the original circumstances no longer apply.
The next four columns on the summary could give details of the loads to be collected—the loading point, commodity, weight and consignee. Then the delivery instructions should. be detailed showing the day and time, together with the destination if that is not included in the description of the consignee.
In accordance with the recommendation that the four phases of traffic control should follow a logical sequence, the last column on the summary of collection orders should give the reference number to enable each order to be traced on to the next stage—the marrying of customers' orders and operators' vehicles.
The sheet on which this is drawn up is often referred to as the working arrangements, and is undoubtedly the heart of all traffic control. Basically it consists of a sheet ruled horizontally with a line for each vehicle in the operator's fleet, and vertically with a column for each day in the week, or whatever period is appropriate.
• Incidentally, it is assumed in this instance that there is insufficient regular channelized traffic to justify the scheduling of numbered duties on a rota system familiar to passenger vehicle operators.
It has also been decided to record the working arrangements on a sheet, as opposed to some form of indicator chart. If used, such charts could consist basically of a simple black-board or the more elaborate system of stick-on, or magnetic, indicators on a suitable base. Such an arrangement, however, is more commonly used to indicate the variations of fleet location.
When applied to traffic control the lack of a permanent record has often proved too great a disadvantage.
I have previously recommended that vehicles should be given fleet numbers relative to their carrying capacity and type rather than merely in chronological order, which has only a limited value. For example, it was suggested that 8-ton platform lorries might be numbered 11 to 20, 12-tonners 21 to 30 and 16-tonners 31 to 40, whilst 8-ton tippers would be Ill to 120 and 8-ton boxvans 211 to 220, with corresponding numbering for the larger vehicles.
If this has been done, then the entry, in sequence, of the feet numbers of the operator's vehicles on the working arrangements will automatically place them in order of type -and size. To emphasize the division, the horizontal lines separating the types could be overruled thereby simplifying allocation of loads to vehicles and reducing the risk of a load being given to the wrong type of vehicle.
After the column indicating the vehicle would, be one giving the name of the driver, followed by columns for the seven days of the week, if, in fact, it is to be a weekly sheet. If long-distance duties, including periods of rest away from home bases, are worked, it would be convenient to allow the week to run from Saturday to Friday.
This is because all vehicles would normally be back to base on Saturday mornings when re-loading would commence for the following week. To start the week on any other day would probably necessitate having to transfer information concerning vehicle location and loads from one working arrangements sheet to the next, whilst if Saturday were chosen this would probably not be necessary to the same extent.
Because it is vital that no errors creep in when transposing data both to and from the working arrangements, it would be advisable to have the column liking the fleet numbers of vehicles at both the extreme left and the extreme right of the sheet.
In addition to listing his own vehicles in fleet order, the operator may also find it convenient, where appropriate, to group them as allocated to depots, also to include details of traffic moved by hired or cOntracted vehicles. These two provisions would ensure the whole of the weekly movement of traffic appearing on the one working arrangement sheet, or set of sheets if that were warranted by the scale of operations.
So that the transport manager (or whoever is in charge of traffic movement) can have a complete picture of all vehicles and traffic under his control, vehicles not on service should be shown at the bottom of the sheet grouped under, two sections—available for service (i.e. spare vehicles) and not available for service (i.e. vehicles under repair.) This latter group could be further sub-divided under the headings servicing, light-dock, heavy-dock, body-shop, accident and de-licensed.
The actual size of the sheet required would be dependent on the amount of detailed instructions necessitated by the traffic peculiar to each operator. It should, however, be sufficient to permit the entry of the number of the order issued to each driver alongside the details of the load to which it refers. Without such a sequence of simple references from collection to delivery, location of any queried item can often he extremely difficult, wasting the time of both operator and customer. S.B.