WORKSHOP WAYS
Page 35
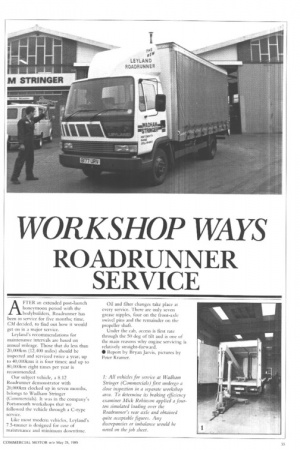
Page 36
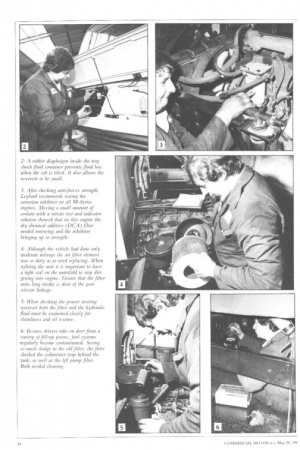
Page 37
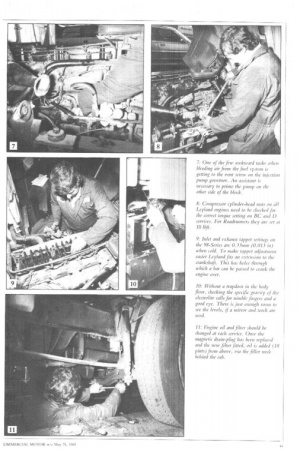
Page 38
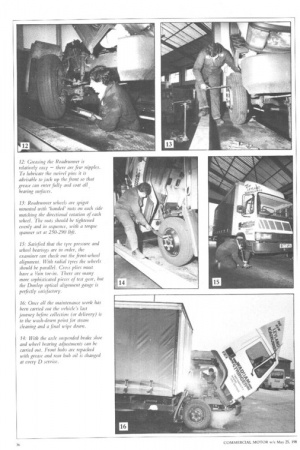
If you've noticed an error in this article please click here to report it so we can fix it.
ROADRUNNER SERVICE
AFTER an extended post-launch honeymoon period with the bodybuilders, Roadrunner has been in service for five months; time, CM decided, to find out how it would get on in a major service.
Leyland's recommendations for maintenance intervals are based on annual mileage. Those that do less than 20,000km (12,400 miles) should be inspected and serviced twice a year; up to 40,000kms it is four times; and up to 80,000km eight times per year is recommended.
Our subject vehicle, a 8.12 Roadrunner demonstrator with 20,000km clocked up in seven months, belongs to Wadharn Stringer (Commercials). It was in the company's Portsmouth workshops that we followed the vehicle through a C-type service.
Like most modern vehicles, Leyland's 7.5-tonner is designed for ease of maintenance and minimum downtime. Oil and filter changes take place at every service. There are only seven grease nipples, four on the front-axle swivel pins and the remainder on the propeller shaft.
Under the cab, access is first rate through the 50 deg of tilt and is one of the main reasons why engine servicing is relatively straight-forward.
• Report by Bryan Jarvis, pictures by Peter Kramer.
1: Al! vehicles for service at Wadham Stringer (Commercials) first undergo a close inspection in a separate workshop area. To determine its braking efficiency examiner Mick Robinson applied a fourton simulated loading over the Roadrunner's rear axle and obtained quite acceptable figures. Any discrepancies or imbalance would he noted on the job sheet. 2: A rubber diaphragm inside the tiny clutch fluid container prevents _fluid loss when the cab is tilted, it also allows the reservoir to he small.
3: After checking anti-freeze strength, Leyland recommends testing the corrosion inhibiter on all 98-Series engines. Mixing a .small amount of coolant with a nitrate test and indicator solution showed that on this engine the dry chemical additive (DCA) Iter needed renewing and the inhibitor bringing up to strength.
4: Although the vehicle had done only moderate mileage the air filter element was so dirty as .to need replacing. When refitting the unit it is important to have a tight seal on the manifold to stop dirt getting into engine. Ensure that the filter units long intake is dear of the gear selector linkage.
5: When checking the power steering reservoir both the filter and the hydraulic fluid must be examined closely for cleanliness and oil texture.
6: Because drivers take on dery from a variety of fill-up points, fuel systems -regularly become contaminated. Seeing so much sludge in the old filter, the Jitter checked the sedimenter trap behind the tank, as well as the lift pump _filter. Both needed cleaning. 7: One of the few awkward tasks when bleeding air from thelu.' el system is getting to the vent screw on the injection pump governor. An assistant is necessary to prime the pump on the other side of the block.
8: Compressor cylinder-head nuts on all Leyland engines need to be checked for the correct torque setting on BC and D services. For Roadrunners they are set at -10 lbft.
9: Inlet and exhaust tappet settings on the 98-Series are 0.33min (0.01.3 in) when cold. To make tappet aditistmem easier Leyland fits an extension to the crankshaft. This has holes through which a bar can be passed to crank the engine over.
10: Without a trapdoor in the body floor, checking the specific gravity of the electrolite calls for nimble fingers and a good eye. There is just enough room to see the levels, if a mirror and torch are used.
11: Engine oil antifilter should be changed at each service. Once the magnetic drain-ply has been replaced and the new filter fitted, oil is added (18 pints)frorn above, via the _filler neck behind the cab. 12: Greasing the Roadrunner is relatively easy — there are few nipples. To lubricate the swivel pins it is advisable to jack up the front so that grease can enter Jully and coat all bearing surfaces.
13: Roadrunner wheels are spigot • mounted with 'handed' nuts on each side Fnatching the directional rotation of each wheel. The nuts should be tightened evenly and in sequence, with a torque spanner set at 2.50-290 15: Satisfied that the tyre pressure and wheel bearings are in order, the examiner can check out the front-wheel alignment. With radial tyres the wheels should he parallel. Cross plies must have a '/sin toe-in. There are many more sophisticated pieces of test gear, but the Dunlop optical alignment gauge is perfectly satisfactory.
16: Once all the maintenance work has been carried out the vehicle's last journey before collection (or delivery) is to the wash-down point /or steam cleaning and a final wipe down.
.14: With the axle suspended brake shoe and wheel bearing adjustments can be carried out. Front hubs are repacked with grease and rear hub oil is changed at every D service.