Never neglect jaws
Page 94
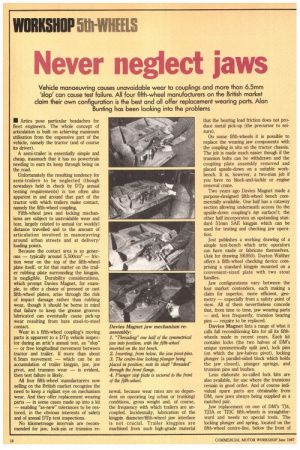
If you've noticed an error in this article please click here to report it so we can fix it.
Vehicle manoeuvring causes unavoidable wear to couplings and more than 6.5mm 'slop' can cause test failure. All four fifth-wheel manufacturers on the British market claim their own configuration is the best and all offer replacement wearing parts. Alan Bunting has been looking into the problems • Artics pose particular headaches for fleet engineers. The whole concept of articulation is built on achieving maximum utilisation from the expensive part of the vehicle, namely the tractor (and of course its driver).
A semi-trailer is essentially simple and cheap, inasmuch that it has no powertrain needing to earn its keep through being on the road.
Unfortunately the resulting tendency for semi-trailers to be neglected (though nowadays held in check by DTp annual testing requirements) is too often also apparent in and around that part of the tractor with which trailers make contact, namely the fifth-wheel coupling.
Fifth-wheel jaws and locking mechanisms are subject to unavoidable wear and tear, largely related to annual (or weekly) distance travelled and to the amount of articulation involved in manoeuvring around urban streets and at delivery/ loading points.
Because the contact area is so generous — typically around 5,500cm2 — friction wear on the top of the fifth-wheel plate itself, or for that matter on the trailer rubbing plate surrounding the kingpin, is negligible. Durability considerations, which prompt Davies Magnet, for example, to offer a choice of pressed or cast fifth-wheel plates, arise through the risk of impact damage rather than rubbing wear, though it should be borne hi mind that failure to keep the grease grooves lubricated can eventually cause pick-up wear resulting from bare steel-to-steel contact.
Wear in a fifth-wheel coupling's moving parts is apparent to a DTp vehicle inspector during an artic's annual test, as "slop" — or free longitudinal movement between tractor and trailer. If more than about 6.5mm movement — which can be an accumulation of trailer kingpin, jaw, jaw pivot, and trunnion wear — is evident, then test failure is likely.
All four fifth-wheel manufacturers now selling on the British market recognise the need to keep a vigilant eye on mechanism wear. And they offer replacement wearing parts — in some cases made up into a kit — enabling "as-new" tolerances to be restored, in the obvious interests of safety and of annual DTp test inspections.
No kilometreage intervals are recommended for jaw, lock-pin or trunnion re newal, because wear rates are so dependent on operating (eg urban or trunking) conditions, gross weight and, of course, the frequency with which trailers are uncoupled. Incidentally, lubrication of the kingpin diameter/fifth-wheel jaw interface is not crucial. Trailer kingpins are machined from such high-grade material that the bearing load friction does not produce metal pick-up (the precursor to seizure).
On some fifth-wheels it is possible to replace the wearing jaw components with the coupling in situ on the tractor chassis. The job is made much easier though if the trunnion bolts can be withdrawn and the coupling plate assembly removed and placed upside-down on a suitable workbench. It is, however, a two-man job if you have no block-and-tackle or engine removal crane.
Two years ago Davies Magnet made a purpose-designed fifth-wheel bench commercially available. One half has a cutaway section allowing underneath access (to the upside-down coupling's top surface!); the other half incorporates an upstanding standard 51rnm SAE kingpin which can be used for testing and checking jaw operation.
Jost publishes a working drawing of a simple test-bench which artic operators can have made or fabricate themselves. (Ask for drawing SK950). Dayton Walther offers a fifth-wheel checking device comprising a standard kingpin mounted on a convenient-sized plate with two stout handles.
Jaw configurations vary between the four market contenders, each making a claim for superior, more efficient, geometry — especially from a safety point of view. All of them nevertheless concede that, from time to time, jaw wearing parts — and, less frequently, trunnion bearing pins — require to be replaced.
Davies Magnet lists a range of what it calls full reconditioning kits for all its fifthwheels made in recent years. Each kit contains locks (the two halves of DM's unique symmetrically split jaw), lock pins (on which the jaw-halves pivot), locking plunger (a parallel-sided block which holds the jaw closed), plunger springs, and trunnion pins and bushes.
Less elaborate so-called lock kits are also available, for use where the trunnions remain in good order. And of course individual spare parts are obtainable from DM, new jaws always being supplied as a matched pair.
Jaw replacement on one of DM's TJ4, TJ3A or TJ3C fifth-wheels is straightforward and needs no special tools. The locking plunger and spring, located on the fifth-wheel centre-line, below the front of