DIY recon contribute
Page 28
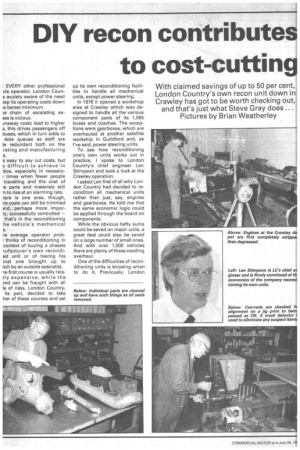
Page 29
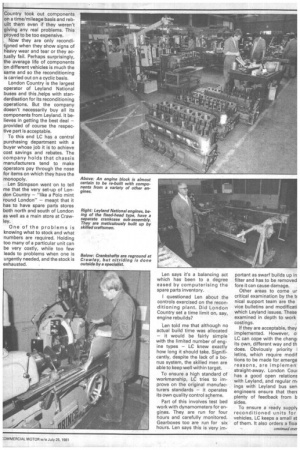
Page 30
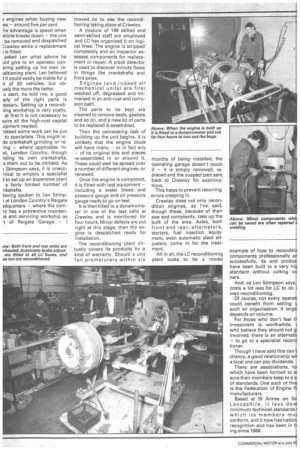
If you've noticed an error in this article please click here to report it so we can fix it.
to cost-cut-tin
With claimed savings of up to 50 per cent, London Country's own recon unit down in Crawley has got to be worth checking out, and that's just what Steve Gray does ...
Pictures by Brian Weatherley
EVERY other professional cle operator, London Couns acutely aware of the need 3ep its operating costs down le barest minimum.
le chain of escalating ex3es is vicious.
inaway costs lead to higher s, this drives passengers off buses, which in turn adds to dole queues as staff are le redundant both on the rating and manufacturing S.
s easy to say cut costs, but y difficult to achieve in Aim especially in recessioe times when fewer people travelling and the cost of -e parts and materials still n to rise at an alarming rate. lere is one area, though, !re costs can still be trimmed Ind, perhaps more imporly, successfully controlled — that's in the reconditioning he vehicle's mechanical S.
ie average operator probr thinks of reconditioning in context of buying a chassis lufacturer's own recondied unit or of having his inal one brought up to itch by an outside specialist. le first course is usually relafly expensive, while the )nd can be fraught with all Is of risks. London Country, its part, decided to take her of these courses and set
up its own reconditioning facilities to handle all mechanical units, except power steering.
In 1976 it opened a workshop area at Crawley which was designed to handle all the various component parts of its 1,065 buses and coaches. The exceptions were gearboxes, which are overhauled at another satellite workship in Guildford and, as I've said, power steering units.
To see how reconditioning one's own units works out in practice, I spoke to London Country's chief engineer Len Stimpson and took a look at the Crawley operation.
I asked Len first of all why London Country had decided to recondition all mechanical units rather than just, say, engines and gearboxes. He told me that the same economic logic could be applied through the board on components.
While the obvious hefty sums could be saved on major units, a great deal could also be saved on a large number of small ones. And with over 1,000 vehicles there are plenty of these needing overhaul.
One of the difficulties of reconditioning units is knowing when to do it. Previously, London Country took out components on a time/mileage basis and rebuilt them even if they weren't giving any real problems. This proved to be too expensive.
Now they are only reconditipned when they show signs of heavy wear and tear or they actually fail. Perhaps surprisingly, the average life of components on different vehicles is much the same and so the reconditioning is carried out on a cyclic basis.
London Country is the largest operator of Leyland National buses and this helps with standardisation for its reconditioning operations. But the company doesn't necessarily buy all its components from Leyland. It believes in getting the best deal — provided of course the respective part is acceptable.
To this end LC has a central purchasing department with a buyer whose job it is to achieve cost savings and rebates. The company holds that chassis manufacturers tend to make operators pay through the nose for items on which they have the monopoly.
Len Stimpson went on to tell me that the very set-up of London Country — "like a Polo mint round London" — meaht that it has to have spare parts stores both north and south of London as well as a main store at Crawley.
One of the problems is knowing what to stock and what numbers are required. Holding too many of a particular unit can be very costly, while too few leads to problems when one is urgently needed, and the stock is exhausted. Len says it's a balancing act which has been to a degree eased by computerising the spare parts inventory.
I questioned Len about the controls exercised on the reconditioning plant. Did London Country set a time limit on, say, engine rebuilds?
Len told me that although no actual build time was allocated — it would be fairly simple• with the limited number of engine types — LC knew exactly how long it should take. Significantly, despite the lack of a bonus system, the skilled men are able to keep well within target.
To ensure a high standard of workmanship, LC tries to improve on the original manufacturers standards — it operates its own quality control scheme.
Part of this involves test bed work with dynamometers for engines. They are run for four hours and carefully monitored. Gearboxes too are run for six hours. Len says this is very im
portant as swarf builds up in filter and has to be removed fore it can cause damage.
Other areas to come ur critical examination by the tE nical support team are the vice bulletins and modificati which Leyland issues. These examined in depth to work costings.
If they are acceptable, they implemented. However, a LC can cope with the changi its own, different way and th does. Obviously priority I letins, which require modif tions to be made for emerge reasons, are implemen straight-away. London Cow has a good open relations with Leyland, and regular ml ings with Leyland bus sell engineers ensure that therE plenty of feedback from b sides.
To ensure a ready supply reconditioned units for vehicles, LC keeps a small st of them. It also orders a floa v engines when buying new .es — around five per cent.
he advantage is speed when .ihicle breaks down — the unit be removed and despatched 2,rawley while a replacement is fitted.
asked Len what advice he uld give to an operator conaring setting up his own reiditioning plant, Len believed t it could easily be viable for a A of 50 vehicles, but obusly the more the better.
'o start, he told me, a good iply of the right parts is :essary. Setting up a recondiling workshop is very costly, at first it is not necessary to iuire all the high-cost capital Jipment needed.
ristead some work can be put to specialists. This might inde crankshaft grinding or re
ing where applicable. In)cl, London Country, though riding its own crankshafts, :s them out to be nitrided. As Stimpson says, it is unecorical to employ a specialist Ito set up an expensive plant a fairly limited number of nkshafts.
laving spoken to Len Stimpat London Country's Reigate 5clquarters — where the cornly has a preventive mainten:.e and servicing workship as rt of Reigate Garage L I
moved on to see the reconditioning taking place at Crawley.
A mixture of 148 skilled and semi-skilled staff are employed and LC has organised it on logical lines. The engine is stripped completely and an inspector assesses components for replacement or repair. A crack detector is used to discover minute flaws in things like crankshafts and front axles.
Engines (and indeed all mechanical units) are first washed off, degreased and immersed in an anti-rust and corrosion bath.
The parts to be kept are cleaned to remove seals, gaskets and so on, and a new kit of parts to be replaced is assembled.
Then the painstaking task of building up the unit begins. It is unlikely that the engine block will have many — or in fact any — of its original bits and pieces re-assembled in or around it. These could well be spread over a number of different engines, or renewed.
Once the engine is completed, it is fitted with test equipment — including a water bleed and pressure gauge and oil pressure gauge ready to go on test.
It is then fitted to a dynamometer in one of the test cells at Crawley and is monitored for four hours. Minor defects are put right at this stage, then the engine is despatched ready for installation.
The reconditioning plant virtually covers its products by a kind of warranty. Should a unit fail prematurely within six
months of being installed, the operating garage doesn't touch it — it is simply removed, replaced and the suspect part sent back to Crawley for examinations.
This helps to prevent recurring errors creeping in.
Crawley does not only recondition engines, as I've said, though these, because of their size and complexity, take up the bulk of the area. Axles, both front and rear, alternators, starters, fuel injection equipment, even automatic slack adjusters, come in for the treatment.
All in all, the LC reconditioning plant looks to be a model example of how to recenditic components professionally ail successfully. Its end produa have been built to a very hig standard without cutting c0 ners.
And, as Len Stimpson says costs a lot less for LC to do I own reconditioning.
Of course, not every operatc could benefit from setting u such an organisation. It large depends on volume.
For those who don't feel 1 investment is worthwhile, who believe they should not di involved, there is an alternatit — to go to a specialist reconcl tioner.
Though I have said this can t chancy, a good relationship wit a local one can pay dividends.
There are associations, tall which have been formed to 4,1 sure their members keep to a di of standards. One such of thee is the Federation of Engine RI manufacturers.
Based at St Annes on Se Lancashire, it lays dow minimum technical standards which its members mu!: conform, and it now has natiori recognition and has been in bi ing since 1968.