16.5M ARTICS
Page 42
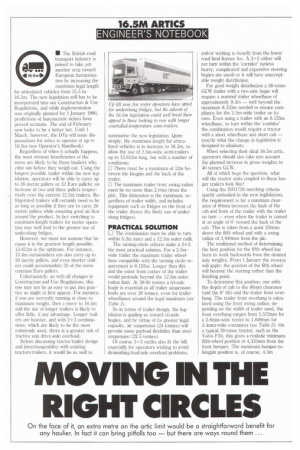
Page 43
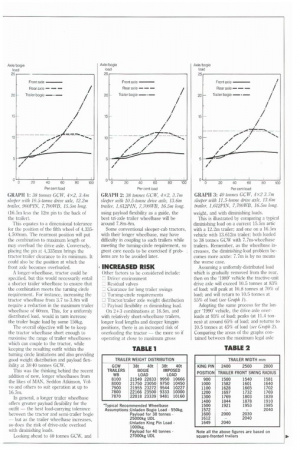
Page 44
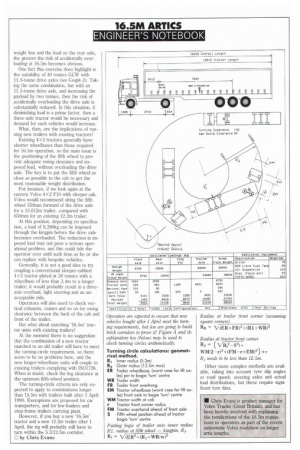
If you've noticed an error in this article please click here to report it so we can fix it.
ENGINEER'S NOTEBOOK
• The British road transport industry is poised to take yet another step toward European harmonisation by increasing the maximum legal length for articulated vehicles from 15.5 to 16.5m. The new legislation still has to be incorporated into our Construction & Use Regulations, and while implementation was originally planned for 1 January 1990, predictions of bureaucratic delays have proved accurate. The end of February now looks to be a better bet. Until 1 March, however, the DTp will issue dispensations for artics to operate at up to 16.5m (see Operator's Handbook).
Regardless of when it actually happens, the most obvious beneficiaries of the move are likely to be those hauliers who cube out before they weigh out. Using the longest possible trailer within the new legislation, operators will be able to carry up to 26 metric pallets or 33 Euro pallets: an increase of two and three pallets respectively over the current 12.2m trailers. Refrigerated trailers will certainly need to be as long as possible if they are to carry 26 metric pallets while ensuring good air flow around the product. In fact switching to maximum-length trailers for reefer operation may well lead to the greater use of underslung fridges.
However, we must not assume that because it is the greatest length possible, 13.612m is the optimum. For instance, 13.4m curtainsiders can also carry up to 26 metric pallets, and even shorter trailers could accommodate 32 of the more common Euro pallets.
Unfortunately, as with all changes in Construction and Use Regulations, this one may not be as easy to put into practice as might at first appear. For instance, if you are currently running at close to maximum weight, then a move to 16.5m and the use of longer trailers is likely to offer little, if any advantage. Longer trailers are heavier, and with 2+3 combinations, which are likely to be the most commonly used, there is a greater risk of tractive unit drive-axle overload.
Before discussing tractor/trailer design and interchangeability with existing tractors/trailers, it would be as well to summarise the new legislation. Quite simply, the maximum length for articulated vehicles is to increase to 16.5m, to allow the use of 2.5m-wide semi-trailers up to 13.612m long, but with a number of conditions:
0 There must be a maximum of 12m between the kingpin and the back of the trailer.
The maximum trailer front swing radius must be no more than 2.04m (from the pin). This dimension is the maximum, regardless of trailer width, and includes equipment such as fridges on the front of the trailer (hence the likely use of underslung fridges).
Li The combination must be able to turn within 5.3m inner and a 12.5m outer radii.
The turning-circle criteria make a 2+3 the most practical solution. For a 2.5mwide trailer the maximum trailer wheelbase compatible with the turning circle requirement is 8.155in. Longer than this and the outer front corner of the trailer would protrude beyond the 12.5m outer radius limit. At 38/40 tonnes a tri-axle bogie is essential as all trailer suspension loads are over 20 tonnes, even for trailer wheelbases around the legal maximum (see Table 1).
So in terms of trailer design, the legislation is guiding us toward tri-axle bogies, and by virtue of its greater legal capacity, air suspension (24 tonnes) will provide more payload flexibility than steel suspension (22.5 tonnes).
Of course 3+3 outfits also fit the bill, especially for operators wishing to avoid diminishing-load/axle-overload problems, and/or wishing to benefit from the lower road fund licence fee. A 3+2 either will not turn within the 'corridor' (unless heavy, complicated and expensive steering bogies are used) or it will have unacceptable weight distribution.
For good weight distribution a 38-tonne GCW trailer with a two-axle bogie will require a nominal trailer wheelbase of approximately 9.3m — well beyond the maximum 8.155m needed to ensure compliance for the 2.5m-wide trailer on its own. Even using a trailer with an 8.155m wheelbase, to turn within the 'corridor' the combination would require a tractor with a short wheelbase and short cab — exactly what the change in legislation is designed to eliminate.
When selecting their ideal 16.5m artic, operators should also take into account the planned increase in gross weights to 40 tonnes GCW.
All of which begs the question, what will the tractor units coupled to these longer trailers look like?
Using the IS01726 matching criteria (partly embodied in the new leglislation), the requirement is for a minimum clearance of 80mm between the back of the cab and front of the trailer with the trailer on turn — even when the trailer is canted at an angle of 6 toward the back of the cab. This is taken from a point 250mm above the fifth wheel and with a swing radius of 2,040mm from the pin.
The traditional method of determining the best position for the fifth wheel has been to work backwards from the desired axle weights. From 1 January the reverse will apply: the position of the fifth wheel will become the starting rather than the finishing point.
To determine this position, one adds the depth of cab to the 80rnm clearance (and the 6° tilt) and the trailer front overhang. The trailer front overhang is calculated using the front swing radius; depending on the width of trailer used, the front overhang ranges from 1,572mm for a 2.6mm-wide reefer to 1,649mm for 2.4mrn-wide containers (see Table 2). On a typical 38-tonne tractor, such as the Volvo 1710, this gives a realistic minimum fifth-wheel position of 4,335mm from the front bumper. The maximum bumper-tokingpin position is, of course, 4.5m
GRAPH I: 38 tonnes GCW, 4x2, 3.4m sleeper with 10.5-tonne drive axle, 12.2m trailer, 90011N, 7,700WB, 15.5.m long.
(16.5m less the 12m pin to the back of the trailer).
This equates to a dimensional tolerance for the position of the fifth wheel of 4,3354,300mm. The rearmost position will put the combination to maximum length or may overload the drive axle. Conversely, placing the pin at 4,335mm brings the tractoritrailer clearance to its minimum. It could also be the position at which the front axle becomes overloaded.
A longer-wheelbase, tractor could be specified, but this would necessarily entail a shorter trailer wheelbase to ensure that the combination meets the turning circle requirement. For instance, increasing the tractor wheelbase from 3.7 to 3.8m will require a reduction in the maximum trailer wheelbase of 60mm. This, for a uniformly distributed load, would in turn increase the trailer bogie load by some 150kg.
The overall objective will be to keep the tractor wheelbase short enough to maximise the range of trailer wheelbases which can couple to the tractor, while keeping the resulting outfit within the turning circle limitations and also providing good weight distribution and payload flexibility at 38/40 tonnes GCW.
This was the thinking behind the recent addition of new, longer wheelbases from the likes of MAN, Seddon Atkinson, Volvo and others to suit operation at up to 16.3m.
In general, a longer trailer wheelbase offers greater payload flexibility for the outfit the best load-carrying tolerance between the tractor and semi-trailer bogie but as the trailer wheelbase increases, so does the risk of drive-axle overload with diminishing loads.
Looking ahead to 40 tonnes GCW, and GRAPH 2: 38 tonnes GOV, 4x2, 3.7m sleeper with 10.5-tonne drive axle, 13.6m trailer, 1,612PIN, 7,700WB, 16.5m long.
using payload flexibility as a guide, the best tri-axle trailer wheelbase will be around 7.8m-8m.
Some conventional sleeper-cab tractors, with their longer wheelbase, may have difficulty in coupling to such trailers while meeting the turning-circle requirement, so great care needs to be exercised if problems are to be avoided later.
DI her actors to be considered include: . Driver environment L Residual valves
Clearance for long trailer swings LI Turning-circle requirements Tractor/trailer axle weight distribution U Payload flexibility us diminishing load. On 2+3 combinations at 16.5m, and with relatively short-wheelbase trailers, longer load lengths and deeper kingpin positions, there is an increased risk of overloading the tractor the more so if operating at close to maximum gross
Per cent load GRAPH 3: 40 tonnes GCW, 4x2 3.7m sleeper with 11,5-tonne drive axle, 13.6in trailer, 1,612P1N, 7,700WB, 16.5m long.
weight, and with diminishing loads.
This is illustrated by comparing a typical diminishing load on a current 15.5m artic with a 12.2m trailer; and one on a 16.5m vehicle with 13.612m trailer; both loaded to 38 tonnes GCW with 7.7m-wheelbase trailers. Remember, as the wheelbase increases, the diminishing-load problem becomes more acute: 7.7m is by no means the worse case.
Assuming a uniformly-distributed load which is gradually removed from the rear, then on the '1989' vehicle the tractive-unit drive axle will exceed 10.5 tonnes at 83% of load; will peak at 10.8 tonnes at 70% of load; and will return to 10.5 tonnes at 55% of load (see Graph 1).
Adopting the same process for the longer '1990' vehicle, the drive axle overloads at 93% of load; peaks (at 11.4 tonnes) at around 65% of load; and returns to 10.5 tonnes at 45% of load (see Graph 2). Comparing the areas of the graphs contained between the maximum legal axle weight line and the load on the rear axle, the greater the risk of accidentally overloading at 16.5m becomes obvious.
One fact this exercise does highlight is the suitability of 40 tonnes GCW with 11.5-tonne drive axles (see Graph 3). Taking the same combination, but with an 11.5-tonne drive axle, and increasing the payload by two tonnes, then the risk of accidentally overloading the drive axle is substantially reduced. In this situation, if diminishing load is a prime factor, then a three-axle tractor would be necessary and demand for such vehicles would increase.
What, then, are the implications of running new trailers with existing tractors?
Existing 4 x 2 tractors generally have shorter wheelbases than those required for 16.5m operation, so the main issue is the positioning of the fifth wheel to provide adequate swing clearance and imposed load, without overloading the drive axle, The key is to put the fifth wheel as close as possible to the cab to get the most reasonable weight distribution, For instance, if we look again at the current Volvo 4x2 F10 with sleeper-cab, Volvo would recommend siting the fifth wheel 350mm forward of the drive axle for a 13.612m trailer, compared with 650mm for an existing 12.2m trailer.
At this position, depending on specification, a load of 9,290kg can be imposed through the kingpin before the drive axle becomes overloaded. The reduction in imposed load may not pose a serious operational problem, and this could tide the operator over until such time as he or she can replace with bespoke vehicles.
Generally, it is not a good idea to try coupling a conventional sleeper-cabbed 4 x 2 tractor plated at 38 tonnes with a wheelbase of less than 3.4m to a longer trailer; it would probably result in a driveaxle overload, light steering and an unacceptable ride.
Operators will also need to check vertical exhausts, cranes and so on for swing clearance between the back of the cab and front of the trailer.
But what about matching '16,5m' tractor units with existing trailers?
At the moment there is no suggestion that the combination of a new tractor matched to an old trailer will have to meet the turning-circle requirement, so there seem to be no problems here, and the new longer-wheelbase units will couple to existing trailers complying with ISO1726. When in doubt, check the leg clearance at the optimum fifth-wheel position.
The turning-circle criteria are only expected to apply to combinations longer than 15.5m with trailers built after 1 April 1990. Exemptions are proposed for car transporters, and for low-loaders and step-frame trailers carrying plant.
However, if you buy a new `16.5m' tractor and a new 12.2m trailer after 1 April, the rig will probably still have to turn within the 5.3/12.5m corridor.
by Chris Evans Operators are expected to ensure that new vehicles bought after 1 April meet the turning requirements, but few are going to build brick corridors to prove it! Figure A and its explanatory key (below) may be used to check turning circles arithmetically.