Moving: the hardest job you'll tackle
Page 110
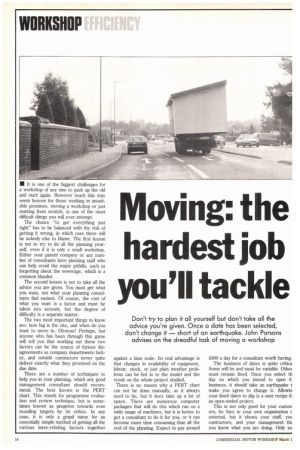
Page 111
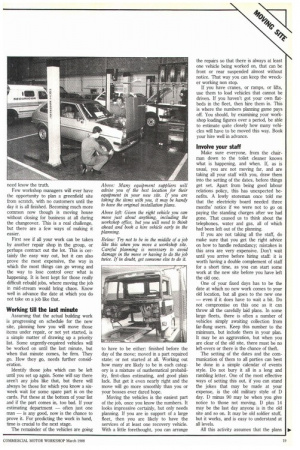
Page 112
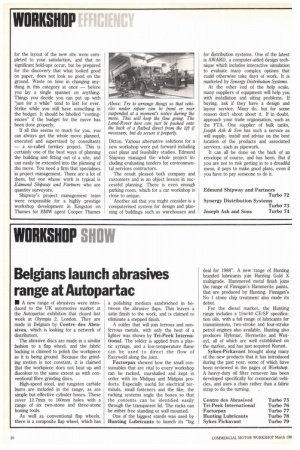
If you've noticed an error in this article please click here to report it so we can fix it.
Don't try to plan it all yourself but don't take all the advice you're given. Once a date has been selected, don't change it — short of an earthquake. John Parsons advises on the dreadful task of moving a workshop
• It is one of the biggest challenges for a workshop of any size to pack up the old and start again. However much this may seem heaven for those working in unsuitable premises, moving a workshop or just starting from scratch, is one of the most difficult things you will ever attempt.
The chance to get everything just right" has to be balanced with the risk of getting it wrong, in which case there will be nobody else to blame. The first lesson is not to try to do all the planning yourself, even if it is only a small workshop. Either your parent company or any number of consultants have planning staff who can help avoid the major pitfalls, such as forgetting about the sewerage, which is a common blunder.
The second lesson is not to take all the advice you are given. You must get what you want, not what your planning consultants find easiest. Of course, the cost of what you want is a factor and must be taken into account, but the degree of difficulty is a separate matter.
The two most important things to know are: how big is the site, and when do you want to move in. Obvious? Perhaps, but anyone who has been through this game will tell you that working out these two factors can be the source of furious disagreements as company departments bicker, and outside contractors never quite deliver exactly what they promised on the due date.
There are a number of techniques to help you in your planning, which any good management consultant should recommend. The best known is the PERT chart. This stands for programme evaluation and review technique, but is sometimes known as progress towards ever receding targets by its critics. In any case, it is only a grand name for an essentially simple method of getting all the various inter-relating factors together against a time scale. Its real advantage is that changes in availability of equipment, labour, stock, or just plain weather problems can be fed in to the model and the result on the whole project studied.
There is no reason why a PERT chart can not be done manually, as it always used to be, but it does take up a lot of space. There are numerous computer packages that will do this which run on a wide range of machines, but it is better to get a consultant to do it for you, or it can become more time consuming than all the rest of the planning. Expect to pay around £400 a day for a consultant worth having.
The business of dates is quite critica Some will be and must be variable. Other must remain fixed. Once you select th day on which you intend to open fc business, it should take an earthquake t make you agree to change it. Allowin your fixed dates to slip is a sure recipe fc an open-ended project.
This is not only good for your custorr ers, be they in your own organisation c external, but it shows your staff, you contractors, and your management tin you know what you are doing. Only yo need know the truth.
Few workshop managers will ever have the opportunity to plan a greenfield site from scratch, with no customers until the day it is all finished. Becoming much more common now though is moving house without dosing for business at all during the changeover. This is a real challenge, but there are a few ways of making it easier, First see if all your work can be taken by another repair shop in the group, or perhaps contract out the lot. This is certainly the easy way out, but it can also prove the most expensive, the way in which the most things can go wrong and the way to lose control over what is happening. It is best kept for those really difficult rebuild jobs, where moving the job in mid-stream would bring chaos. Know well in advance the date at which you do not take on a job like that.
Working till the last minute
Assuming that the actual building work is progressing on schedule for the new site, planning how you will move those items under repair, or not yet started, is a simple matter of drawing up a priority list. Some urgently-required vehicles will be worked on until the last minute, but when that minute comes, be firm. They go. How they go, needs further consideration, Identify those jobs which can be left until you set up again. Some will say there aren't any jobs like that, but there will always be those for which you know a sixweek wait for some spare part is on the cards. Put these at the bottom of your list and if the part comes in, too bad. If your estimating department — often just one man — is any good, now is the chance to prove it. For predicting the work in hand, time is crucial to the next stage.
The remainder of the vehicles are going to have to be either: finished before the day of the move; moved in a part repaired state; or not started at all. Working out how many are likely to be in each category is a mixture of mathematical probability, first-class estimating, and good plain luck. But get it even nearly right and the move will go more smoothly than you or your bosses ever dared hope.
Moving the vehicles is the easiest part of the job, once you know the numbers. It looks impressive certainly, but only needs planning. If you are in support of a large fleet, then you are likely to have the services of at least one recovery vehicle. With a little forethought, you can arrange the repairs so that there is always at least one vehicle being worked on, that can be front or rear suspended almost without notice. That way you can keep the wrecker working non stop.
If you have cranes, or ramps, or lifts, use them to load vehicles that cannot be driven. If you haven't got your own flatbeds in the fleet, then hire them in. This is where the numbers planning game pays off. You should, by examining your workshop loading figures over a period, be able to estimate quite closely how many vehicles will have to be moved this way. Book your hire well in advance.
Involve your staff
Make sure everyone, from the chairman down to the toilet cleaner knows what is happening, and when. If, as is usual, you are not moving far, and are taking all your staff with you, draw them into the setting of the dates, before things get set. Apart from being good labour relations policy, this has unexpected benefits. A lowly storeman once told me that the electricity board needed three months' notice if we were not to go on paying the standing charges after we had gone. That caused us to think about the telephones, water and gas, all of which had been left out of the planning.
If you are not taking all the staff, do make sure that you get the right advice on how to handle redundancy; mistakes in this area are very expensive. Don't wait until you arrive before hiring staff: it is worth having a double complement of staff for a short time, as you can start some work at the new site before you have left the old one.
One of your fixed days has to be the date at which no new work comes to your old location, but all goes to the new one — even if it does have to wait a bit. Do not compromise on this one as it can throw all the carefully laid plans. In some large fleets, there is often a number of vehicles simply awaiting collection from far-flung users. Keep this number to the minimum, but include them in your plan. It may be an aggravation, but when you are clear of the old site, there must be no left-overs or there is the chance of theft.
The setting of the dates and the communication of them to all parties can best be done in a simple calendar of events style. Do not bury it all in a long and rambling letter. One of the most effective ways of setting this out, if you can stand the jokes that may be made at your expense, is the old military style of D day. D minus 90 may be when you give notice to those not moving. D plus 14 may be the last day anyone is in the old site and so on. It may be old soldier stuff, but it works, and is easy to understand at all levels.
All this activity assumes that the plans for the layout of the new site were completed to your satisfaction, and that no significant hold-ups occur, but be prepared for the discovery that what looked good on paper, does not look so good on the ground. Waste no time in changing anything in this category at once — before you lay a single spanner on anything. Things you decide you can put up with "just for a while" tend to last for ever. Strike while you still have something in the budget. It should be labelled "contingencies" if the budget for the move has been done properly.
If all this seems to much for you, you can always get the whole move planned, executed and supervised by consultants — a so-called turnkey project. This is certainly one of the best ways of planning the building and fitting out of a site, and can easily be extended into the planning of the move. You need a firm that specialises in project management. There are a lot of them, but one whose work is typical is Edmund Shipway and Partners who are quantity surveyors.
Shipway's project management team were responsible for a highly prestige workshop development in Kingston on Thames for BMW agent Cooper Thames Ditton. Various alternative solutions for a new workshop were put forward including cost plans and feasibility studies. Edmund Shipway managed the whole project including evaluating tenders for environmental services contractors.
The result pleased both company and customers and is an object lesson in successful planning. There is even enough parking room, which for a car workshop is close to unique.
Another aid that you might consider is a computerised system for design and planning of buildings such as warehouses and
for distribution systems. One of the latest is AWARD, a computer-aided design technique which includes interactive simulation to evaluate many complex options that could otherwise take days of work. It is marketed by Synergy Distribution Systems.
At the other end of the help scale, many suppliers of equipment will help you with installation and siting problems. If buying, ask if they have a design and layout service. Many do, but for some reason don't shout about it. If in doubt, approach your trade organisation, such as the ETA. One supplier of bulk tanks, Joseph Ash & Son has such a service as will supply, install and advise on the best location of the products and associated services, such as pipework.
It can all be done on the back of an envelope of course, and has been. But if you are not to risk getting in to a dreadful mess, it pays to make good plans, even if you have to pay someone to do it Edmund Shipway and Partners Turbo 72 Synergy Distribution Systems Turbo 73 Joseph Ash and Sons Turbo 74