Special versions of new Atkinson twin-steer tractive unit carry load
Page 58
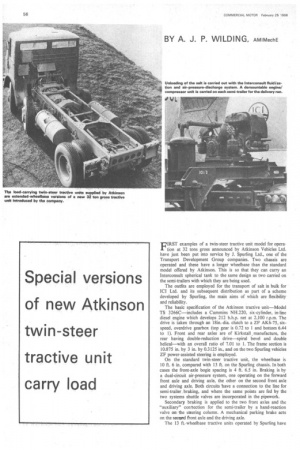
Page 59
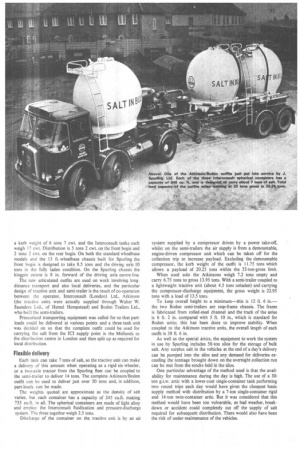
If you've noticed an error in this article please click here to report it so we can fix it.
BY A. J. P. WILDING, AMIMechE
VIRST examples of a twin-steer tractive unit model for opera
non at 32 tons gross announced by Atkinson Vehicles Ltd. have just been put into service by J. Spurling Ltd., one of the Transport Development Group companies. Two chassis are operated and these have a longer wheelbase than the standard model offered by Atkinson. This is so that they can carry an Interconsult spherical tank to the same design as two carried on the semi-trailers with which they are being used.
The outfits are employed for the transport of salt in bulk for ICI Ltd. and its subsequent distribution as part of a scheme developed by Spurling, the main aims of which are flexibility and reliability.
The basic specification of the Atkinson tractive unit—Model TS 3266C—includes a Cummins NH.220, six-cylinder, in-line diesel engine which develops 212 b.h.p. net at 2,100 r.p.m. The drive is taken through an 18in.-dia. clutch to a ZF AK6-75, sixspeed, overdrive gearbox (top gear is 0.72 to 1 and bottom 6.44 to I). Front and rear axles are of Kirkstall manufacture, the rear having double-reduction drive—spiral bevel and double helical—with an overall ratio of 7.01 to I. The frame section is 10.875 in. by 3 in. by 0.3125 in., and on the two Spurling vehicles ZF power-assisted steering is employed.
On the standard twin-steer tractive unit, the wheelbase is 10 ft. 6 in. compared with 13 ft. on the Spurling chassis. In both cases the front-axle bogie spacing is 4 ft. 6.5 in. Braking is by a dual-circuit air-pressure system, one operating on the forward front axle and driving axle, the other on the second front axle and driving axle. Both circuits have a connection to the line for semi-trailer, braking, and where the same points are fed by the two systems shuttle valves are incorporated in the pipework.
Secondary braking is applied to the two front axles and the "auxiliary" cornection for the semi-trailer by a hand-reaction valve on the steering column. A mechanical parking brake acts on the second front axle and the driving axle.
The 13 ft.-wheelbase tractive units operated by Spurting have a kerb weight of 6 tons 7 cwt. and the Interconsult tanks each weigh 17 cwt. Distribution is 5 tons 2 cwt. on the front bogie and 2 tons 2 cwt. on the rear bogie. On both the standard wheelbase models and the 13 ft-wheelbase chassis built for Spurting the front bogie is designed to take 8.5 tons and the driving axle 10 • tons in the fully laden condition. On the Spurling chassis the kingpin centre is 8 in. forward of the driving axle centre-line.
The new articulated outfits are used on work involving longdistance transport and also local deliveries, and the particular design of tractive unit and semi-trailer is the result of co-operation between the operator, Interconsult (London) Ltd., Atkinson (the tractive units were actually supplied through Walter W. Saunders Ltd., of Hemel Hempstead) and Boden Trailers Ltd., who built the semi-trailers.
Pressurized transporting equipment was called for so that partloads could be delivered at various points and a three-tank unit was decided on so that the complete outfit could be used for carrying the salt from the ICI supply point in the Midlands to the distribution centre in London and then split up as required for local distribution.
Flexible delivery
Each tank can take 7 tons of salt, so the tractive unit can make a delivery of this amount when operating as a rigid six wheeler, or a two-axle tractor from the Spurling fleet can be coupled to the semi-trailer to deliver 14 tons. The complete Atkinson/Boden outfit can be used to deliver just over 20 tons and, in addition, part-loads can be made.
The weights quoted are approximate as the density of salt varies, but each container has a capacity of 245 cu.ft. making 735 cu.ft. in all. The spherical containers are made of light alloy and employ the Interconsult fluidization and pressure-discharge system. The three together weigh 2.5 tons.
Discharge of the container on the tractive unit is by an air
system supplied by a compressor driven by a power take-off, whilst on the semi-trailers the air supply is front a demountable, engine-driven compressor unit which can be .taken off for the collection trip to increase payload. Excluding the demountable compressor, the kerb weight of the outfit is 11.75 tons which allows a payload of 20.25 tons within the 32-ton-gross limit.
When used solo the Atkinsons weigh 7.2 tons empty and carry 6.75 tons to gross 13.95 tons. With a semi-trailer coupled to a lightweight tractive unit (about 4.5 tons unladen) and carrying• the compressor-discharge equipinent, the gross weight is 22.95 tons with a load of 13.5 tons.
To keep overall height to a minimum---this is 12 ft. 6 in.— the two Boden semi-trailers are step-frame chassis. The frame is fabricated from rolled-steel channel and the track of the axles is 6 ft. 2 in. compared with 5 ft, 10 in., which is standard for Boden units; this has been done to improve stability. When coupled to the Atkinson tractive units, the overall length of each outfit is 38 ft. 6 in.
As well as the special artics, the equipment to work the system in use by Spurlitig includes 56-ton silos for the storage of bulk salt. Any surplus salt in the vehicles at the end Of a day's delivery can be pumped into the silos and any demand for deliveries exceeding the tonnage brought down on the overnight collection run can be met from the stocks held in the Silos.
One particular advantage of the method used is that theavailability for maintenance during the day is high. The use of a 30ton g.t.w. artic with a lower-cost single-container tank performing two round trips each day would have given the cheapest basic supply method with distribution by a 7-ton single-container rigid and 14-ton twin-container am-tic. But it was considered that this method would have been Inc vulnerable, as bad weather, breakdown or accident could completely cut off the supply of salt required for subsequent distribution. There would also have been the risk of under-maintenance of the vehicles.