Hydraulic Drive for Cement Mixer
Page 38
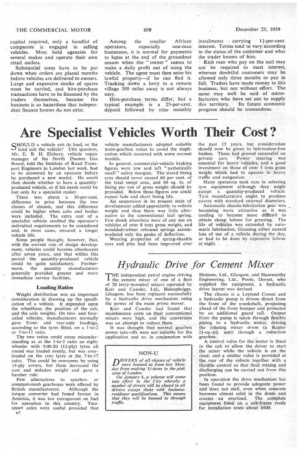
If you've noticed an error in this article please click here to report it so we can fix it.
THE independent petrol engine driving the cement mixer of one of a fleet of 20 lorry-mounted mixers operated by Keir and Cawder, Ltd., Bishopbriggs, Glasgow, has been replaced successfully by a hydraulic drive mechanism using the power of the main prime mover.
Keir and Cawder had found that maintenance costs on their conventional mixers were high, and the conversion was an attempt to reduce them.
It was thought that normal gearbox power take-offs were not suitable for the application and so, in conjunction with Hutsons, Ltd.. Glasgow, and Hamworthy Engineering, Ltd., Poole, Dorset, who supplied the equipment, a hydraulic drive layout was devised.
The chassis is a Leyland Comet and a hydraulic pump is driven direct from the front of the crankshaft, projecting ahead of the front bumper and protected by an additional guard rail. Output from the pump is taken through flexible piping to a hydraulic motor, driving the rotating mixer drum (a Rapier 24-cu.-yd. unit) through a reduction gearbox.
A control valve for the motor is fitted in the cab to allow the driver to start the mixer while the vehicle is on the road, and a similar valve is provided at the rear of the vehicle together with a throttle control so that final mixing and discharging can be carried out from this position.
In operation the drive mechanism has been found to provide adequate power and does not stall, even when concrete becomesalmost solid in the drum and
creates • an overload. The complete equipment fitted on a sub-frame ready for installation costs about £600.